Epoxy Deposition – Requirement for High-Volume Manufacturing (HVM) of Chip-on-Submount (CoS)
Most die bonders offered today have evolved from their original objective of solving generic semiconductor packaging applications. While these semiconductor die bonders may be well-suited for the die bonding requirements of semiconductor packages, they lack the specific unique features required for successful HVM of CoS.
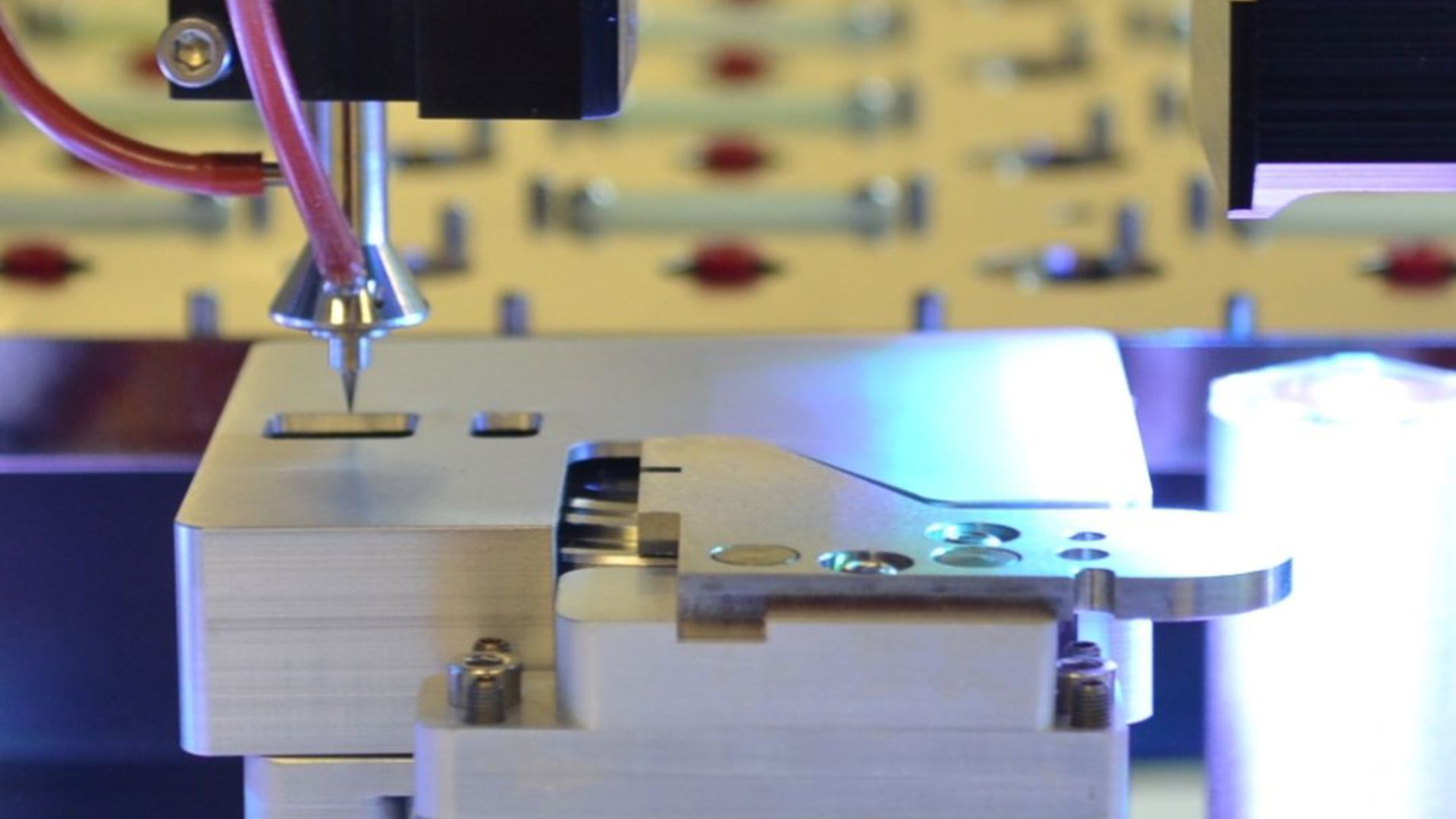
Customers require an application-specific specialized die bonder for HVM of CoS that is able to deliver high speeds while maintaining flexibility. This is best achieved with a standard, flexible, high-speed system that can be easily reprogrammed for new device designs and types, resulting in shorter delivery times for standardized machines, which allows customers to scale production rapidly. A HVM CoS die bonder should include many parallel processing features to maximize throughput. One of the unique requirements of a CoS-specific HVM die bonder is epoxy deposition.
Epoxy Deposition
CoS components are small and consequently require very small epoxy dots for successful epoxy die attach. Components, such as 200 micron laser diodes, require very small volumes of conductive epoxy with an exact dimension. Epoxy coverage with no voiding and controlled, thin bond lines is critical to maximize thermal transfer, ensure mechanical strength and minimize stresses. Squeeze-out must be controlled to prevent shorting or bridging, and epoxy must be placed in precise locations to maximize yield.
There are two basic methods for applying epoxy to accomplish the task described above. These include epoxy stamping (pin transfer or daubing), and syringe fluid dispensing. The selection of deposition method will largely depend upon the properties of the epoxy used and the minimum dot size required. Factors such as silver grain size, material viscosity, thixotropic index, and packaging methods will all influence the decision on the material deposition method. Often for CoS, the solution is epoxy stamping because the process requires dots smaller than 200 microns. Both alternatives are now examined in more detail.
Epoxy Stamping
Epoxy Stamping is used to create very small epoxy dots by touching down in epoxy at the epoxy stamping well and then transferring the material onto the substrate. Dot size is determined by the epoxy thickness at the epoxy stamping well and the epoxy stamping tool profile. In the epoxy stamping process, a reservoir of epoxy is presented in a grooved well. The epoxy stamping well is rotated so that the material is passed under an adjustable height wiper blade. The height of the wiper blade should be precision adjustable using a micrometer device. The rotating epoxy stamping well can have multiple grooves to accommodate multiple types of epoxy.
Epoxy Stamping does not have to be limited to the transfer of single dots. Gang-arrayed (multiple) epoxy stamping tools can be employed to transfer an array of dots simultaneously. These gang epoxy stamping tools have multiple points that place the same pattern of dots with each touchdown. This is useful for increased throughput and for precise control over the pattern in the epoxy stamping process.
Tool profile is another critical factor of epoxy stamping to consider. Tools can be designed with a spherical tip or a flat tip depending on the shape and size that is desired for the dot. When combined with good control of epoxy thickness in the well, the right epoxy stamping tool can produce repeatable dots of a very specific height and diameter.
Epoxy stamping is a technique frequently used to attain very small epoxy dots. Sometimes known as daubing or pin transfer, this technique relies on a compliant tool touching down in epoxy and transferring the material to another surface. The key parameters to control in epoxy stamping are thickness and tool profile.
In this process, epoxy is usually presented to a machine in a grooved epoxy stamping well. The epoxy stamping well is rotated such that the material is passed under a fixed height wiper blade located just before the touchdown point. The wiper blade ensures that the epoxy is the right thickness in the epoxy stamping well. The wiper blade height can be controlled via a micrometer, and the epoxy stamping well rotation can be stopped when a proximity sensor determines that the epoxy stamping tool is about to touch down. Tool profile is the second critical factor to consider in an epoxy stamping process. Tools can be designed with a spherical tip or a flat tip depending on the shape that is desired for the dot.
Epoxy stamping does not have to be limited to the transfer of single dots. Gang-arrayed (multiple) epoxy stamping tools can be employed to transfer an array of dots simultaneously. These tools have multiple tips that place the same pattern of dots with each touchdown. By employing a tool-changing bank with different epoxy stamping tools and various touchdown points in several grooves in the epoxy stamping well, multiple epoxies can be stamped without changing the setup.
Syringe Fluid Dispensing
Syringe fluid dispensing is an alternative to epoxy stamping and is used to apply epoxy when the parts are larger (typically greater than 0.25mm). The process typically includes high-resolution servo driven, positive displacement pumps, for the most accurate dispensing of dots, lines and areas. A precision time/pressure pump can also be used depending on the application, materials and process requirements. Material flow is enhanced by a chamfered design in the needles inside the wall, with the chamfering toward the needle tip. This reduces surface tension, provides for more precise control, and also reduces clogging.
Summary
HVM of CoS is an important and challenging problem requiring unique capabilities from the die bonding system. A HVM CoS die bonder should include many parallel processing features to maximize throughput. An application-specific standardized die bonder will deliver a flexible solution, which maximizes product yield, throughput, and process control, to ensure a successful solution for HVM of CoS. This approach also results in fast machine delivery times. Fast machine delivery times allow CoS manufacturers to scale production rapidly, to meet their market demands.