Smaller, smarter, faster
Full-line flexibility in Germany’s industrial heartlandJust outside of Nürnberg, Germany, one forward-thinking manufacturer is rapidly modernizing its production to meet fast-growing demands for advanced industrial IoT electronics. Thanks to the latest full-line assembly solutions from Mycronic, mikrolab can now respond to global competition with greater speed, quality and cost efficiency than ever before.
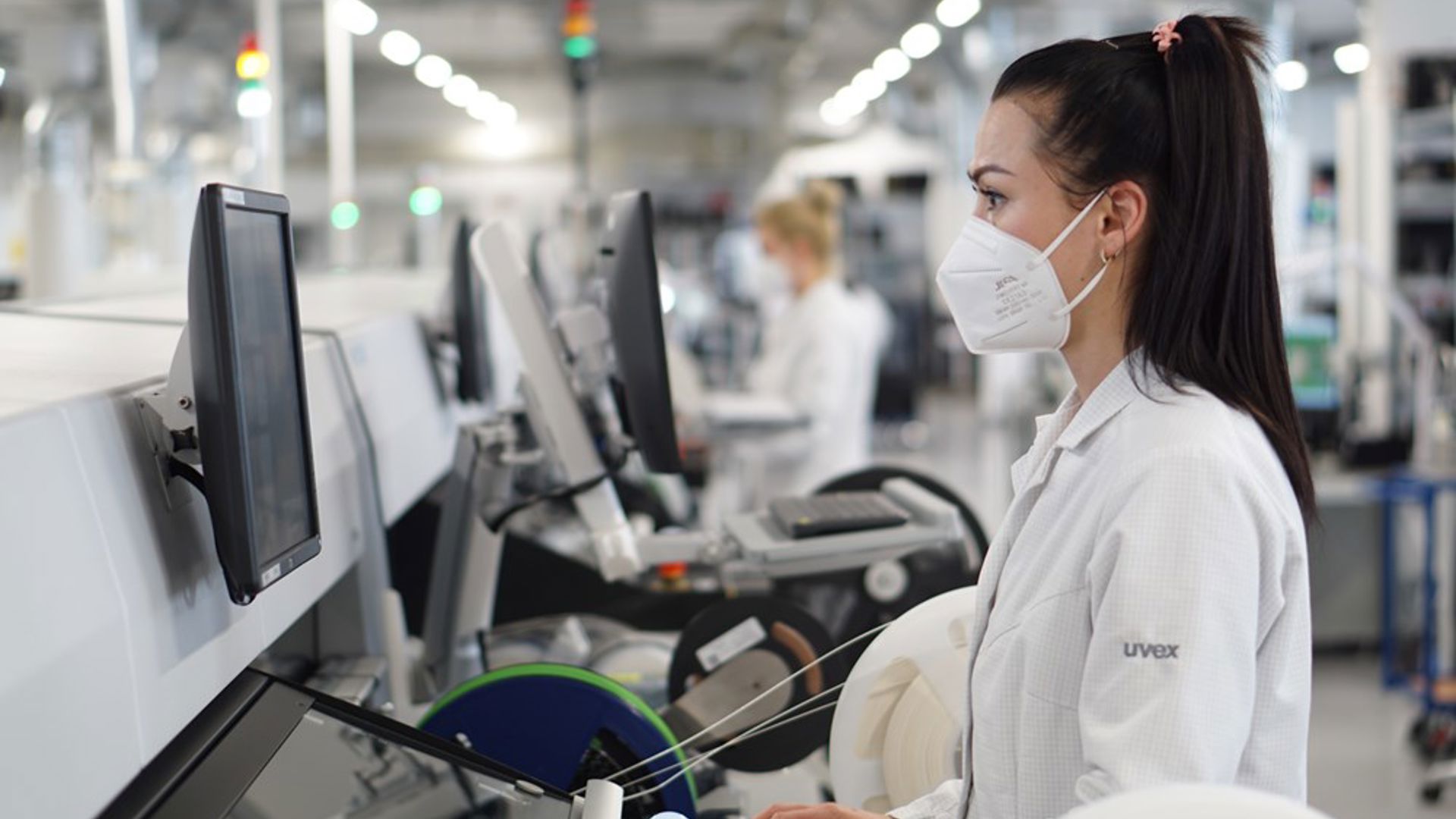
A new era of automation
Founded in 1978, mikrolab is based in the German industrial heartland, a region renowned for some of the world’s most advanced manufacturing solutions for medical, automotive and industrial automation technologies. In recent decades, the company has specialized in the development of firmware and hardware for embedded digital systems, as well as prototyping, testing and series production of electronics assemblies and complete devices. Today some eighty percent of production is dedicated to sophisticated OEM products including navigation systems for maritime vessels, portable measuring and control devices, safety-relevant medical electronics and control systems for various industrial applications.
For nearly twenty years, the company’s two SMT lines have served them well. But as customer needs evolved, a new production line was needed. In particular, mikrolab aims to significantly expand its share in the fast-paced EMS market, where an ability to handle far smaller and more diverse components, flexible changeovers and a wider range of batch sizes is an absolute necessity. “Our customers are trying to assert themselves in the market by establishing entire product families,” says Andreas Lebrecht, Production Manager, mikrolab. “This leads to smaller quantities and more assembly variants.”
A full-line Mycronic solution – consisting of two MY700 Jet Printers and three MY300 pick-and-place machines – was chosen to replace the previous two SMT lines with the aim of ensuring the best combination of speed, flexibility and quality. MYCenter Material Handling, MYCenter Proactive Replenishment Monitor and MYCenter Analysis were also included to provide intuitive interaction with the data most crucial to maintaining high productivity throughout the assembly process.
Boosting flexibility
One of the key motivations for the new investment was the need to handle far smaller components, down to dimensions of 150μ x 300μ, as well as larger board formats. “By replacing our four pick-and-place machines with three MY300s, we now have a much wider range of both board sizes and component types,” explains Andreas. “They can be as small as 01005 or 03015 chips, or as large as 140 x 73 x 22 mm. Now we’re able to print, assemble and solder PCBs as large as 640 x 510 mm.”
The addition of two MY700 Jet Printers has added further productivity gains. By eliminating the need for stencils, the solution enables rapid changes to solder paste application while maintaining speeds up to two million dots per hour, thus ensuring continuous supply to the pick-and-place machines. “The costs and procurement time of the stencils are completely eliminated,” says Andreas. “Setup is very fast, and thanks to the four ejectors, we can now apply adhesive dots and solder paste in one production run, even if there are already components on the side to be printed. We’ve removed all the limits we faced with stencil printing.”
Streamlining changeovers
Of course, a wider variety of products also means more changeovers, which is exactly the challenge the Agilis feeder system, e-label systems and material handling software were designed to address. “The Mycronic set-up concept is significantly more cost-effective than the alternatives,” says Andreas. “The Agilis feeders are a huge advantage when you take into account our component diversity and batch sizes, and this has a direct impact on the available machine running time and production costs.”
With the new system in place, changeover times have been dramatically reduced, and setup errors have been virtually eliminated. The result is consistently high line utilization and daily placement output despite a growing number of changeovers, says Andreas. “We’re not impressed by a line’s theoretical placement performance, according to IPC. The real performance over the course of a day always depends on the range of components on the assembly, the distribution of components among the machines, the order’s batch size and the eventual downtime due to tooling, sampling or missing feeders.”
Software-driven performance gains
For program creation, mikrolab uses a combination of Factory Logix Express and MYCenter with CAD import. “It’s a really intuitive way to create programs for the jet printers and pick-and-place machines,” says Andreas. “The processing time is minimal.”
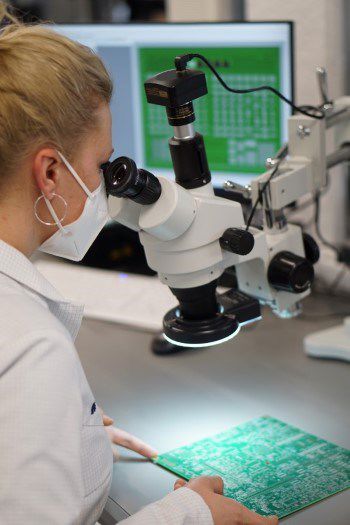
Along the new production line are several large monitors displaying MYCenter PRM (Proactive Replenishment Monitor) and MYCenter Analysis. “The operators use MYCenter PRM to see what material is needed for the current job so they can prepare the material in advance, which significantly improves productivity,” says Andreas. “MYCenter Analysis gives them a live overview of the most important performance indicators on the pick-and-place machine, which makes it a lot easier to visualize operational data and discover potential performance improvements.”
Facing the future
With the new production line in operation, Andreas and his team are looking forward to collaborating more closely with customers in developing and manufacturing their future product portfolios. “Our market is really facing two growing trends right now,” he explains. “On the one hand, there’s more and more transparency and comparability in international tenders, which makes it very important to maintain the right cost structure. On the other hand, the importance of reliable partnerships is also growing, especially among small- and medium-sized customers, so our collaboration with long-standing customers is certainly going to intensify.”
The automotive industry, Andreas explains, is an especially good example of the need for speed, quality and flexibility in electronics manufacturing. “In a lot of cases, ‘just-in-sequence’ delivery has become standard and is now working its way in to the regular industrial sector,” he says. “We also expect data networking to take hold, so that customers can see the status of their orders in real time. Now we’re well positioned to support both these trends as the pace of change continues to accelerate.”
“At the end of the day, we’re very excited that we can now set up and produce new jobs more quickly and more cost-efficiently,” Andreas concludes. “The new production line really enhances the product quality and expands our technological capabilities. Now that we have much higher capacity – both in terms of component range and throughput – we can increase the number of assemblies we produce and serve even more technologically demanding customers.”