Evolution of a coater
From high volume coating machine to flexible, full featured, easy to program coating systemMYCRONIC INTRODUCED the MYC50 conformal coating system to the global market in November 2017. The system was designed to work in the demanding high running factories of China and Asia.

Entering new markets required different capabilities, the quality was there, but the demands in Europe and the Americas required adapting the system to a new marketplace. A multidisciplinary team working on three continents was formed to obtain direct customer input as well as competitive offerings. An aggressive timeline was set to obtain the minimal viable product (MVP) and subsequent enhancement of the new functionalities to be on par with the leaders in these regions. A new R&D approach was implemented where both Mycronic sales and applications worked hand in hand with R&D to jointly bring to market a solution capable to address any coating requirement.
Two critical developments to become on-par with market leaders
A third coating valve for GEL applications was the most critical item to develop. Gel valves apply a thicker version of the coating material with a needle to prevent the coating material from entering into connectors and other restricted areas on a PCB where interconnection and conductivity are critical. For many of today’s coating applications this is a must have valve. Developing the GEL valve allowed to perfectly coat even the most critical (densely populated) PCB’s.
Offline programming is a critical software feature for conformal coating customers. In a medium volume high mix production environment it is important to be able to prepare the next program while the first batch of a different product is being produced. Furthermore conformal coating is not a digital process, it is an analogue process where material viscosity, flow, atomization and surface energy will define your coating results.
When the design requirements were complete, we understood that to offer this function we had to re-define our online software as well. In 12 months both a new online software and offine programming software were released. Giving the MYC50 a more intuitive interface online and an easy to program oÁine function. Customers have highlighted its versatility and ease of use compared to their previous experiences.
Now we were on-par with the industry, but we strive to be the leaders. Our focus has switched to process control, ease of use and new capabilities.
The steps to a full process control, flexible, precision coating system
Spray coating is one of the most widely used methods for conformal coating. Compared to film coating it can handle from low to mid-range viscosity materials and also the PCB layout is hardly given any restriction. The drawback is edge definition. How to have both a fast process with good edge definition using a spray valve? We tackled this challenge and developed the V-5800 valve. When baselined against film coating valves that can only be operated with low viscosity materials and cannot be used when there are many tall components on a PCB, the V-5800 performed as well and at similar speeds. The V-5800 gave our customers greater flexibility with a single valve than available before. This is now our go-to valve for most applications.
Typical three valve conformal coating setup: 1) Gel valve, 2) Needle jet and 3) Precise spray valve.
As mentioned, coating is a very analogue process and material flow is important to understand if a process is robust and repeatable. By understanding this principal an active flow monitoring system was developed. This system monitors the material flow during coating in real time, the flow range is determined during process programming to tie the output of a good part to the flow of the system when coating that part. The process window is defined by the user for each product. This way board-to-board repeatability can be guaranteed, but also overcome issues like flow variation due to viscosity changes over time. The flow system can also be used to determine and adjust the material flow per valve. For traceability requirements, we can register the applied amount of material for each PCB in a log-file.
In order to coat and dispense into critical angles, the valve’s nozzle stand-off distance and entry angle are important concepts to understand. To make the processes more repeatable the nozzle finding system was developed, to detect all valves working at any angle. This results in repeatable processing of all parts when tied to a laser height sensor, removing the normal variation from operator to operator setups.
As processes get integrated into larger production lines, it is important to be able to work with MES systems. For this a new software package that ties into our new software was developed and allows for the customization required to meet different end user expectations and mandates for each of their individual MES systems. Now we are able to offer into the Tier 1 (automotive) suppliers with much stricter process controls and MES requirements.
The evolution continues
Our 18 month journey toward an evolved MYC50 conformal coating system will never be complete. We are constantly improving to offer the best product in the industry. We are already in the works to enhance fl ow monitoring, online/oÁ ine software, coating inspection and other new coating process enhancements. Our approach in MYSmart is customer centric development and this has resulted in new business gains across all regions. As a result of our customer centric approach to development we have developed a new product for industrial dispensing!
Offline programming
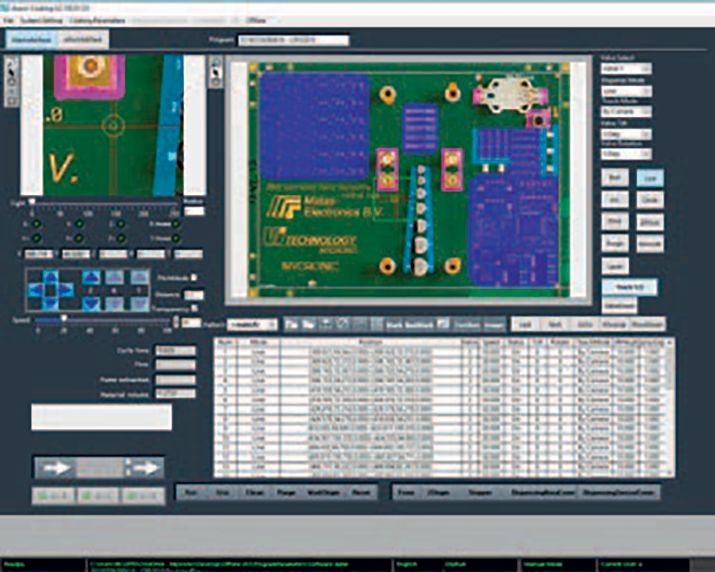
Some highlights are:
Each valve application is selectable by color (above right). The width of the pass is defined by the user and area coating is simple by teaching the diagonally opposite angles — the software calculates the rest!
Avoiding collision to raised components is critical, for this we have both valve nozzle inner diameter and outer diameter (ID/OD) visible while you teach (above left) to ensure that when you teach on the board the nozzle will not contact any raised components.
Transparent coloring allows for easy to view component coating to ensure that the coverage past critical components are acceptable to your process.
Cycle time is calculated o· ine when programming to ensure you can optimize your coating process without the need of executing on a machine.
Material volume calculations will show the user the projected amount of material per board based on their program, this also serves to indicate if the program complies with process quality metrics of required materials.