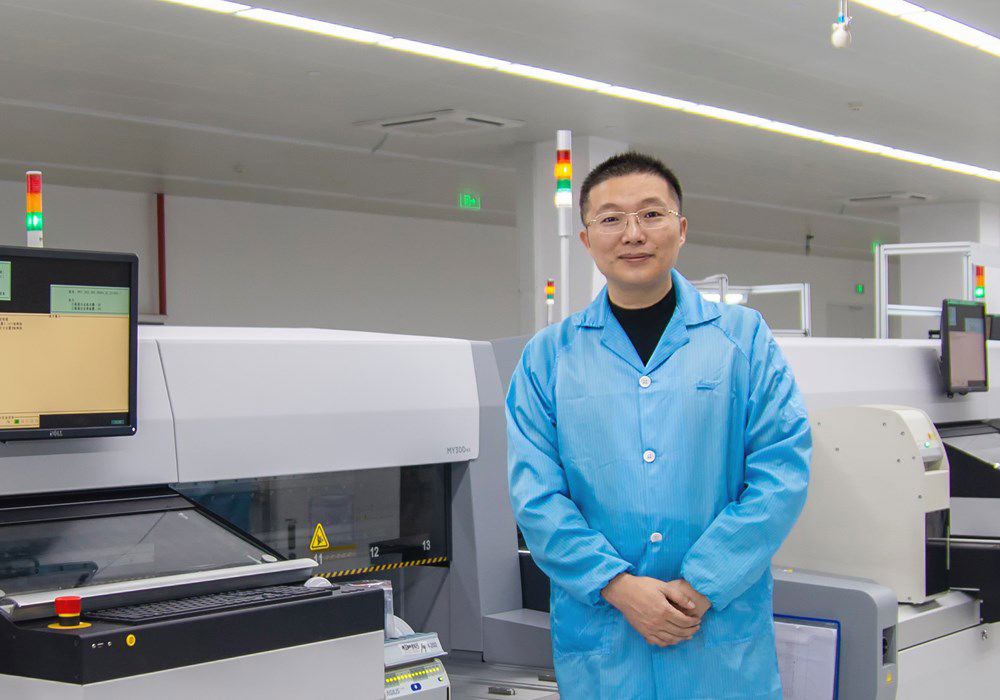
Thinking outside the line
How Wuxi Good Electronics is pushing the frontiers of flexible assembly
Mr. Liu Haifeng has never been one to stick with the status quo. As General Manager of Wuxi Good Electronics Co., Ltd., he is always on the hunt for the latest production technologies, new manufacturing concepts and better ways to serve his customers. The company’s current production setup shows just how far the right technologies – and an innovative mind – can push flexible assembly into new frontiers.
Enter the world of a manufacturing pioneer
Step into Wuxi Good Electronics today and you’ll see a highly agile production environment configured specifically to handle the variety and quality of some of China’s most advanced electronics assemblies. This is an environment built to handle more than 10,000 types of high-value components, where any assembly might be the first of its kind, and where excess material and board defects are simply not accepted. It’s no coincidence, then, that the world’s first 5G motherboard prototype was produced here more than a decade ago – a testament to the company’s reputation for pioneering groundbreaking technologies.
From the very beginning, Wuxi Good Electronics was set up specifically to cater to the prototyping needs of China’s fast-growing high-tech industries. This made Mycronic a perfect fit, largely due to the ability of its pick-and-place equipment to handle all types of tape-strip components with automatic feeder recognition. “About one-third of our production batches are a single board, and another third consists of small prototype batches of two to five boards,” explains Liu Haifeng. “This is really our niche: to help accelerate our customers’ R&D by producing their prototypes as fast as possible, without sacrificing quality. We recognized years ago that Mycronic shared this focus, and our partnership has really paid off with a significant increase in prototype orders from the very start.”
Expanding the concept of flexibility
Like many of the products it manufactures, the factory’s setup is one-of-a-kind. Alongside a more conventional line for series production, one machine in particular stands out: the PCB buffer tower, a customized, multi-track intelligent board conveying system. From here, all bare boards entering the factory are automatically registered and conveyed – via the screen printer, Mycronic jet printer and SPI – to the most efficient of five independent pick-and-place machines.
Depending on the actual product and the completeness of the material preparation, five different products from the PCB buffer tower might be routed to five different MY200 and MY300 pick-and-place machines simultaneously. For another product, two or more machines might combine in-line to complete a single assembly. In either case, the machines automatically identify all online materials, making the best use of the flexibility and production efficiency of each piece of equipment.
More components, less work
Because a single MY300 can accommodate and process more than 200 kinds of bulk and odd-shaped components at a time, the handling of short-tape and unpackaged components has been vastly simplified. “The ability to handle small pieces of reels or tapes, and the freedom to place the feeder in any free position, is absolutely essential to our flexibility,” says Liu Haifeng. “The Agilis feeders make it so easy, with no maintenance or calibration required. And because packaged materials can be loaded offline, without an operator on the line to carry out online editing and confirmation, the MY300 has improved our work efficiency for an extremely wide range of materials.”
Finally, alongside the higher-volume production line, two MYTower component storage systems are combined into an intelligent material handling solution, to ensure easy access and proactive replenishment. Initially, Mr. Liu motivated the investment by his ambition to assure customers that their material would be handled with the industry’s highest standards, including strict access security, comprehensive traceability and state-of-the-art environmental controls. Over time, however, the towers have delivered on another promise: a significant increase in labor efficiency. “The intelligence of the material handling systems, together with the flexibility of the jetting and placement systems, has helped us double the number of changeovers we can handle with the same production staff,” says Liu Haifeng. Similar gains have been achieved in the kitting area, where just one operator performs a job that once occupied as many as three full-time staff.
An overview of an innovator
Company:
Wuxi Good Electronics Co., Ltd.
Location:
Wuxi, China
Profile:
High-tech manufacturer of small-batch, high-reliability electronics (IPC Class 3 or higher)
Mycronic products:
Mycronic customer since 2011, now with production including jet printing technology, flexible pick-and-place equipment and automated component storage solutions from Mycronic
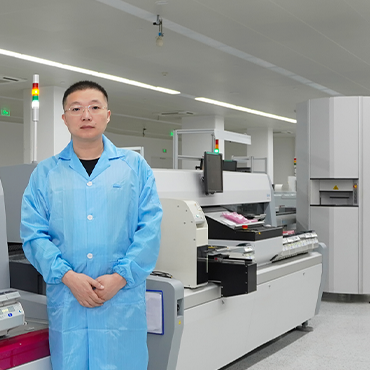
Faster programming, better quality
Of course, in the challenging world of rapid prototyping, experienced operators remain essential to high productivity. For particularly difficult components, operators utilize an assisted mount feature, which allows them to guide the pick-and-place machine for a particular component placement, thereby avoiding the full vision programming process. By enabling low-force control, for example when mounting thin and sensitive components, this process has also enabled production staff to virtually eliminate lead re-soldering.
Proving the shortest distance isn’t a single line
Along with all these quality and efficiency gains is an extremely high level of production flexibility. From batch-size-one prototype, to small-batch production through to series of hundreds of boards, the entire system is programmed to dynamically adapt, allocate production and combine pick-and-place capacity from the second the first bare board is scanned.
"Our high-flexibility production line layout has truly realized the rapid switching of small batches and multiple varieties,” explains Liu Haifeng. “It’s solved the stubborn problem of low production line utilization, and it’s greatly improved our production capacity and efficiency. It involved a lot of hard work, but this non-linear combination of five pick-and-place machines has really improved our equipment utilization and reduced the input cost of the production line.”
As a result of the company’s strength in rapid prototyping, Liu Haifeng’s team is seeing increasing integration with the customer’s R&D teams. To support this development, a design-for-manufacturing (DFM) system was recently connected to the Mycronic equipment and MYCenter software. “We continue to make progress in reducing the reserve cycle for our customers,” says Liu Haifeng. “We can do more changeovers and get more output, so that customers can now get their prototype while they’re waiting at the factory. We like to say that we do ‘prototypes-to-go’,” he says with a smile.
Partnership for the future
“A lot of this success is due to the great collaboration between ourselves and Mycronic,” he continues. “We share similar ambitions, we learn together, and their salespeople and application engineers are all familiar with our business. I consider the local Mycronic team as my colleagues since the interaction and communication have been so great. Now, as long as we stay focused on our niche business and move forward together, it doesn’t matter what our higher-volume competitors do.”