More growth, less pain
How one Silicon Valley company is accelerating the design-to-manufacturing cycleFounded 13 years ago in Silicon Valley as an engineering consulting firm, NVZN Labs has quickly evolved into a full-stack design and manufacturing company, specializing in industrial machines and cutting-edge technologies. As their client base and production volumes have expanded, Mycronic equipment has played a central role in the quality, flexibility and production scalability that the company is able to provide.
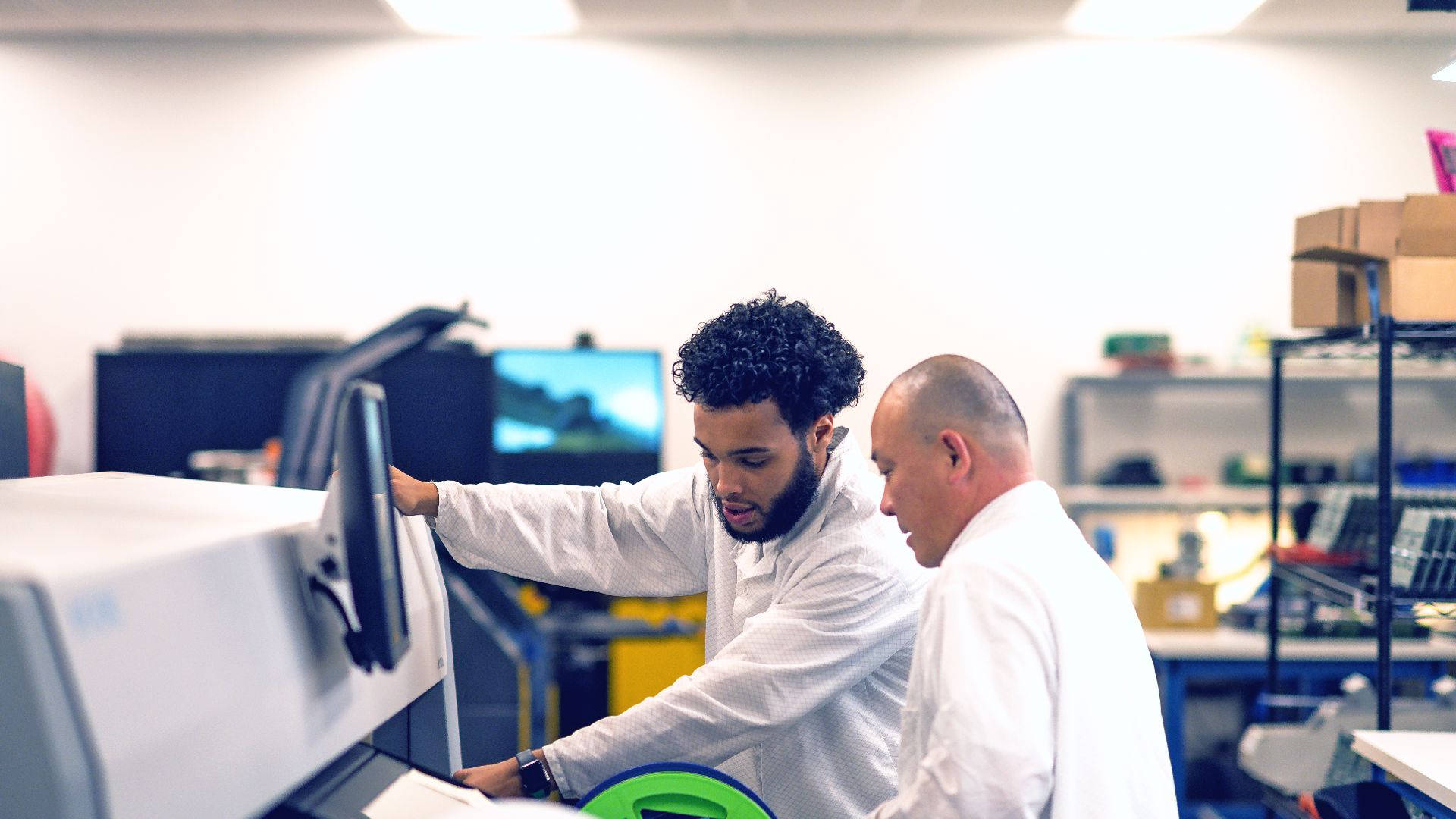
A launchpad for new products
If there’s one thing that all NVZN Labs’ customers have in common, it’s an ambition to design, launch and deliver new products at scale. But when it comes to state-of-the-art electronics, this is much easier said than done. “A good example is a customer that came to us about a year ago,” says NVZN Labs founder and CEO Collin Stoner. “They needed a prototype run of 25 pieces, a demo product to sell into their management and strategic partners, and they needed it fast. So, we had to spin out a functional product in a week and a half, including custom boards and housing. This kind of job would be impossible if you had to order parts, so we’re really dedicated to streamlining everything in-house.”
Investing in agile manufacturing
In its early years, NVZN Labs primarily focused on designing and consulting for clients, providing end-to-end solutions encompassing hardware, circuit boards, layout, programming and test verification. As demand for their services grew rapidly, the company invested in production equipment including advanced CNC machines, 3D printing equipment, a MY600 jet printer, MY300 pick-and-place machine and a MYPro I series 3D AOI system.
Today, they create a diverse array of products ranging from medical devices and night vision technologies to industrial instrumentation, aerospace flight computers,
automotive manufacturing control systems and scientific instrumentation. And with every new client success comes a higher demand for manufacturing output.
“Nowadays, we’re getting more and more customers who are just ready to go into production,” explains Collin, “and they might need nine or ten thousand boards. In these cases, we do a lot of the parts of the product, including manufacturing, inspection and test for pretty much any board. Then there’s CNC machining, 3D printing and so on for the mechanical enclosures. When you’re producing the entire product like this, managing quality becomes critical — especially as you go to
volume.”
To integrate circuit board manufacturing into their product delivery services, NVZN Labs had evaluated various PCB assembly equipment options. Among the contenders, Mycronic stood out due to its flexibility in high-mix production. “I generally want to have the absolute best equipment for the job,” says Collin. “For example, you can get by with a 3-axis CNC machine, but ours is 5-axis because it’s
just better. The same is true for our PCB assembly equipment.”
Flexible jetting and component placement
Screen printing, although a reliable technique, was deemed to be simply too wasteful when working on projects involving a variety of board quantities. To address this challenge, NVZN Labs adopted the MYPro MY600 Jet Printer, which
offered greater flexibility, accuracy and efficiency. The MY600 allowed them to minimize errors and make rapid solder paste adjustments when finetuning the designs of prototype boards.
“The jet printer has been great for us, since we seem to have a lot of weird parts that can be hard to catch the first time around,” says Collin. “So, after the pick-and-place or after testing in reflow, we can go back, adjust the paste deposits and inspect it. We can change the paste settings in about five minutes, and we do it all the time.”
Similarly, the choice of a MY300 pick-and-place solution was motivated by a need for fast, flexible changeovers in an environment with complex flows of high-value components. “When it comes to the pick-and-place process,” adds Collin, “the Agilis feeders have added enormously to our flexibility. We integrated our ERP system straight into the MY300, so we know where every component is and can easily change jobs at any time.”
Scaling up process quality
The most recent addition to the company’s production line is the MYPro I series 3D AOI inspection system. Having previously relied on manual inspection, production staff began to encounter quality issues as they scaled up production into batch sizes numbering in the thousands. Coplanarity issues, misaligned placements and soldering problems, all of which were difficult to detect manually, resulted in
the need for a comprehensive 3D AOI inspection system.
The implementation of the MYPro I series has had a transformative effect on the company’s manufacturing quality and efficiency. By detecting defects earlier
in the production process, they have achieved a substantial reduction in errors identified during final visual inspections. In addition, the ability to catch defects promptly and make necessary corrections inline has significantly streamlined the production team’s daily workflow.
“It’s drastically improved both our profitability and product quality,” says Collin. “We’ve reduced errors found by visual inspection by more than 90 percent,
and coplanarity errors caught by visual inspection have been completely eliminated.”
In terms of cost savings, Collin estimates that the new AOI system has saved several hours per job in manual inspection and post-SMT repair alone. “A typical prototype run for us is 25–50 units of large, complex boards,” he explains. “Even with programming time, we save hours on each job over manual inspection and repair after SMT versus immediate inline detection with the AOI and correction for the following boards. With our labor rate, this can be $200–250 per production run of opportunity costs saved, both in direct (manual) inspection time and repairing defects that weren’t caught until after SMT is finished, because visual inspection happens too slowly to make inline corrections.
Easy programming, better inspection models
As a new user of advanced 3D inspection systems, Collin was especially surprised by how quickly the new solution could be brought online. “We had an operator who was untrained on AOI,” he explains, “but he only needed about a week and a half of
training. Now, he can generate programs in about an hour and a half to get us up and running very quickly. The speed of this training cycle was quite a bit faster than expected.”
Even more time has been saved, says Collin, thanks to Escape Tracker, an automated inspection library optimization function designed to reduce false calls
with less operator intervention. Escape Tracker is used on every job that NVZN Labs runs through their system, consistently improving the inspection process and fine-tuning the inspection model with every board inspected.
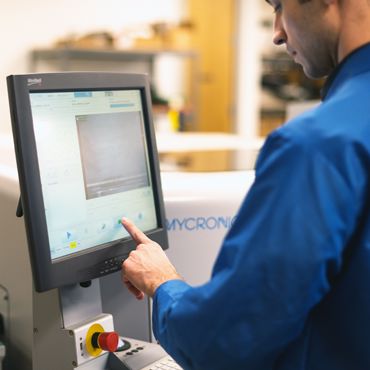
Leveraging the benefits of flexible production
Measured in business terms alone, the company’s investment in flexible, integrated design and manufacturing is clearly paying dividends. In addition to designing and launching successful products for dozens of Silicon Valley’s most innovative clients, NVZN Labs is on track to achieve its third straight year of double-digit growth.
But in an unpredictable world, the benefits of flexibility have also emerged in other, more surprising ways. “Just look at the supply chain disruptions over the past few years,” reflects Collin. “If you had to rely on a certain component or a certain contract manufacturer, you could easily be waiting months to get your product out the door! Instead, we’ve focused on our in-house capabilities — simplifying designs, using interchangeable families of components and maintaining multiple footprints for added flexibility.
So whether it’s a new prototype or a full manufacturing run, we’ve got the engineering capabilities to respond on-the-fly, and our Mycronic equipment has been a big part of this strategy.”