Building Complex Hybrid Circuits-Advanced Packaging
Complex Hybrid Circuits are used in a variety of high reliability applications including military, aerospace, medical, and photonics. MRSI offers dispense and die bonding solutions specifically geared to these challenging applications.
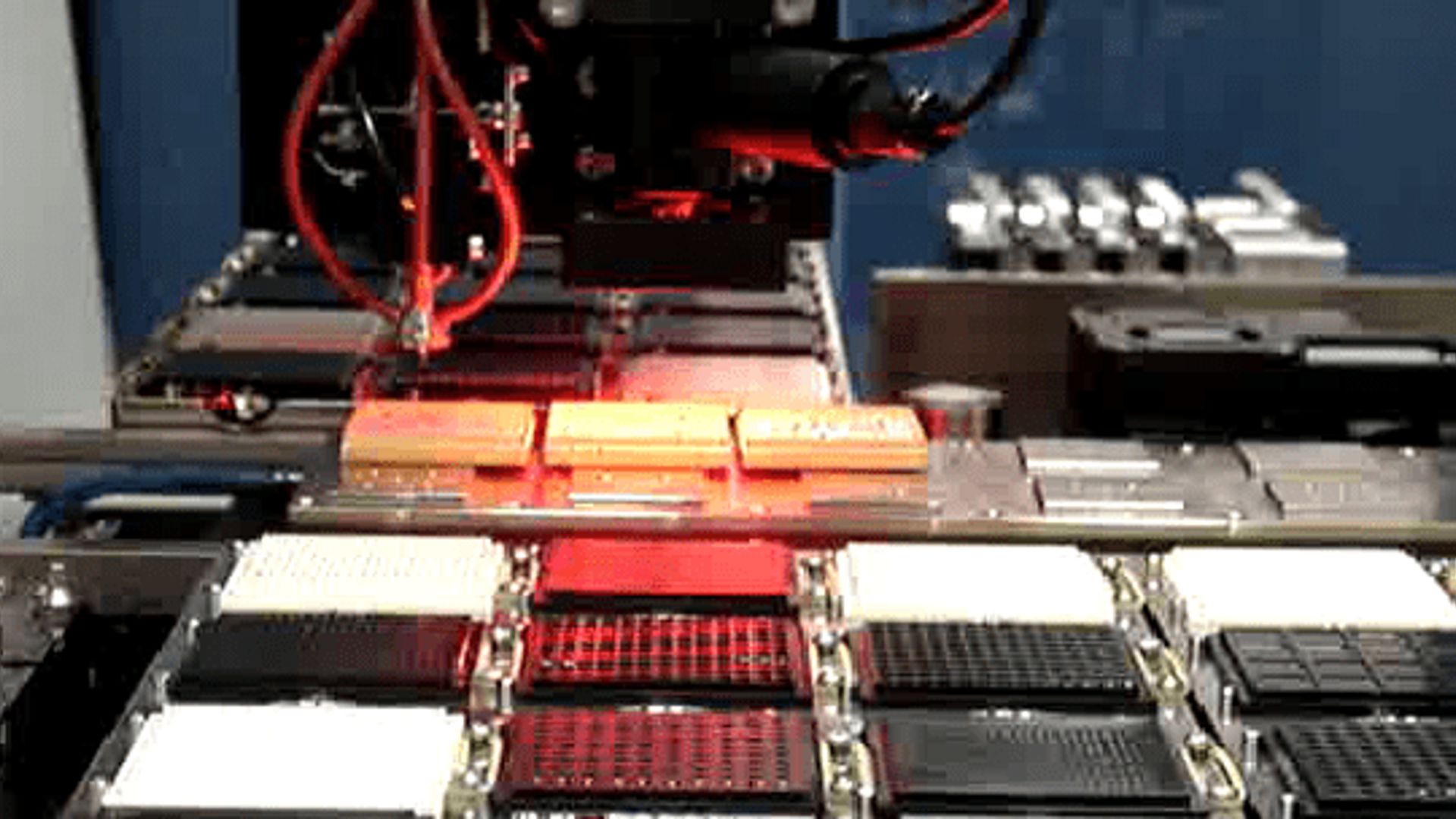
MRSI-705 5 Micron Die Bonder
The MRSI-705, 5-Micron Die Bonder sets the mark for high-precision, high-speed component assembly. Engineered for manufacturing robustness, the MRSI-705 die bonder is a flexible configurable platform, with the largest installed base in the industry for advanced packaging. Applications are found across a wide range of market segments, such as life & health sciences, aerospace, defense, automotive, lighting, communications, and more.
The MRSI-705 die bonder is built to meet the highest standards of reliability and dependability. It starts with an award-winning, industry standard platform with a day-in/day-out accuracy of ±5 microns and flexibility achieved by leveraging the die bonder platform’s signature features:
- Large Work Area – The unique overhead gantry design of the MRSI-705 translates into a large work area that easily accommodates a wide variety of material inputs and outputs.
- The die bonder can pick from any combination of Gel-Paks®, waffle packs, wafers, and tape feeders.
- Advanced Vision System – The die bonder’s advanced vision system enables rapid detection and orientation of die over a full 360° and the vision system aligns and places die according to substrate fiducials, the die edge, or relative to features of previously-placed die.
- Traceability – The MRSI family of high precision die bonders includes software to track material as the products are assembled.
- Tri-color (red, green, and blue) stadium lighting is combined with a collimated light source to enable the processing of the widest range of die, substrates and packages.
- Material Handling – Tooling is modular, ensuring fast, easy change-over between production runs.
- Force Control – Force control on the MRSI die bonders is the result of years of evolution and is the benchmark in the industry today. Proprietary force control algorithms allow faster placements without force overshoot. This applies at forces as low as 10 grams and as high as 2kg.
- MRSI Systems Windows Software intuitive graphical user interface, running on Windows™ simplifies the set-up and production process. The user interface is common to all MRSI die bonders and epoxy dispensers.
Business Outcomes For Our Customers
Since the MRSI-705 was first introduced in 2012, combining all of these features into one system, the following compelling business outcomes have been consistently achieved for our customers:
- Strongest ROIs in the industry– A well-established platform with an unmatched Cost of Ownership, increasing the overall production efficiency of product lines
- Proven Manufacturing Readiness– A work horse with minimum downtime and compelling reliability.
- Configurable Asset– The open platform adapts to changing portfolios and can handle complex multi-chip modules and other advanced assembly challenges with ease.
- Extended Machine Lifetime– The total cost of ownership is driven by the exceptional performance of the system over time with upgrade paths available as new features are introduced.
MRSI-175Ag Epoxy Dispenser
The MRSI-175Ag Epoxy Dispenser handles the most demanding dispensing applications such as microwave modules, optical modules, hybrid circuits, multichip modules, and semiconductor packaging. Two dispense heads. These heads can be used for two dispense pumps one dispense pump and one stamping head.
The MRSI-175Ag Epoxy Dispenser offers a wide variety of application specific features:
- Rotary positive displacement auger pump, Time/Pressure dispense pumps, Jetting Pumps or Stamping Heads.
- Advanced Vision System combined with programmable tri-color lighting assures accurate fiducial registration for precise placement of dispensed patterns.
- Laser height sensing maintains critical dispense heights.
- Automatic tip calibration and Tip Cleaning.
- Material Handling – Tooling is modular, ensuring fast, easy change-over between production runs.
- MRSI Systems Windows Software The MRSI-175Ag’s intuitive graphical user interface, running on Windows™ simplifies the set-up and production process. The user interface is common to all MRSI machines.
Business Outcomes For Our Customers
Again, because all of these features are combined in an advanced dispensing system, this equates to significant operational and financial benefits for our customers, including:
- Increase capacity at lower cost –Separating the dispensing process step from the placement operation translates into lower costs by leveraging both machine types for what they do best.
- Less Labor Cost –Automatic needle cleaning, automatic calibration routines mean less operator intervention and higher productivity.
- Higher Yields –High precision, automated process control functions, proven pump technology all come together to ensure maximum yields, which in turn translates into a lower cost per part.
- Flexibility –Handle whatever comes your way with the ability to use the right pump for the right application. Reconfigure if needed.
- Lower Cost of Ownership– Commonality with MRSI placement machines means lower spare parts cost, lower parts inventory, lower training costs.
Summary
MRSI Systems offers a variety of dispense and die bonding solutions. Contact MRSI to learn more about how we can address your specific application requirements.
About MRSI Systems
MRSI Systems is a leading manufacturer of fully automated, high-precision, high-speed die bonding and epoxy dispensing systems. We enable customers to optimize the performance of their process including yield, throughput, and uptime by building systems that use our unique expertise. In summary, this includes our proprietary software, proven hardware, deep process knowledge, state-of-the-art manufacturing, and a world-class customer service team. MRSI’s systems are built on common platforms that can be configured to meet specific customer requirements. These platforms are designed to be scalable for R&D prototyping, pilot production and high volume manufacturing. Our solutions deliver the best financial returns in the industry while integrating seamlessly into our customer’s production. Markets include Telecom/Datacom (Data Center), Aerospace & Defense, Medical Devices, Computers and Peripherals, and Industrial. Since 1984, we have been recognized as the standard of the industry, delivering our solutions to leading optoelectronic and microelectronic customers worldwide. We are headquartered in Billerica, MA in the greater Boston area. Our sales are supported by a global network of direct service and support professionals, located in China, Taiwan, Singapore, Korea, Thailand, Malaysia, the Philippines, Israel, Europe, United Kingdom, and the United States.