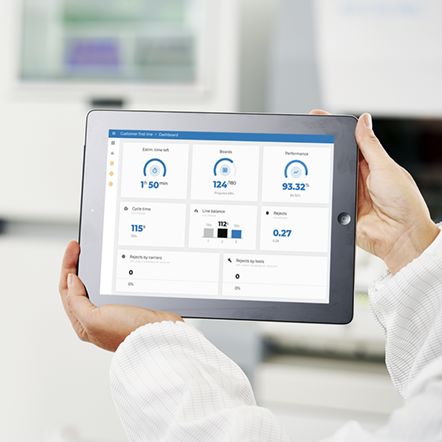
MYCenter Analysis
- Utilization Higher utilization and uptime
- Reject rate Lower reject rate and less waste
- Intervention Less operator intervention
- Ease Ease of use
- Production Higher output
Think bigger. Dig deeper. Act faster.
Now there’s a better way to take control of production performance. The MYCenter Analysis dashboard software gives you the actionable data you need to increase utilization, reduce reject rates and improve line balancing in real time.
Higher-level insights
Improved efficiency starts with the right data. In Live View, the MYCenter Analysis dashboard shows the current state of the line, number of boards produced, cycle time, efficiency and workload balance. Directly from the web-based dashboard, you can compare current utilization with historical data, plan necessary interventions and continuously refine production efficiency from anywhere, on any device.
Deeper problem-solving
With component mispick and reject analysis, MYCenter Analysis makes it possible to diagnose root causes before the problems multiply. When an uncommonly high reject rate is discovered, production engineers can click through an extensive reject rate analysis, examine data and review detailed images of individual mounthead nozzles and components.
Thanks to detailed utilization data, potential bottlenecks can also be identified beyond the pick-and-place machines in both upstream and downstream production. With the right analysis, it’s possible to reveal issues that slow down the line including excessive waiting times for PCBs arriving in the line, solder paste issues detected in the Solder Paste
Inspection system or full PCB magazines at the end of the line, to name just a few. MYCenter Analysis makes this debottlenecking process faster, more effective and more thorough, thereby significantly reducing the need for trial-and-error diagnosis.
Better line balancing
As products and production processes grow more complex, effective line balancing has the potential to deliver huge productivity gains. MYCenter Analysis makes it easier to discover inefficiencies due to frequent machine stoppages as well as reduced speeds in the mounting or feeding of components. In cases where MYPlan is not being used, the software can also high-light instances where a more optimal kitting setup might be possible.
Faster results
Thanks to faster diagnosis of even the smallest problem areas, production managers can more effectively plan key steps and reduce machine stoppages to a minimum. Improved maintenance of component and package data, together with optimized feeder composition and loading, further contribute to more effective line balancing throughout the production process.
Brochure
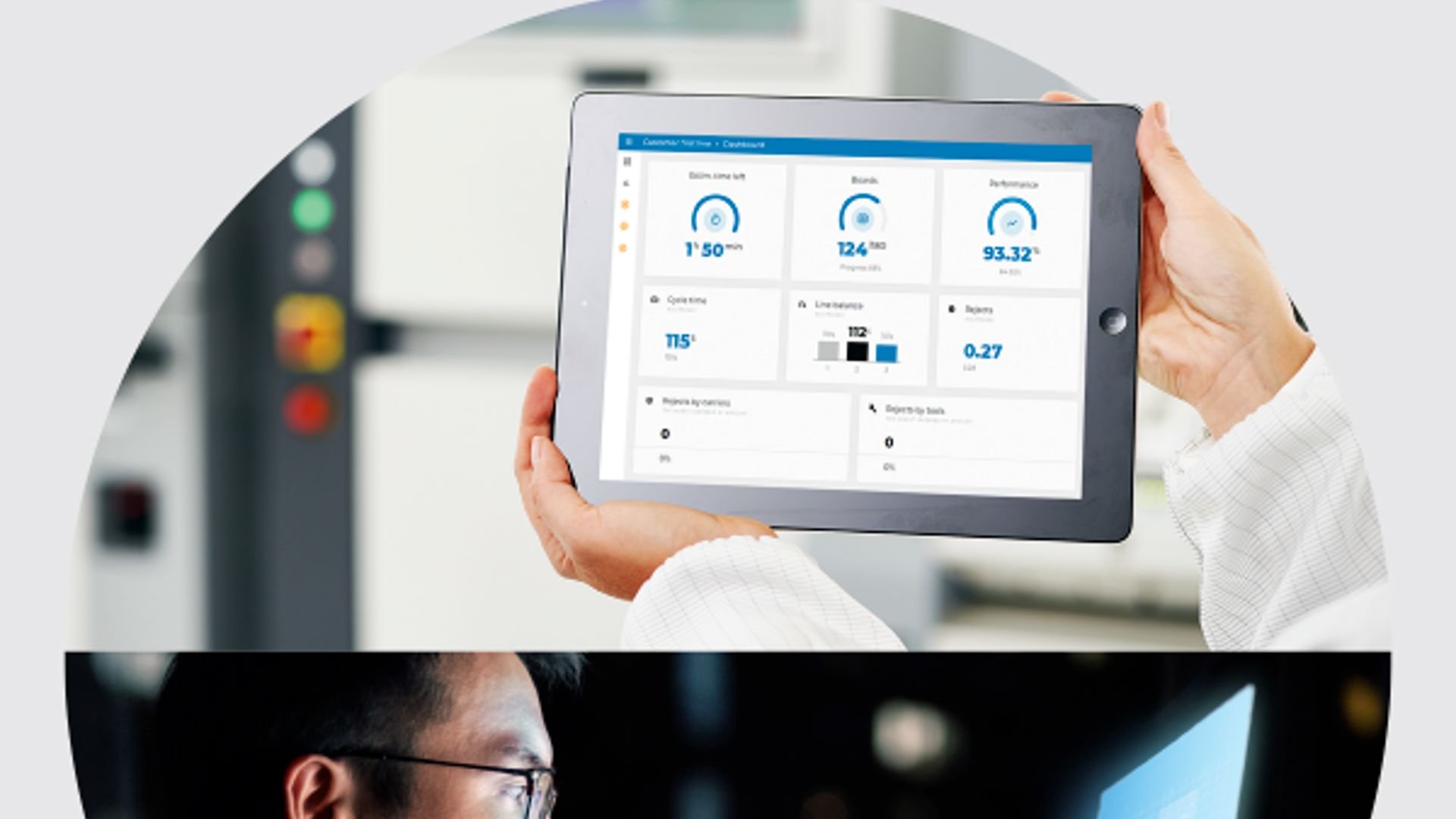