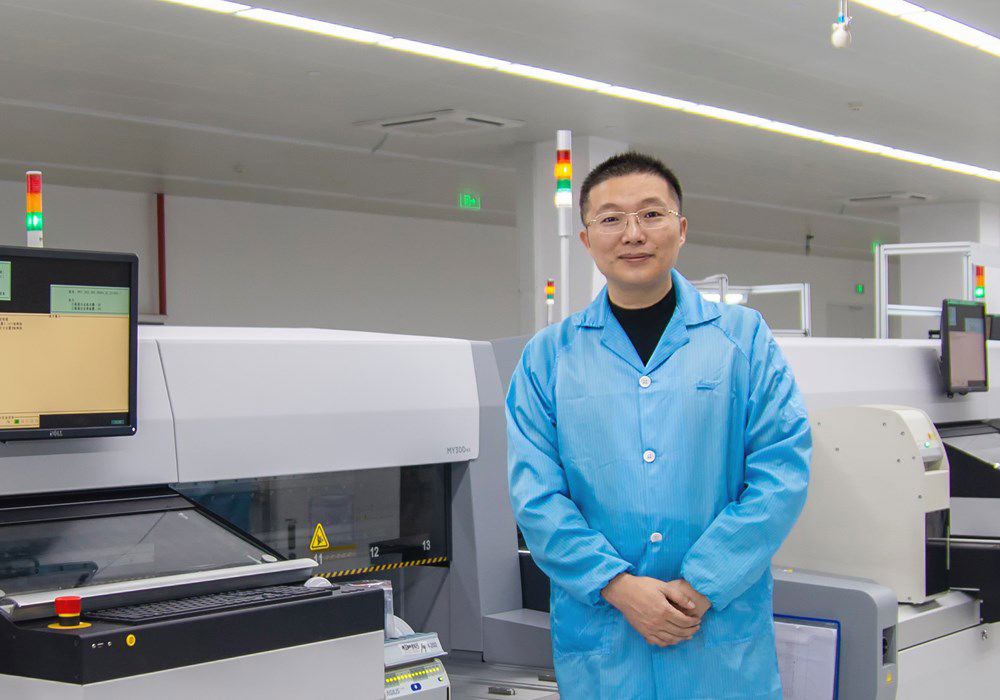
Voir au-delà de la ligne de production
Comment Wuxi Good Electronics repousse les frontières de la flexibilité
M. Liu Haifeng n’a jamais été du genre à contenter du statu quo. En tant que Directeur Général de Wuxi Good Electronics Co., il est toujours à la recherche des dernières technologies de fabrication, de nouveaux concepts de production et des meilleures façons de servir ses clients. La configuration de la production actuelle de l'entreprise montre à quel point les bonnes technologies – et un esprit innovant – peuvent emmener l'assemblage CMS vers de nouveaux horizons de flexibilité.
Entrez dans le monde d’un pionnier de la fabrication
Si vous visitez les locaux de Wuxi Good Electronics aujourd’hui vous verrez un environnement de production hautement agile configuré spécifiquement pour gérer la variété et la qualité de certains des assemblages électroniques les plus avancés de Chine. Il s'agit d'un environnement conçu pour traiter plus de 10 000 types de composants de grande valeur, où chaque assemblage peut être le premier du genre, et où les excédents de matière et les défauts ne sont tout simplement pas acceptés. Ce n’est donc pas un hasard si le premier prototype de carte mère 5G au monde a été produit ici il y a plus de dix ans, ce qui témoigne de la réputation de l’entreprise en matière de technologies révolutionnaires.
Dès le début, Wuxi Good Electronics a été créée spécifiquement pour répondre aux besoins de prototypage des industries de haute technologie chinoises à croissance rapide. Cela a fait de Mycronic un choix tout désigné, en grande partie grâce à la capacité de son équipement de placement à gérer tous les types de composants livrés sur bande, avec reconnaissance automatique du feeder. « Environ un tiers de nos lots de production sont constitués d’une seule carte, et un autre tiers est constitué de petits lots prototypes de deux à cinq cartes », explique Liu Haifeng. « C’est vraiment notre créneau : aider à accélérer la R&D de nos clients en produisant leurs prototypes le plus rapidement possible, sans sacrifier la qualité. Nous avons reconnu il y a des années que Mycronic partageait cet objectif, et notre partenariat a vraiment porté ses fruits avec une augmentation significative des commandes de prototypes dès le début. »
Élargir le concept de flexibilité
Comme beaucoup de produits qu’elle fabrique, la configuration de l’usine est unique en son genre. Outre une ligne plus conventionnelle pour la production en série, une machine en particulier se distingue : la tour «buffer» de PCB, un système de transport de carte intelligent multi-piste personnalisé. De là, toutes les cartes nues entrant dans l’usine sont automatiquement enregistrées et acheminées – via la machine de sérigraphie, le jet printer Mycronic et la SPI – vers la plus efficace des cinq machines de placement indépendantes.
En fonction du produit et de l’avancement de la préparation des composants, cinq produits différents peuvent être acheminés simultanément depuis la tour buffer vers chacune des cinq machines de placement MY200 et MY300. Pour un autre produit, deux machines ou plus peuvent se combiner en ligne afin de compléter un seul assemblage. Dans les deux cas, les machines identifient automatiquement tous les matériaux en ligne, en tirant le meilleur parti de la flexibilité et de l’efficacité de production de chacun des équipements.
Plus de composants, moins de travail
Parce qu’une seule MY300 peut accueillir et traiter plus de 200 types de composants massifs et de forme irrégulière, la manipulation des composants en bande courte et non emballés a été considérablement simplifiée. « La capacité de manipuler de petits morceaux de bobines ou de rubans, et la liberté de placer le feeder dans n’importe quelle position libre, sont absolument essentielles à notre flexibilité », explique Liu Haifeng. « Les feeders Agilis facilitent les choses, sans entretien ni calibrage. Et parce que les composants emballés peuvent être chargés hors ligne, sans besoin de modification ni de confirmation sur la ligne, la MY300 a amélioré notre efficacité de travail pour une gamme extrêmement large de composants. »
Enfin, parallèlement à la ligne de production de plus grand volume, deux systèmes de stockage de composants MYTower sont combinés offrant une solution de manutention des composants intelligente, assurant un accès facile et un réapprovisionnement proactif. Initialement, M. Liu a motivé cet investissement par son ambition d’assurer aux clients que leurs composants seraient manipulés selon les normes les plus élevées de l’industrie, avec une sécurité d’accès stricte, une traçabilité complète et des contrôles environnementaux de pointe. Au fil du temps, cependant, les tours ont tenu une autre promesse : une augmentation significative de l’efficacité du travail. « L’intelligence des systèmes de manutention des composants, ainsi que la flexibilité des systèmes de jetting et de placement, nous ont permis de doubler le nombre de changements que nous pouvons gérer avec le même personnel de production », explique Liu Haifeng. Des gains similaires ont été réalisés dans le domaine du kitting, où un seul opérateur effectue une tâche qui occupait autrefois jusqu’à trois employés à temps plein.
Aperçu d’un innovateur
Entreprise :
Wuxi Good Electronics Co., Ltd.
Localisation :
Wuxi, Chine
Profil :
Fabricant d’électronique high-tech, prototype et petites séries, à hautement fiabilité (IPC Classe 3 ou supérieure)
Equipements Mycronic :
Client Mycronic depuis 2011, la production comprend désormais la technologie de jet printing, des équipement de pick-and-place flexibles, et des solutions de stockage automatisé des composants
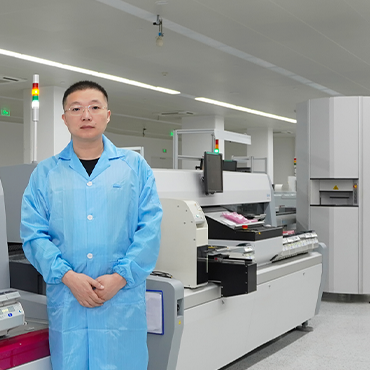
Programmation plus rapide, qualité supérieure
Bien entendu, dans le monde difficile du prototypage rapide, les opérateurs expérimentés restent essentiels à une productivité élevée. Pour les composants particulièrement difficiles, les opérateurs utilisent une fonction de montage assisté, qui leur permet de guider la machine de placement pour un placement de composant particulier, évitant ainsi le processus complet de programmation de la vision. En permettant un contrôle à faible force, par exemple lors du montage de composants minces et sensibles, ce processus a également permis au personnel de production d’éliminer pratiquement la ressoudure au plomb.
Prouver que la distance la plus courte n’est pas une simple ligne
Avec tous ces gains de qualité et d’efficacité, il y a un niveau extrêmement élevé de flexibilité de production. Du prototype de la taille d’un lot à la production en petits lots en passant par une série de centaines de cartes, l’ensemble du système est programmé pour s’adapter dynamiquement, allouer la production et combiner la capacité de placement dès la seconde où la première carte nue est numérisée.
« La grande flexibilité de notre ligne de production a vraiment permis des changements rapides entre petits lots ou entre différentes variétés de cartes », explique Liu Haifeng. « Elle a permis de résoudre le problème persistant de la faible utilisation des lignes de production et a considérablement amélioré notre capacité de production et notre efficacité. Cela a nécessité beaucoup de travail, mais cette combinaison non linéaire de cinq machines de placement a vraiment amélioré l’utilisation de notre équipement et réduit le coût d’entrée de la ligne de production. »
En raison de la force de l’entreprise dans le prototypage rapide, l’équipe de Liu Haifeng constate une intégration croissante avec les équipes de R&D du client. Pour soutenir ce développement, un système de design for manufacturing (DFM) a récemment été connecté à l’équipement Mycronic et au logiciel MYCenter. « Nous continuons de progresser dans la réduction du cycle de réserve pour nos clients », déclare Liu Haifeng. « Nous pouvons effectuer plus de changements et obtenir plus de rendement, de sorte que les clients peuvent maintenant obtenir leur prototype pendant qu’ils attendent à l’usine. Nous aimons dire que nous faisons des 'prototypes à emporter' », dit-il en souriant.
Partenariat pour l’avenir
« Une grande partie de ce succès est due à la grande collaboration entre Mycronic et nous », poursuit-il. « Nous partageons des ambitions similaires, nous apprenons ensemble, et leurs commerciaux et ingénieurs d’application connaissent tous notre métier. Je considère l’équipe locale de Mycronic comme mes collègues car l’interaction et la communication ont été réellement excellentes. Maintenant, tant que nous restons concentrés sur notre activité de niche et que nous allons de l’avant ensemble, peu importe ce que font nos concurrents à volume plus élevé. »