Say hello to Leo the robot!
Automating material handling through roboticsStock accuracy, traceability, and timely delivery of parts are key aspects of a material handling system. Today, most factories still rely on manual handling of electronic components. In the best case with the support of unique barcodes for parts and a tight software integration to a MES or ERP system. To further increase factory productivity, improving the business, a higher degree of automation is required. This is a trend already ongoing among electronic manufacturers worldwide.
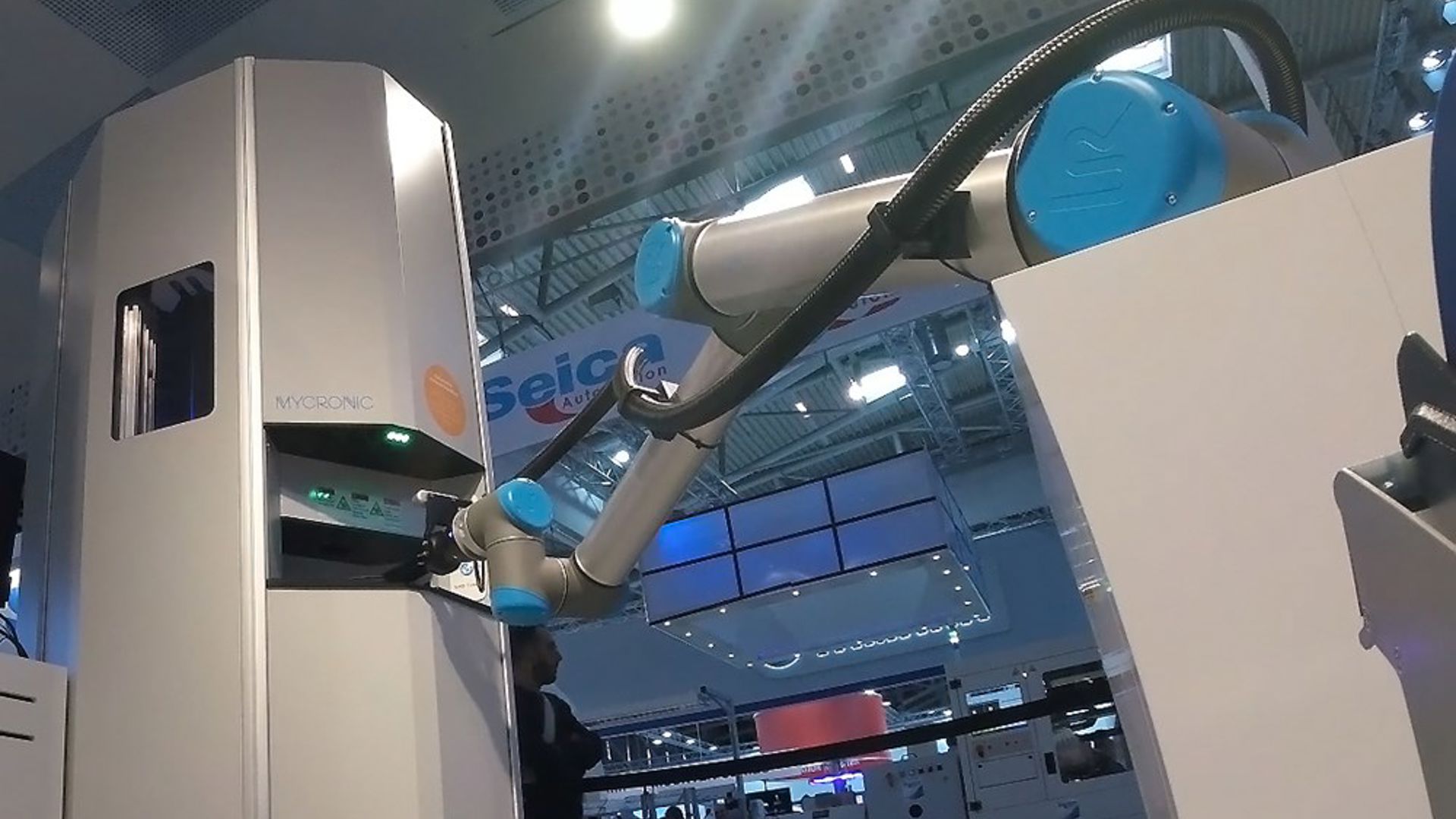
IT IS NOTHING NEW for factories to make use of robotics, however the industry is still expecting a greater focus on automation, and automating what, until now, have been manual process steps in manufacturing. This includes moving electronic components and PCBs efficiently to and from the SMT assembly line. A process improvement that will require more novel storage systems and planning software for automatic inventory control and material tracking together with an increased use of robotics, such as automated guided vehicles (AGVs) and collaborative robots.
Last year at the tradeshow Productronica Mycronic showcased what a fully automated material handling system can look like. The solution encompassed the intelligent storage solution SMD Tower, AGVs and a robotic arm delivering higher efficiency with less human intervention.
Products used in the Productronica demonstration
|
Mycronic believe in a smarter material flow through intelligent material handling. In highmix SMT assembly, the time in between jobs is significant and should be as short as possible. Having an automated material flow can greatly reduce the overall kitting time and thereby minimize changeover cost.
Through the integration of a robotic arm and an AGV, electronics manufacturers can load and unload reels from the SMD Tower, and distribute them to their respective kitting areas without human intervention.
The solution — how it works
A single carrier (reel) or a list of carriers for a complete job is requested from one or more SMD Towers. The towers start to unload reels and the robotic arm will pick reels from the tower terminals and place them into bins in the correct kitting order on the AGV. When the bins are fully kitted with reels, the AGV transports the bins to the kitting area. In the kitting area, the bins are placed into magazines and are then ready to be used on the SMT assembly line.
The robotic arm has a special gripper that allows it to pick all sizes of reels and the AGV has been programmed to always be waiting in the same location. A vision system on the robotic arm is used to accurately locate the position of the AGV relative to the robotic arm. This ensures that the reels are placed accurately in the bins at a high speed.
Reaping the benefits of automation
A key objective for manufacturers automating the PCB assembly process, is to improve both productivity and equipment utilization. As an example, automating material handling results in fewer operators required to manage the flow of electronic components and circuit boards to and from the SMT lines. This makes it possible for operators to focus their work on more value adding tasks in the factory — a process improvement leading to a more optimized material flow as well as lower operational costs.
Another aspect of this process improvement is that it reduces bottlenecks, as this automated solution constantly loads reels into the SMD, preparing for upcoming jobs. This means material is ready on time when you need it at the kitting station. It also reduces material handling errors, such as misplaced reels or retrieving the incorrect reel from stock. In addition it greatly improves the retrieval time for reels when kitting. All in all, the benefits are manifold and cost savings great.
Automated material handling will help manufacturers capture and create more value in tomorrow’s demanding production environments.