Putting performance data to work
Enhancing reject analysis and line balancing with MYCenter AnalysisAs an innovative European contract manufacturer, DF Elettronica is determined to continually push the limits of automation. Whether it’s inspection, traceability, material transport or process optimization, the application of highly advanced technologies has been central to the company’s successful production strategy for many years. MYCenter Analysis is just the latest in the ongoing pursuit for the optimal high-flexibility production environment.
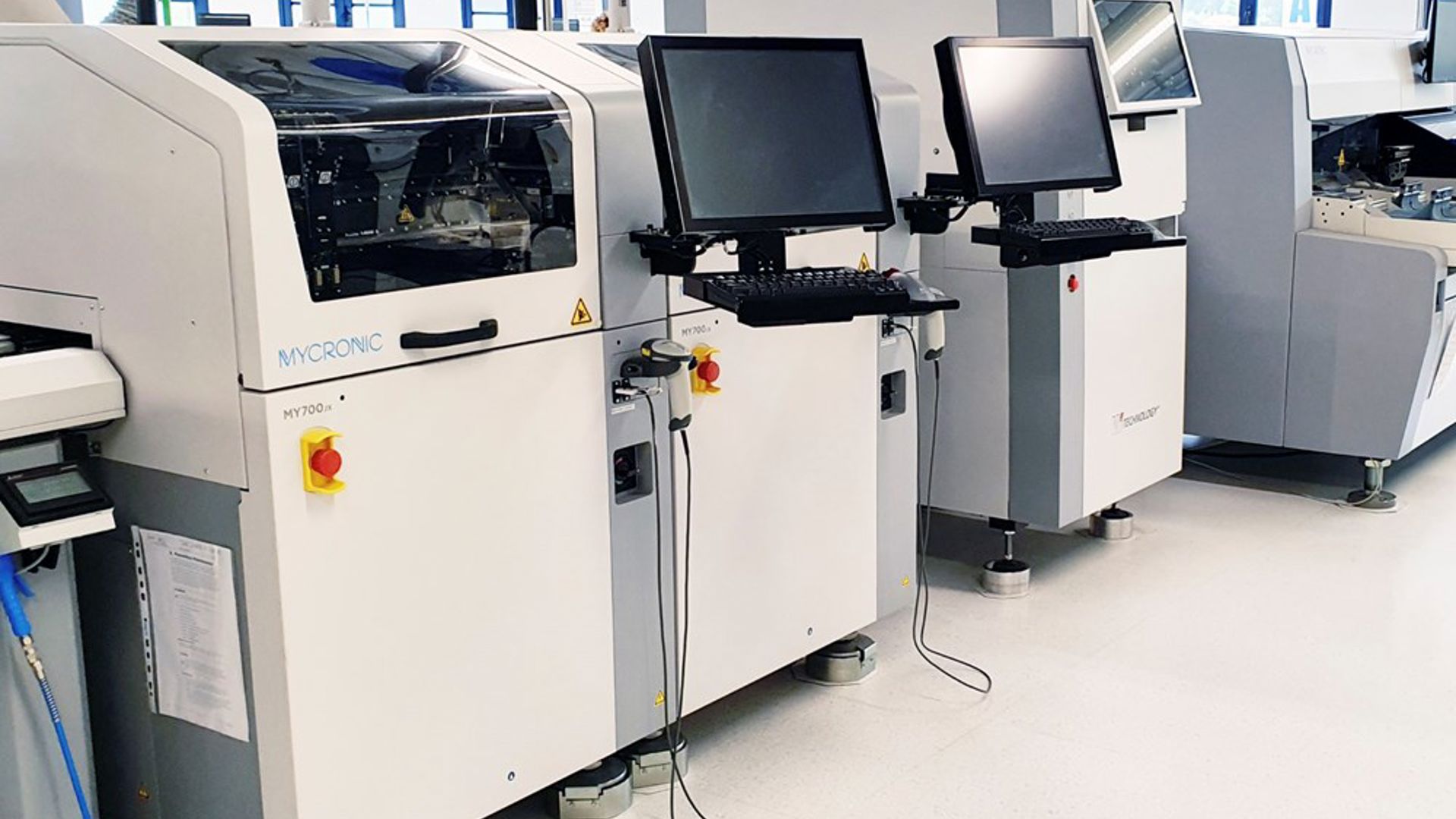
Located on the northern outskirts of Florence, Italy, DF Elettronica is a relatively small EMS with a staff of just over thirty. But by combining the right people with the right production technologies, the company punches well above its weight, serving a diverse range of leading European biomedical, lighting and telecom customers.
Investing in agility
“Our owner is a strong believer in factory automation and the application of advanced technologies,” says Patrizio Sorace, production manager at DF Elettronica. “He was early to invest in a vacuum chamber oven, which was a crucial strength in the manufacturing of high-quality LED lighting systems. When he saw too much time spent moving racks of PCBs from SMT to final assembly, he invested in autonomous transportation systems. The same is true for 3D inspection, laser marking systems and flying probe testing, all of which have paid off for our customers. So when he heard of MYCenter Analysis, he immediately saw its potential to save a lot of time and effort.”
Down on the production floor, the most immediate need was for better visualization of pick-and-place performance data. “When it came to machine balancing, we wanted a quicker way to understand where we could make potential improvements,” says Mr. Sorace, explaining that this was especially true for their large batch production line. “Some of these batches can occupy the line for several days, so even five or six seconds gained per board is pretty significant.”
The other objective was to more rapidly identify the sources of component rejects and waste, which all too often involved complex root-cause analysis. “We’d ask ourselves: Is this a feeder problem? Faulty package design? A dirty or broken nozzle?” says Mr. Sorace. “There are tons of variables, so what we really wanted was some kind of statistical analysis that would tell us whether a majority of the problems were related to a specific nozzle, or component for example”
The power of Analysis
Given an opportunity to beta-test MYCenter Analysis, Mr. Sorace and his team leapt at the opportunity. “We were really happy when we received the first release of MYCenter Analysis,” he says. “This was exactly our goal: to get the statistical analysis we needed for operators to find the reasons for any reject problems. Now they can just click to find the images of a nozzle that needs cleaning and very quickly draw the right conclusion. Or they might use it from home to identify a problem nozzle, for example. Of course everything’s not solved, but we’re certainly making improvements.”
Seeing the big picture
As with many smaller factories, Mr. Sorace and his colleagues have a wide range of tasks. As production manager, Mr. Sorace oversees the infrastructure, monitoring overall machine performance and potential workflow improvements. At other times he might assist on the production line, creating packages and performing other technical duties. “This is typical for a factory like ours,” he explains. “We’re all so occupied with multiple machines and processes that it can be difficult to see the bigger picture sometimes. That’s where a software like this can make a difference, giving us the statistical overview we need.”
In the future, the company’s owner has proposed assigning a stronger role for production monitoring and improvements to an advisor off the line – a responsibility most likely to fall to Mr. Sorace and MYCenter Analysis. “Our operator simply has too much to do,” Mr. Sorace says, “so now I can use the software to support him. I can easily see a scenario where a high-volume job comes in, each line has its own dedicated operator and someone outside the lines focuses on production monitoring, analysis and improvement. This is what we’re aiming for.”
Boosting performance
When asked to quantify the benefits of MYCenter Analysis, Mr. Sorace admits that this can be a challenge in high-mix production, where the aim is to continually gain control over an endless range of variables. “Our production varies so much from job to job that’s it’s really difficult to do any kind of before-and-after comparison,” he explains. “And this year is a total anomaly due to the pandemic, so any comparative analysis wouldn’t be very realistic. But our experience is that MYCenter Analysis has helped us a lot, especially in terms of reject analysis and line balancing for bigger jobs. In the long run we’ll definitely use it to set more data benchmarks, and to compare historical data with current performance. If we can continue to increase automation, improve our ability to change very quickly between jobs day-to-day, and serve a lot of customers very quickly with high quality and the lowest possible cost, then we know we’re headed in the right direction.”