How to achieve zero stencil defects
Controlled paset depositionThrough Mycronic’s fully integrated 3D solder paste inspection and jet printing solution, you can automatically eliminate your stencil defects.
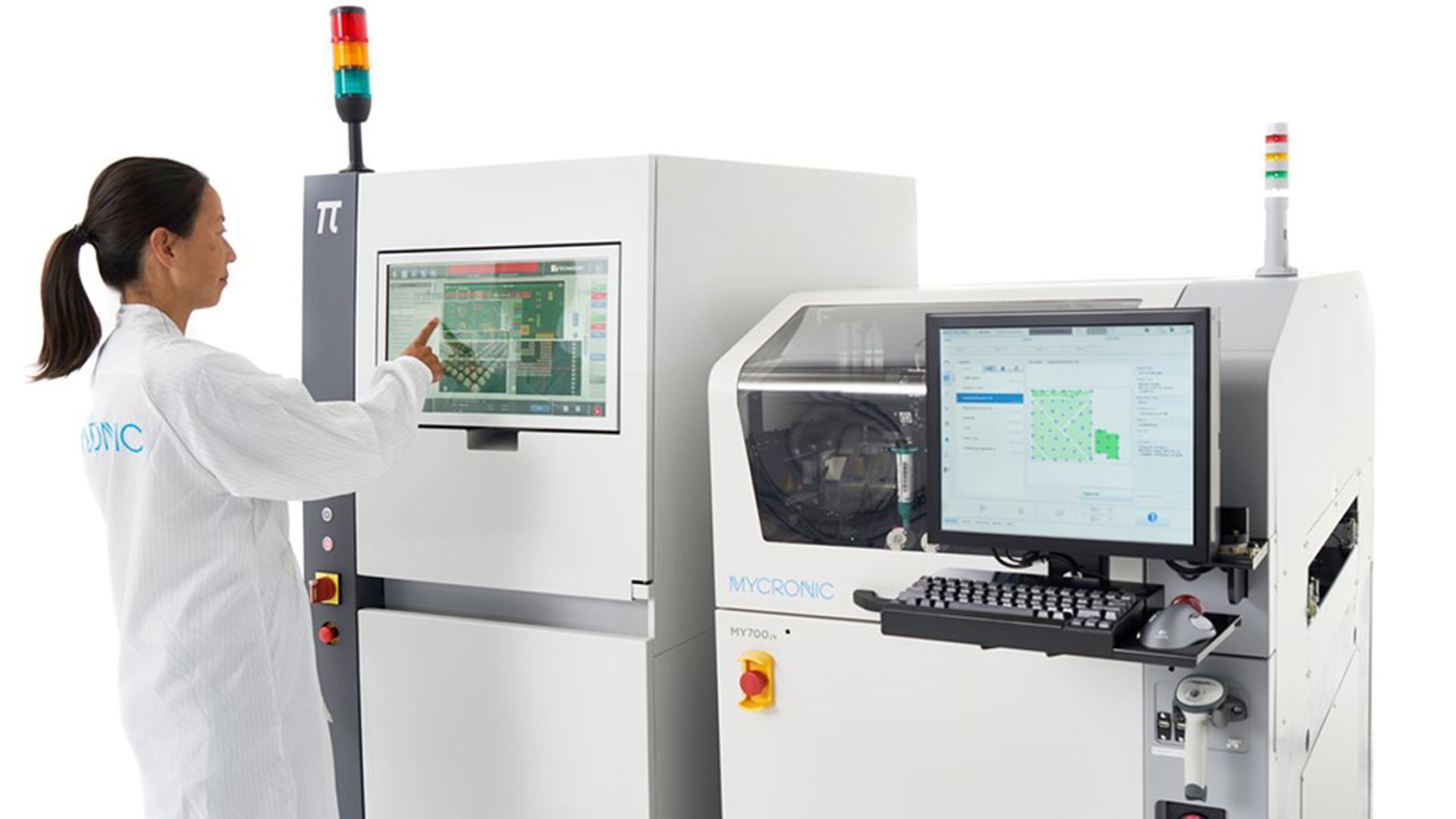
No worries, no compromises
Every manufacturer with stencil printers faces a number of difficult trade-off s: between continuity and quality, small and large components, and thin and thick stencils. All too often, this results in a wide SPI threshold for solder paste volume in order to avoid false calls and keep production fl owing.
These challenges are especially acute for manufacturers of automotive and power electronics, whose PCBs might contain 80 percent chip components, together with an array of large, high-voltage components, or vice versa. The MY700 and 3D SPI add-on solution eliminates the need to compromise stencil thickness by automatically applying the deposits wherever they’re needed most.
As Viktor Olsson, Product Manager Jet Printing, explains, “with closed-loop horizontal communication between the screen printer, SPI and Jet Printer, you get the automatic precision you need for whichever stencil thickness you choose. If it’s a 75-micron stencil, it can jet more volume on top to compensate for the larger components. If it’s 200 microns, it jets all the small dots you need. And for any other issues, it automatically inspects and repairs individual deposits with the industry’s highest precision.”
Bigger production volumes, bigger opportunities
This level of control represents a huge opportunity for high-volume manufacturers, where an FPY improvement of even a fraction of a percent can have a major impact on profitability, quality and delivery times. “The ability to simplify stencil designs and automatically correct any difficult deposits at high speeds is really an industry first,” says Tomas Stetter, Sr. VP Assembly Solutions.
“Wherever stencils are involved, our solution can increase total yield, first pass yield and overall line utilization both immediately, and over time. When it comes to taking the next step towards Industry 4.0, there’s really no simpler, more trouble-free way to improve the quality of the solder paste application process in these extremely demanding environments.”