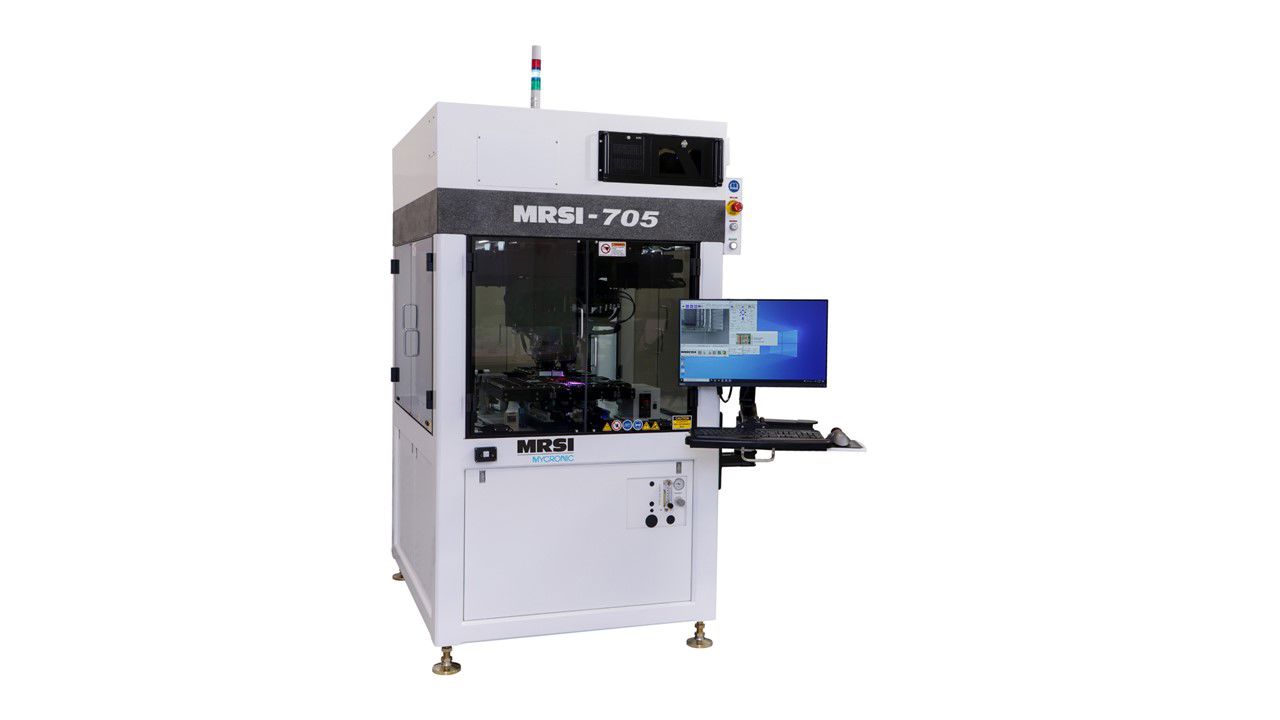
MRSI-705 DIE BONDER
- Flip-Chip Capable
- Offers an optional patented turret configuration to significantly increase the production volume
- Built to meet the highest standards of reliability and dependability
The MRSI-705 5-Micron Die Bonder sets the mark for high-precision, high-speed component assembly. Engineered for manufacturing robustness, the MRSI-705 is a flexible configurable platform, with the largest installed base in the industry in advanced packaging. Applications are found across a wide range of market segments, such as life & health sciences, aerospace, defense, automotive, lighting, communications, and more.
The MRSI-705 is built to meet the highest standards of reliability and dependability. It starts with an award-winning, industry standard platform with a day-in/day-out accuracy of 5 microns; achieved by leveraging the platform’s signature design features:
- A solid granite platform supports the placement head from above, so that no mechanisms are cantilevered. All of this makes the MRSI-705 thermally and mechanically stable with extremely fast settling times and +/- 5 microns or better placement accuracy, a requirement for critical applications.
- Minimized number of moving mechanical parts.
- The major system X Y axes use zero force, ironless, actively cooled linear motors with high resolution linear encoders. Encoder scales have 0.1-micron resolution for fast, precise, closed-loop positioning. The linear motors deliver faster speeds (acceleration, deceleration and velocity), with better settling times and overall smoother motion.
- Reliability is enhanced through the use of advanced air-bearing technology in the Z axis.
Benefits
The MRSI-705 produces the following compelling business outcomes for customers:
- Strongest ROIs in the industry – A well-established platform with an unmatched Cost of Ownership. Lifts up overall production efficiency.
- Extended Machine Lifetime – Exceptional performance over time. Upgrade paths as new features are introduced.
- Proven Manufacturing Readiness – A work horse with minimum downtime. Compelling reliability.
- Configurable Asset – The MRSI-705 is an open platform that adapts to changing portfolios. Can handle complex multi-chip modules and other advanced assembly challenges with ease.
New Configuration for Higher Volume
The MRSI-705 offers an optional patented turret for “on-the-fly” tool change to significantly increase the production volume from our machine without sacrificing flexibility. The patented turret has the capacity for 12 tools with zero tool change time. This leads to increased machine efficiency, higher output and lower manufacturing costs. Applications include complex products with multiple chips and processes that require processing of chips with different sizes or epoxy stamping processes, which can significantly improve equipment efficiency.
Features
The base MRSI-705 die bonder comes already equipped with industry-leading functionality. Additional capability is available to reflect specific application needs. Standard Features include:
Large Configurable Work Area
The unique overhead gantry design of the MRSI-705 translates into a large 700 sq.in work area that easily accommodates a wide variety of material inputs and outputs. The MRSI-705 can accommodate up to 90 Waffle Packs when utilizing the system’s unique Sector Plate Shuttle, ensuring maximum flexibility in assembly. Even the smallest die can be effectively handled.
The system can pick from any combination of Gel-Paks®, waffle packs, wafers, and tape feeders. When picking from wafer, the system utilizes a motor-driven, controlled force lift mechanism for picking thin die and large aspect ratio die, and includes theta compensation. Ink dot recognition and wafer mapping ensures that only known good die are picked.

Force Control for Advanced Assembly
The MRSI-705 features closed-loop force feedback, enabling delicate handling of III-V semiconductor components, such as Gallium Arsenide (GaAs) and Indium Phosphide (InP) devices as well as MEMS with fragile microstructures. Die are processed with forces as low as 10 grams applied to the component. Force values are programmed per component type, which means that each die type can be picked and placed with its unique programmed and controlled force.
Advanced Machine Vision
The MRSI-705’s advanced vision system enables rapid detection and orientation of die over a full 360°. Boundary trace or pattern recognition is used to locate the die center or application-critical features, as well as robust substrate fiducial alignment. This enables the alignment of orientation-critical die such as MMICs and beam lead diodes prior to placement.
The vision system aligns and places die according to substrate fiducials, the die edge, or relative to features of previously-placed die; ensuring repeatable and precise alignment of optical and microwave devices.
- Boundary trace and/or pattern recognition is used to locate the die center, edges, or any other application-critical features.
- Fast orientation enables die such as MMICs and lasers to be used directly from the supplier without any need for pre-orientation.
- Global and local vision alignments are used for nested substrates and feature alignment. This enables fast, error-free processing of complex assemblies.
The MRSI-705’s vision system features multiple magnification and programmable lighting for both upward and downward facing cameras.
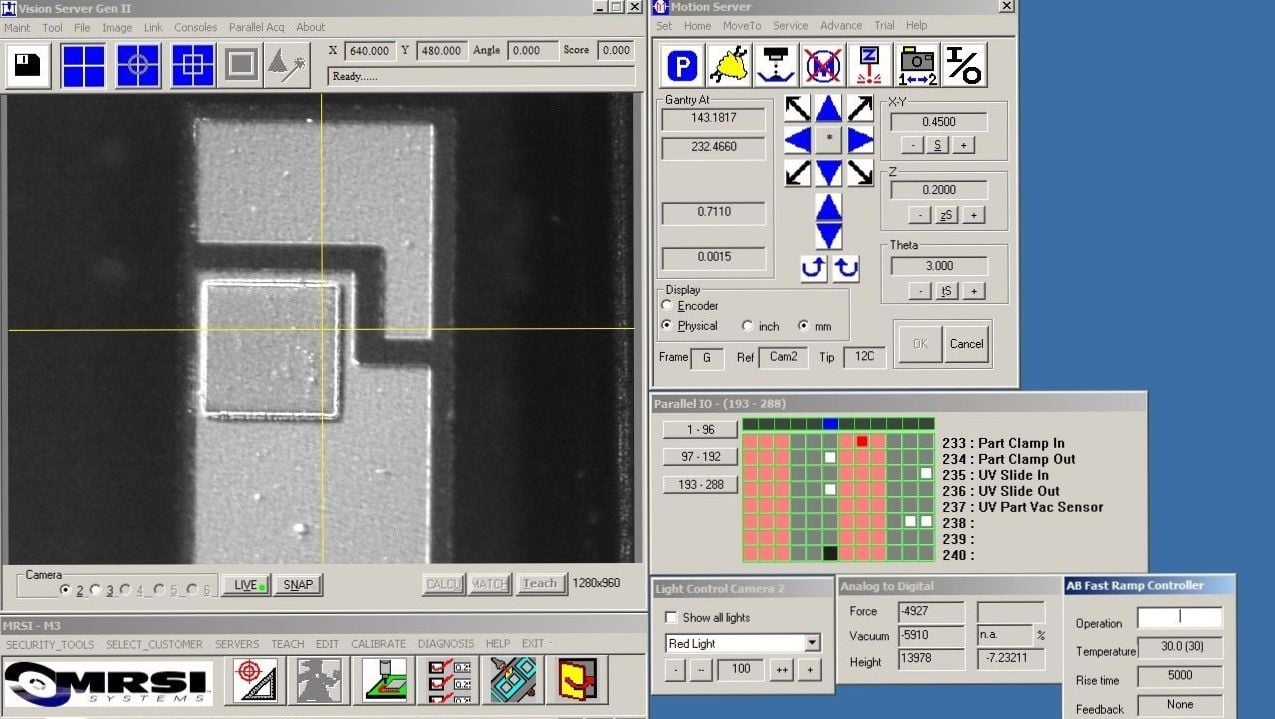
Programmable Multi-Color Lighting
Lighting intensity is programmable for both ring and collimated light functions, for each camera. Optimal light conditions may be set for die recognition and for alignment. Multi-color lighting may be used to enable optimum imaging of a low-contrast components. Red, green and blue programmable lighting is a powerful tool when processing challenging alignment surfaces such as gold on alumina. Such an advanced vision toolbox ensures optimum performance, which directly translates into less machine interruptions due to vision errors.
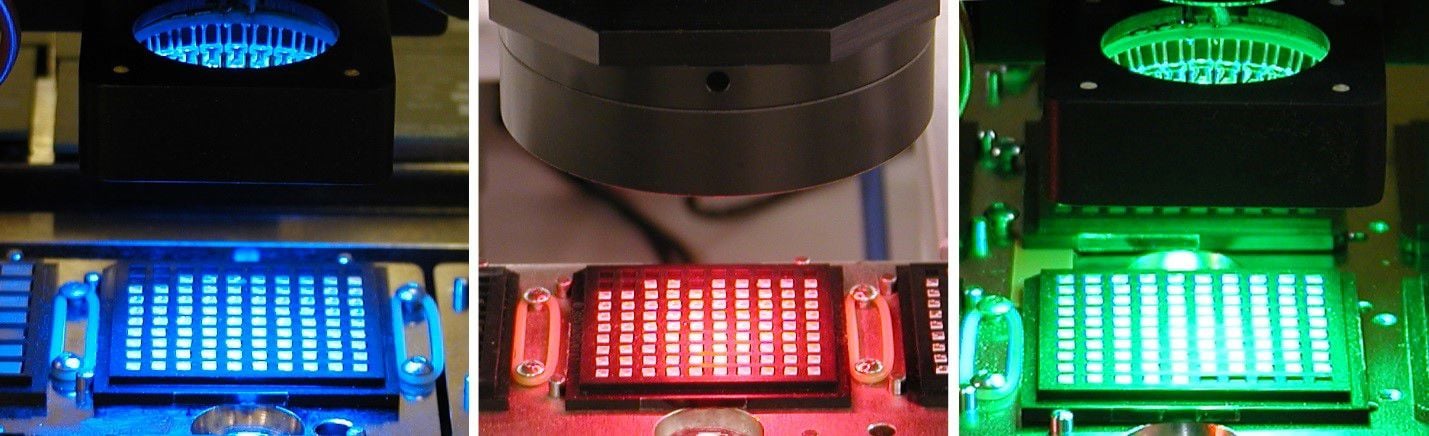
Quality Software, Computer and Motion Control
The MRSI-705’s intuitive graphical user interface runs on Windows and simplifies the set-up and production process. The software includes a pre-programmed library of waffle packs and die. Components are easily taught and are available for all substrate programs. The XML-formatted database allows for simple data manipulation and offline programming. New vision tools such as an adjustable region of interest, enhanced gain control, filters, and pattern matching enable vision processing of the most challenging substrate and die materials. CAD download, advanced calibration routines, automatic program selection based on the bar code of an incoming boat, full material traceability and network connectivity mean that very little machine time is devoted to programming, thereby maximizing productivity.
The MRSI-705’s control platform provides smoother and more precise control with up to 32 axes of motion, and a common controller for all axes including the conveyors. Computer hardware configuration features front USB ports for ease of use and dual hard drives with ghosting for optimum data security and minimum down time/immediate recovery.
Turnkey Integrated Production Lines
MRSI Systems offers a complete solution for advanced packaging, including our family of high-speed, precision bonders and epoxy dispensers. SMEMA compatibility allows integration of the MRSI-705 with a wide range of equipment including in-line ovens for a turnkey production solution. MRSI Systems reliability combined with our worldwide service and support commitment means that your system will always be available for production.
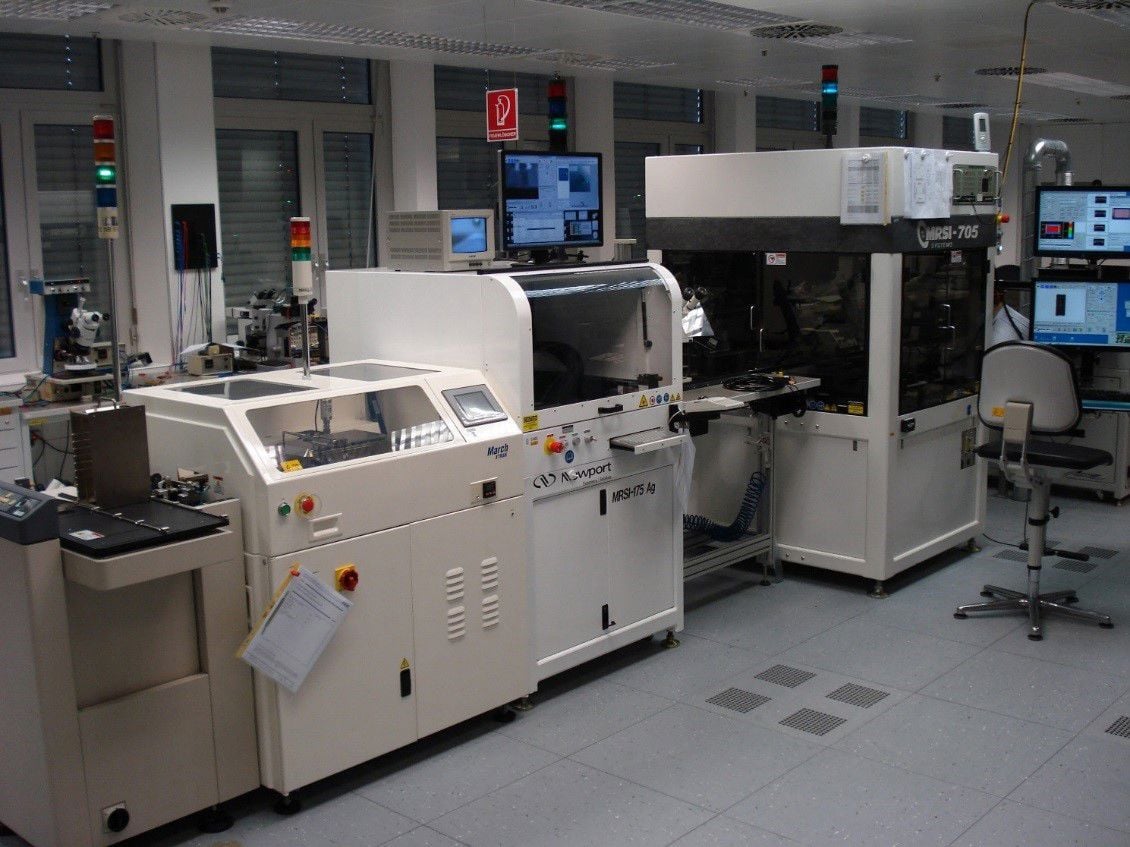
Options
MRSI systems may be configured with off-the-shelf options to meet application-specific needs, a cost effective alternative to custom automation. The base platform comes equipped with standard features. The machine can then be configured in various ways with one or a combination of the following options:
Material Handling
Tooling is modular, ensuring fast, easy change-over between production runs – The MRSI-705 supports three modes of operation when it comes to product presentation. They are: in-line conveying, cassette-to-cassette load/unload, or standalone mode. The system’s conveyor readily handles boats, fixture trays, lead frames and boards. The MRSI-705 offers heavy parts-handling capability and excellent co-planarity for large die assembly.
Benefits:
- Easily integrated into automated production lines, both the in-line and cassette-to-cassette tooling options allow for greater machine autonomy, translating into a workload reduction and less setup downtime.
- Standalone tooling allows for greater flexibility required for R&D and small lot production, translating into faster changeover and therefore higher machine efficiency.
- Existing customer tooling, used upstream and or downstream from the assembly step, can be adapted; allowing streamlined product handling strategies to be implemented. Less product transfer means less operations, lower handling defect rates and improved cycle time.
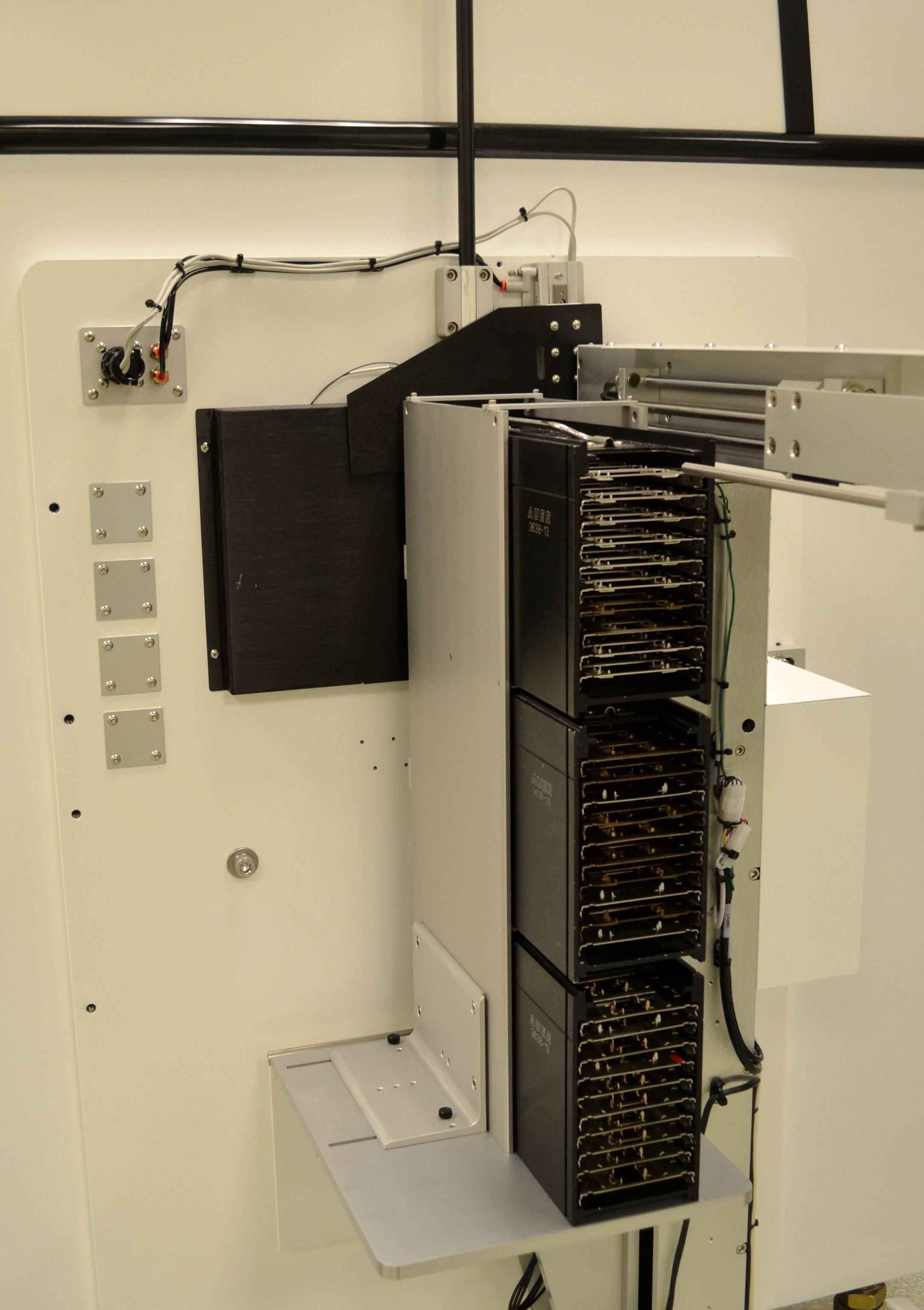
Tool Change
Limitless number of pick-up and stamping tools on board – The MRSI-705 features a thirteen-position tool bank with fast automatic tool change. Additional tool change banks are added for a wider range of tools. The tool change banks hold round surface pick-up tips, perimeter and inverted pyramid collets, and stamping tools. This is particularly well suited for processes requiring a large number of parts-specific tools, such as eutectic bonding applications.
Benefits:
- Ability to assemble complex products with a multitude of component types. The overall reduction in production cycle time translates into higher throughputs and machine efficiency.
- Fast Product Change-Over means increased machine efficiency. Increased efficiency translates into higher output and lower manufacturing costs.
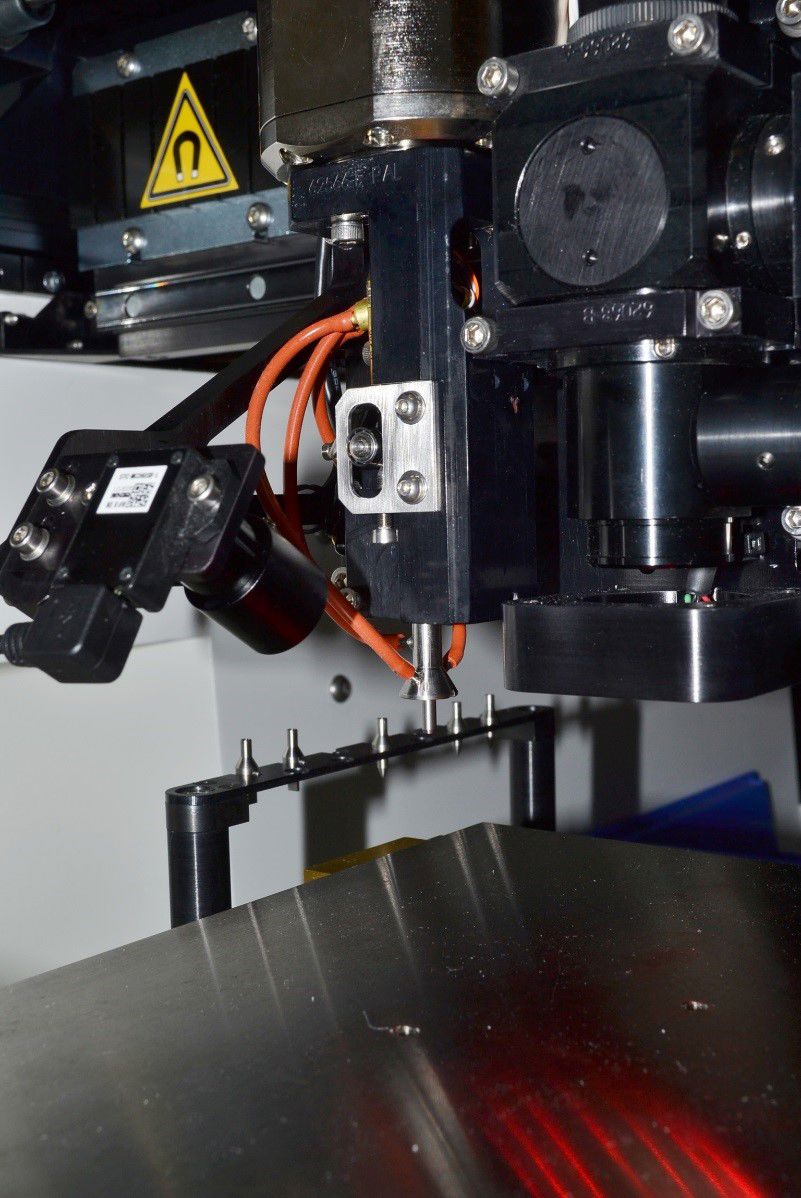
Wafer Processing
Direct Pick from Wafers minimizes die handling and simplifies supply chain – The MRSI-705’s automatic wafer feeder includes automatic theta compensation, servo controlled synchronized closed loop movement of the pick head and the ejection needle, wafer mapping, ink dot detection, and fast change ejection needle clusters. Needleless ejector system is available for ultra-thin devices. Thin and fragile die are delicately picked from the wafer tape by synchronizing the movement of the pick head and the ejection needles. Automatic theta compensation aligns the die to the needle cluster in the theta axis. Wafer maps or ink dots are supported, ensuring that only the good die are processed. Fast change ejector needles and domes allow for easy accurate changeover between device types.
Benefits:
- By using servo controlled synchronized systems, yield is increased by avoiding damaged and cracked die, especially for thin, fragile III-V material die, with internal or surface features.
- Production volumes are increased by eliminating pick error caused by wafer theta to the ejector pins alignment, especially for high aspect ratio devices.
- Wafer result mapping and ink dot recognition assures only know-good-die are used, thus ensuring a high yield. Fast change ejector needles and domes maximize system uptime.
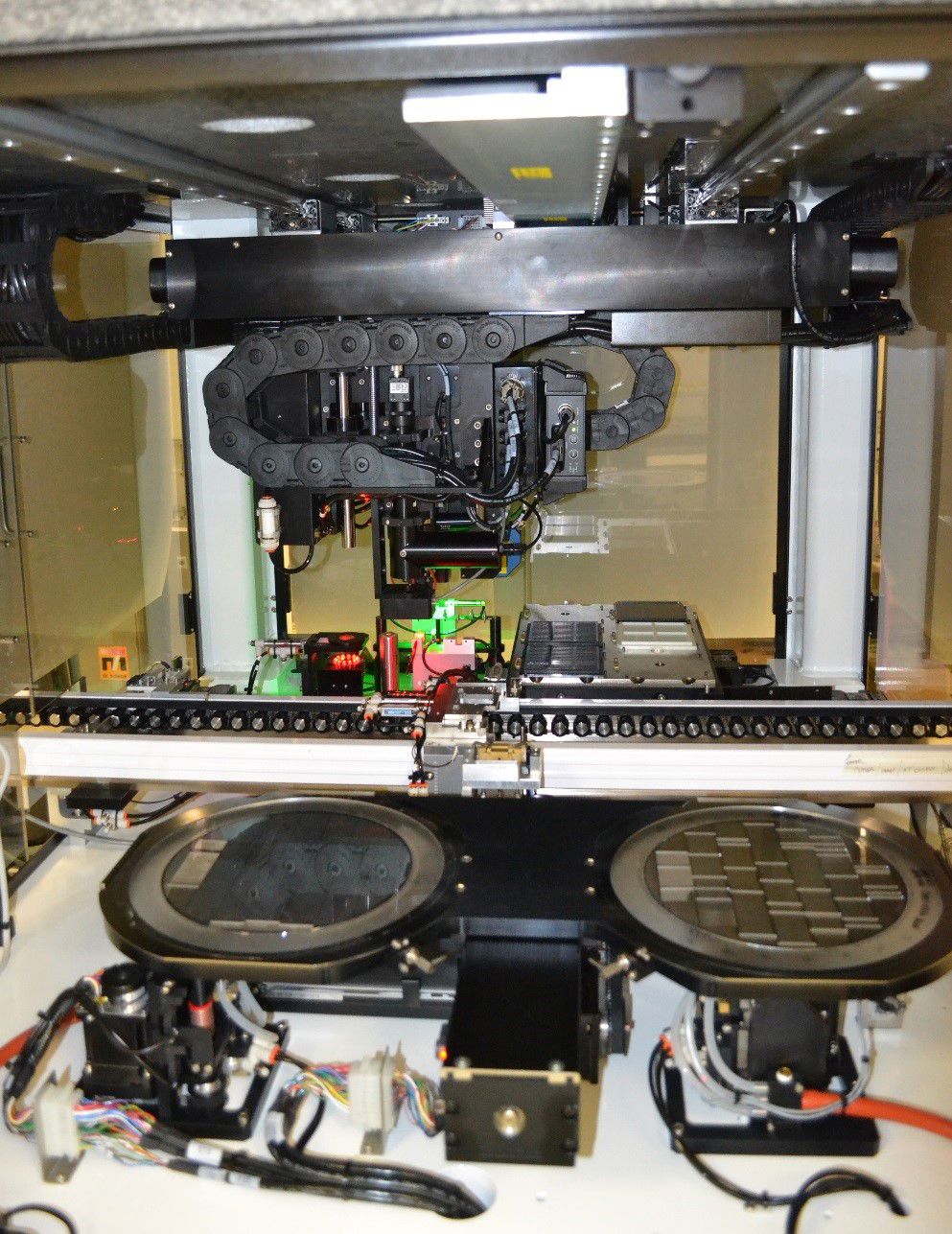
Stand Alone Eutectic Capability
Flexible and High Throughput Solution for High-Reliability Packages – The MRSI-705 may be configured with a eutectic bonding kit, ideal for Gold Silicon, Gold Tin and Gold Germanium bonding processes. With this package, applications such as eutectic bonding on sub-mounts, TO headers, and butterfly packages are possible. An optional Progressive Heated Boat Indexer is available for high volume eutectic applications.
Both direct eutectic and reflow eutectic bonding processes are supported. The package includes a reflow station with a hi-speed temperature ramp (closed loop pulse heating). A heated cover gas of Hydrogen and Nitrogen is present over the hot plate. The reflow station design includes provisions for vacuum hold down or part clamping. The system automatically transports the substrate or package to and from the stage for eutectic bonding.
The eutectic station is programmable, tailoring the process to your specific bonding requirements.
- Contact Forces are closed-loop controlled
- Temperature ramp rates are programmable, optimizing the heating profile while avoiding thermal shock.
- Multiple temperature setpoints are programmed to bring the substrate to a base temperature, followed by a final rise to the reflow temperature, as the part is placed.
- A programmable mechanical scrub may be used to break through oxide layers, thereby ensuring overall bonding quality.
Benefits:
- This optional package permits a portfolio expansion to offerings of hermetically-sealed packages. In addition to packaging of high power devices such as amplifiers, a path is provided for mass production of photonics/optical assemblies.
- The fully automated process ensures repeatable results, equating to higher yields, and an improved bottom line.
- Programmable fast ramping eutectic stage allows process flexibility, while maximizing throughput. Well controlled cover gas flow and temperature minimizes voiding. Vacuum and mechanical part clamping flexibility eliminates part movement during eutectic bonding. A tightly controlled process ensues. Higher yields and repeatable quality is the outcome.
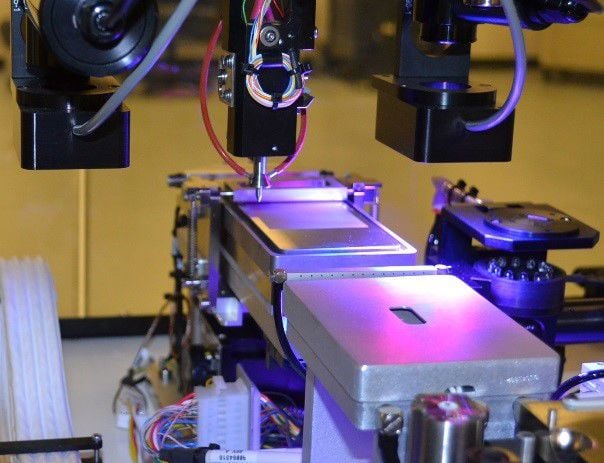
Inline Eutectic Capability
Fully-Automated Eutectic Die Bonding Reduces Labor Costs, Improves Yields – An automated in-line material handling system is coupled with MRSI’s well proven In-Situ die bonding options to provide a high speed, fully automated turn-key solution for eutectic die attach processes.
The in-line material handling system loads a carrier of substrates (boat) onto the conveyor. The conveyor transfers the boat to the bonding area.
- Substrates are incrementally heated to the process temperature by processing through preheat zones.
- At the bond station parts come into contact with the pulse heated bonding stage and the eutectic bonding process is performed.
- The boat is then indexed to the next substrate position and the above process is repeated until all the boat positions have been assembled. As the indexer transfers the boat, the packages are incrementally cooled by passing over a cool down zone position. When completed, the indexing conveyor transfers the boat to the output magazine loader.
- Various bonding processes are supported:
- For Gold Silicon direct eutectic, the system aligns the package and then picks and places the die, and scrubs (variable amplitude and frequency) to accomplish the eutectic bond. A heated cover gas of Hydrogen and Nitrogen is present over the bonding area.
- For solder reflow eutectic bonding, such as Gold Tin (Au/Sn) eutectic attach of Gallium Arsenide (GaAs) and Gallium Nitride (GaN) die, the system aligns the package and picks and places a preform onto the package (if required, the preform can be pre-deposited). The die is then picked and placed, while the temperature at the bonding position is ramped using a pulse-heated eutectic stage and scrubbed (variable amplitude and frequency) to accomplish the eutectic reflow. A heated cover gas of Hydrogen and Nitrogen is also present over the bonding area.
Benefits:
- Improved productivity through automation. Scalable to high volumes.
- Expanded Portfolio, as capability is extended to high-power semiconductor packages requiring high heat dissipation rates.
- Investment protection if re-configuration becomes necessary. Machine retains its base modular nature.
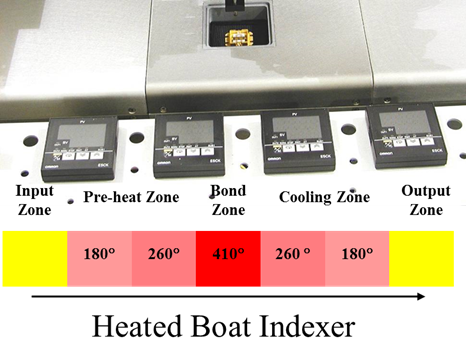
In-Situ UV Epoxy Dispensing & Curing
Applications such as the assembly of Active Optical Cables (AOCs) cannot tolerate loss in die placement accuracy during the post-placement epoxy curing operation. Lenses, for example, require extremely accurate post die bond positioning to ensure optimum system performance. In such cases, In-Situ UV epoxy curing is a solution, whereby parts are cured while held in place, eliminating the possibility of components moving as the epoxy material cures.
The UV option includes specialized UV epoxy dispense hardware, as well as curing accessories. This includes easy-clean, accurate time/pressure dispense pumps for short pot-life materials.
Auto-shutter light guards on the dispense needles ensure that the dispense needle tips do not clog due to inadvertent UV exposure.
Benefits:
- Provides advanced assembly capability on a flexible platform base.
- Fully automated process ensures high yields and reduced labor costs.
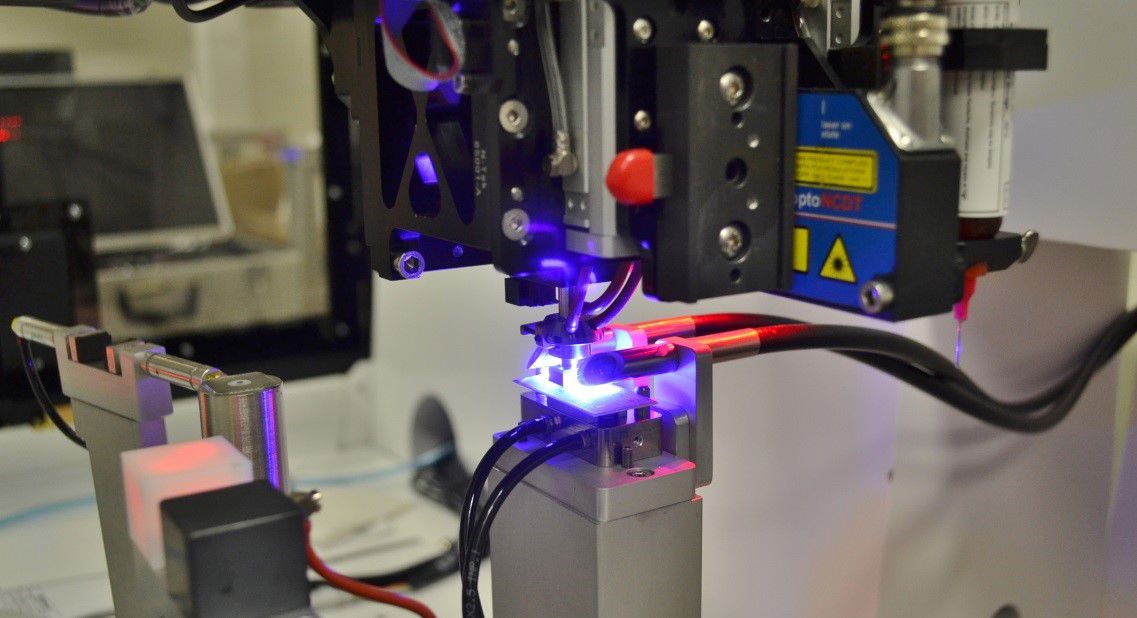
Dispense Capability
Dispense AND Place on the same machine – The MRSI-705 open platform may be configured with dual cartridge style positive displacement dispensing pumps, thereby complementing its core assembly capabilities. Thus, a single machine is able to handle the dispensing of die attach, dam and fill material or lid attach material; followed by the placement of the die or lid as part of a single process setup. The complete assembly process on a single platform is enabled.
The addition of dispensing pumps on the MRSI-705 provides precise control of epoxy volume when dispensing small dots or area fills. Main features include:
- Closed loop servo motors
- A three-point laser height sensor provides the ability to determines the tilt of each surface on which material will be dispensed.
- Automatic needle cleaning
- Automatic needle alignment enables fast setup and switching between pattern types.
- Automatic software calibration routine using through beam sensors
- Automatic priming
- Line drawing capability
- Superior bond line thickness control
- Dot sizes down to 0.004” (100 microns)
Benefits:
- Avoid the purchase of a separate dispensing machine. Ideal for R&D environments, prototyping and low volume production.
- Minimize floor space
- Reduced Setup time
- Scale up with an MRSI-175Ag when volumes ramp. No need to re-qualify.
- Investment Protection through ability to reconfigure the base platform.
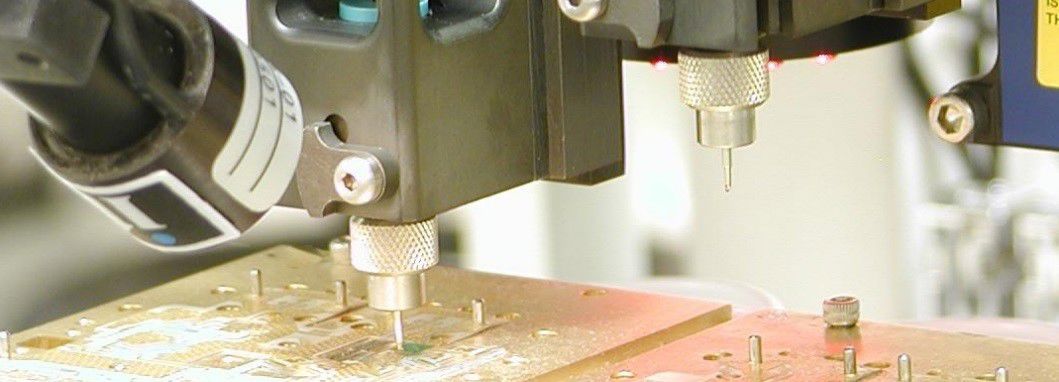
Epoxy Stamping
Complex Assemblies on ONE Platform, with multiple epoxy materials and multiple die sizes along with placement – A rotating stamping-well with multiple epoxy grooves presents epoxy for stamping. Dot size is determined by the depth of the groove and tip dimensions.
Stamping (or daubing) tools are interchangeable with standard pickup tools and are used to create very small epoxy dots by touching down in the stamping well and then onto the substrate. Single dots as small as 0.004″ (100 microns) are possible. They may also be ganged for higher throughput.
Benefits:
- Portfolio Expansion – Added capability of small die processing, multi-chip modules.
- Solution for die attach of small die
- Solution for die attach of complex module assembly with die of varying sizes and varying epoxy materials.
- Minimize floor space
- Reduced setup time
- Investment protection through ability to reconfigure the base platform
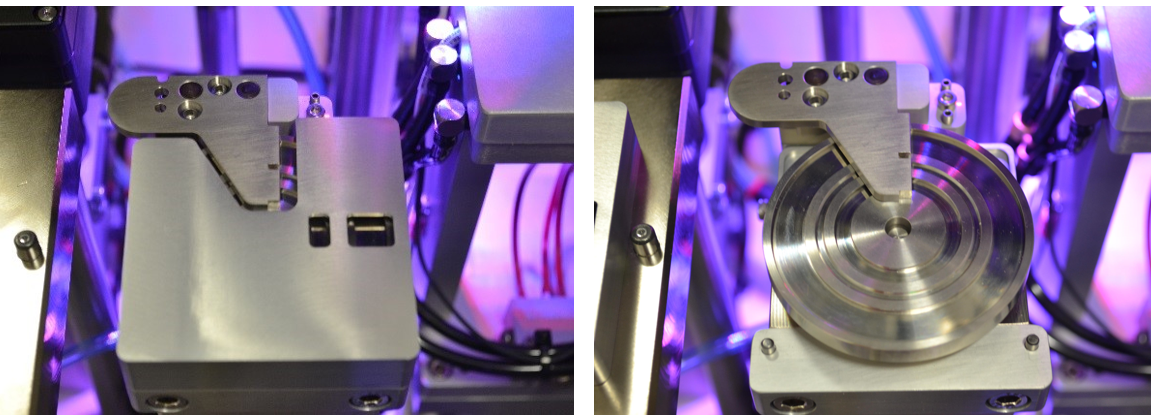
Heated Bonding Head (Optional)
Provides maximum head transfer from atop devices in conjunction with traditional heating beneath devices within a low oxygen atmosphere.
Up to 400˚C at steady status or pulsed conditions. The heated head enables localized eutectic bonding. It is beneficial when there are multiple locations of pre-deposited solder. The heated head gives the ability to bond one area at a time.
Die Bonding with Co-planarity Adjustment
Provides an effective means to ensure accurate and reliable die bonding when a high level of parallelism (co-planarity) between two bonding surfaces is required. The challenges of the bonding co-planarity could result from large size of a die, a die with a high aspect ratio between length and width, the wedge effect along thickness of a die and/or a carrier, etc. MRSI Systems’ production-ready and time-proven technology compensates for these conditions and enables optimal device attachment, be it electrical interconnects or optical paths. Innovative in design, Die Bonding with Co-planarity Adjustment supports a wide variety of applications satisfying Optical Communications, Industrial Lasers, LiDAR, Aerospace, Medical, and more.
Videos
Brochures
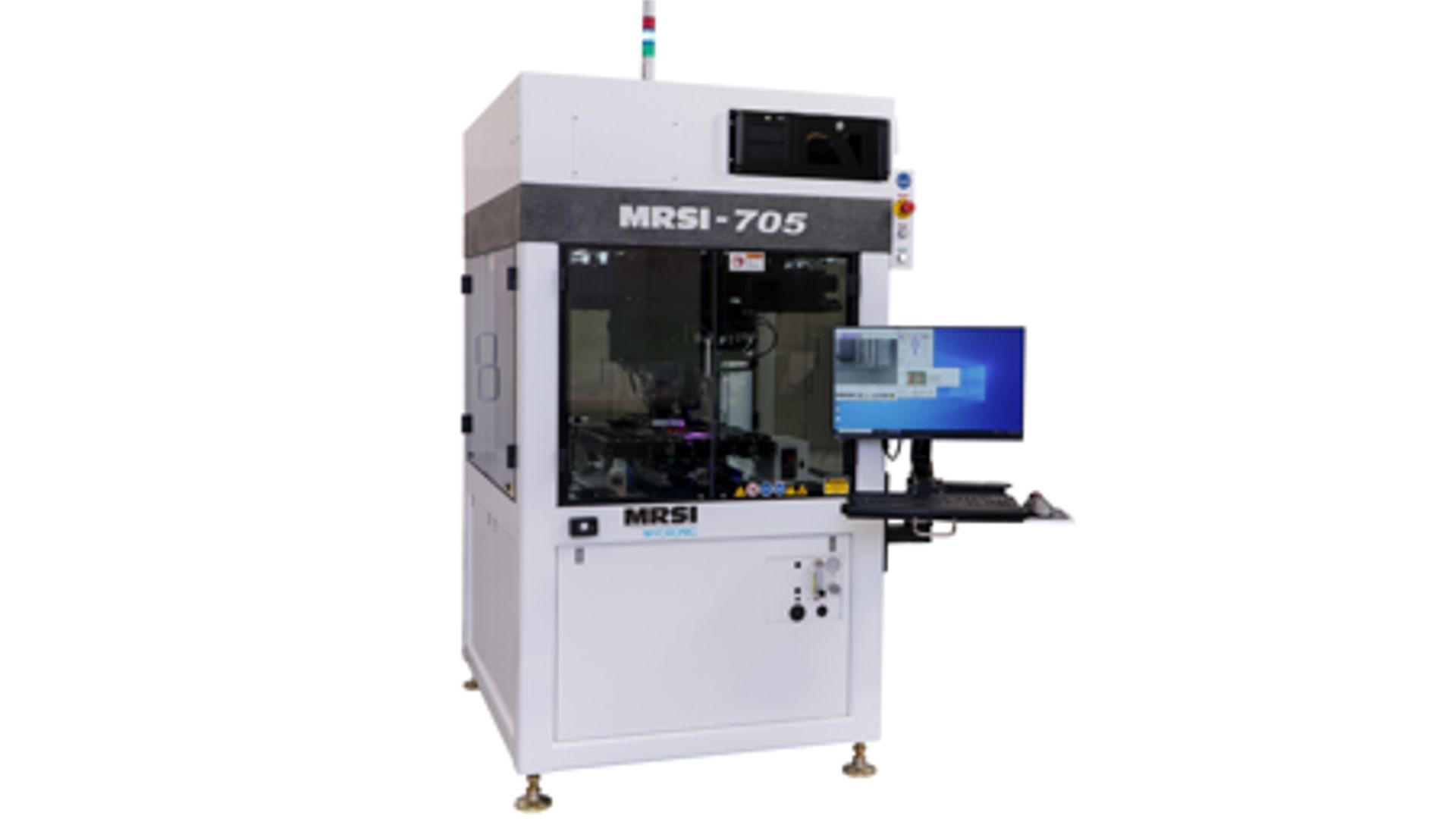
MRSI-705
For detailed Data Sheets please contact Sales.
MRSI-705
Contact us
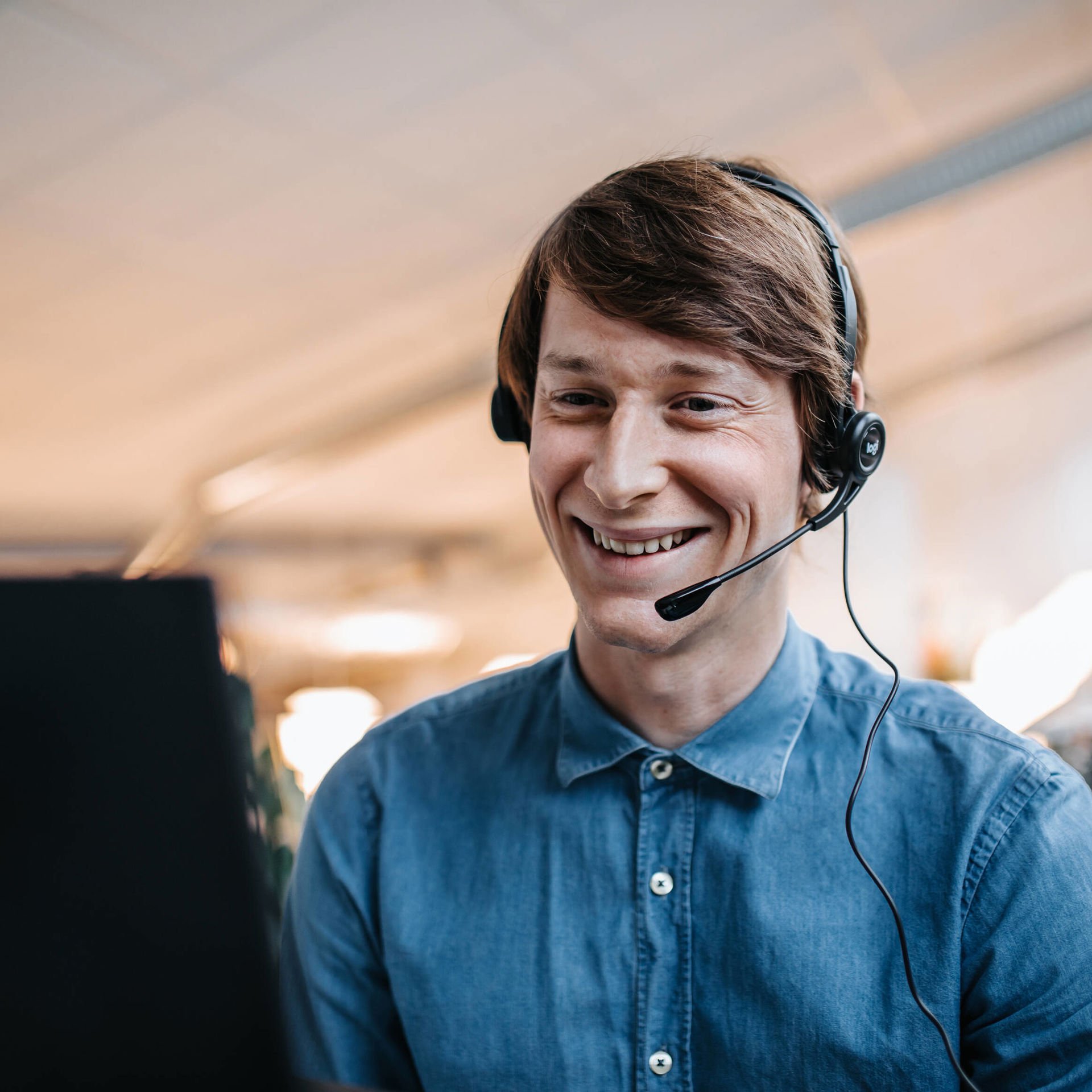