Trends, Challenges and Opportunities for High Volume Manufacturing of Photonic Devices for Data Center Applications
There are many challenges that photonic device suppliers are facing in the current market. As part of IEEE’s Tech Insider Webinar Series, MRSI Systems recently delivered a presentation on high volume manufacturing of photonic devices. The following post highlights some of the major points from that session.
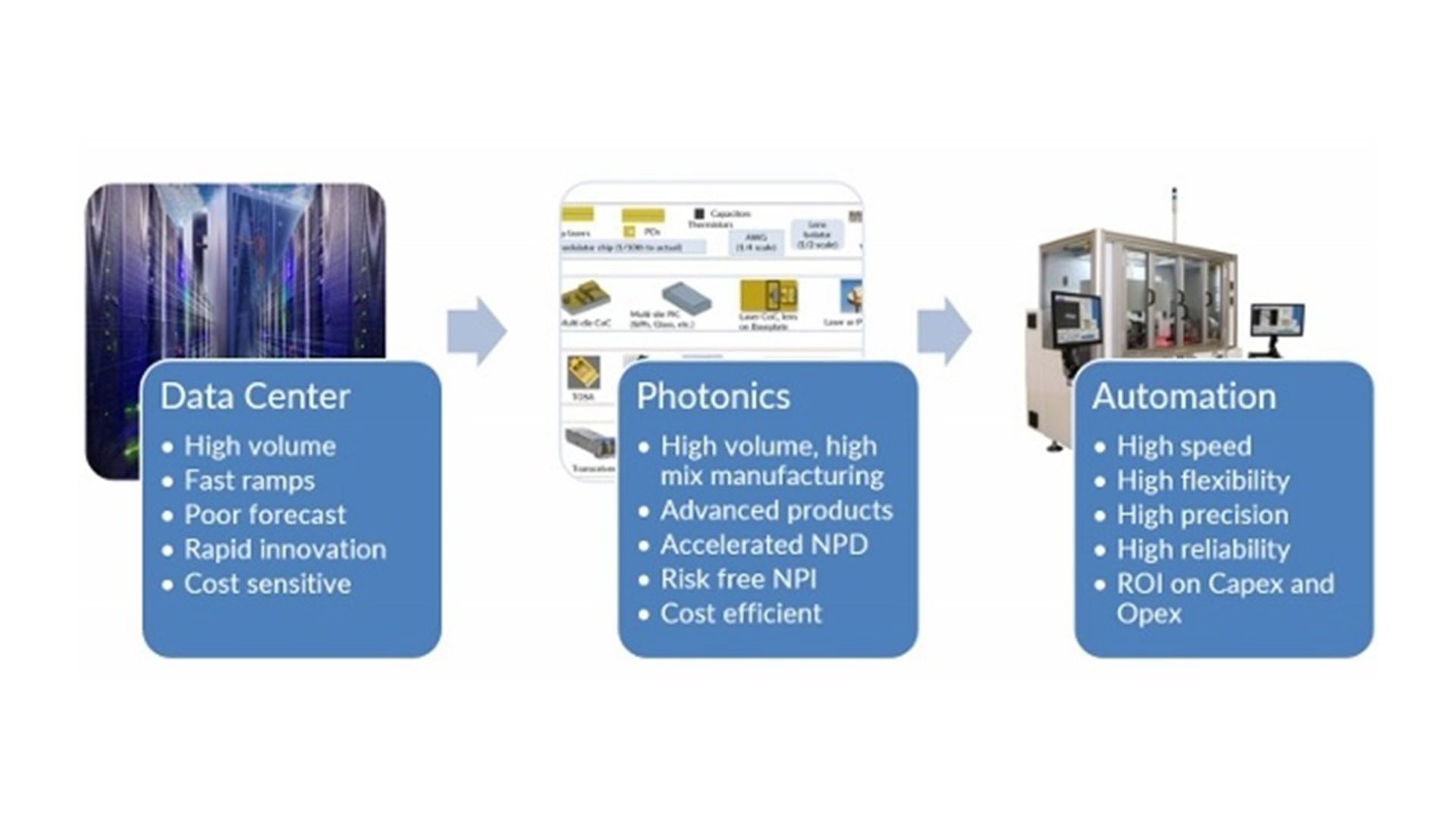
Trends
The high growth of internet usage and the proliferation of applications especially video streaming has been driving bandwidth demand for many years. As Cisco’s study shows, both global IP traffic and global data center traffic has been growing at a cumulative annual growth rate of around 25% for many years. The emerging applications, such as the Internet of Everything, driverless cars, data centers, and others are driving the continuous growth of bandwidth demand. At the core to support all of these applications and bandwidth demand is fiber optics and photonics. In particular, hyper scale data center’s just-in-time supply chain management model brings significant challenges and opportunities to photonic device suppliers.
Challenges for Photonic Device Suppliers
Given these trends there are significant challenges for photonic device suppliers.
- Need a reasonably large manufacturing base to handle the size of each order
- Can’t ramp fast enough for the short lead time when getting an order
- Can’t reduce labor cost fast enough when losing an order
- Contract Manufacturing model is sometimes challenged to respond due to capacity competition for the same projects from multiple photonics customers at one time
Response of Photonic Device Suppliers
In summary, this new environment demands that photonic device suppliers execute on the following priorities:
- “Elastic” capacity model for
a. High Quality, Low Cost manufacturing with Fast Switch on-and-off of capacity - More automation for R&D and Manufacturing
a. Lowers the dependence on labor to reduce variable cost (labor hiring, training, and retention)
b. Minimizes NPI risks by using the same automation platform and processes
Automation Improves Photonics Supplier’s Response to Data Center Demand
Opportunities
All of these challenges, driven by the new cloud-based data center business model, come with opportunities. Data Center applications provide the highest volume opportunity for photonics, which requires fast ramp and full volume delivery. However, it provides relatively poor visibility for demand forecasting due to the nature of the project-based demand model. This requires rapid innovation to match this upgrade plan, which occurs every three to five years; and, it is extremely cost sensitive. So, the challenge for photonics manufacturers is really the need to provide high mix manufacturing capacity with high throughput.
Case Study— Photonics HVM Requirements— High Speed Die Bonding without Sacrificing Flexibility or Precision
- Photonics HVM needs high speed equipment to be flexible and precise
- Photonics HVM needs high precision for higher yield and more complex products
- Current photonics HVM tightens front end (e.g. CoC) packaging tolerance to have better yield in later packaging steps to reduce total assembly cost
- Next generation photonic packaging designs require 3 micron die bonding precision
- Some of silicon photonics assembly steps need 3 micron die bonding precision to work with self-alignment mechanics built on parts using semiconductor nanofabrication in order to achieve submicron post-processing accuracy
MRSI-HVM3 die bonding system’s speed is the fastest in class for photonic CoC HVM, without sacrificing precision or flexibility, realized by optimizing the following assembly steps.
- “On-the-fly” tool change
- Parallel material handling and final bonding steps using dual head/gantry/stage
- Ultrafast temperature ramping & cooling of eutectic hot stage
MRSI-HVM3 die bonding system provides future-proof assembly with ±3µm@3s die bonding precision, built based upon long proven MRSI-M3 die bonding system (±3µm@3s)
Contact MRSI Systems to learn more about our MRSI-HVM3 high speed die bonding system.