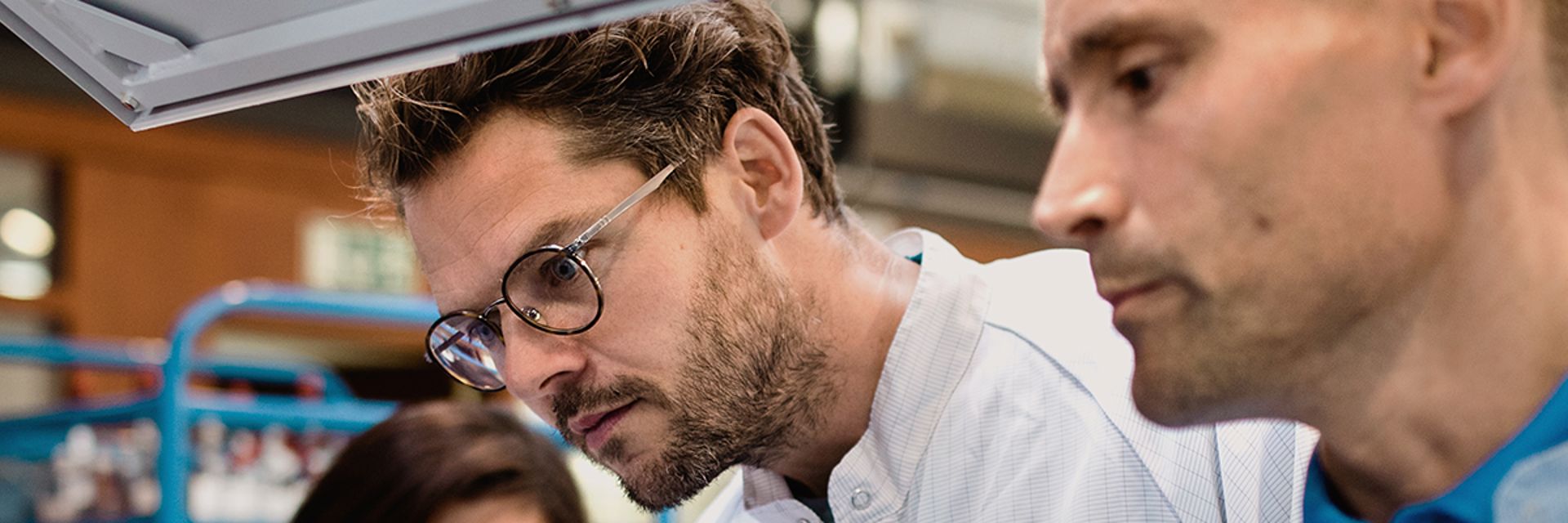
Case stories
The following customer case stories provide insight into the quality and reliability of the equipment and PCB assembly solutions offered by Mycronic.
Customers have praised Mycronic’s machines for enabling efficient and effective assembly processes, as well as our knowledgeable and attentive staff. One customer even noted that with Mycronic they were able to decrease assembly time and repetitive manual work, resulting in increased production volume.
Mycronic's team of experts is always willing to go the extra mile to ensure customer satisfaction. With Mycronic, customers can trust that their assemblies will be completed on time and to the highest standards.
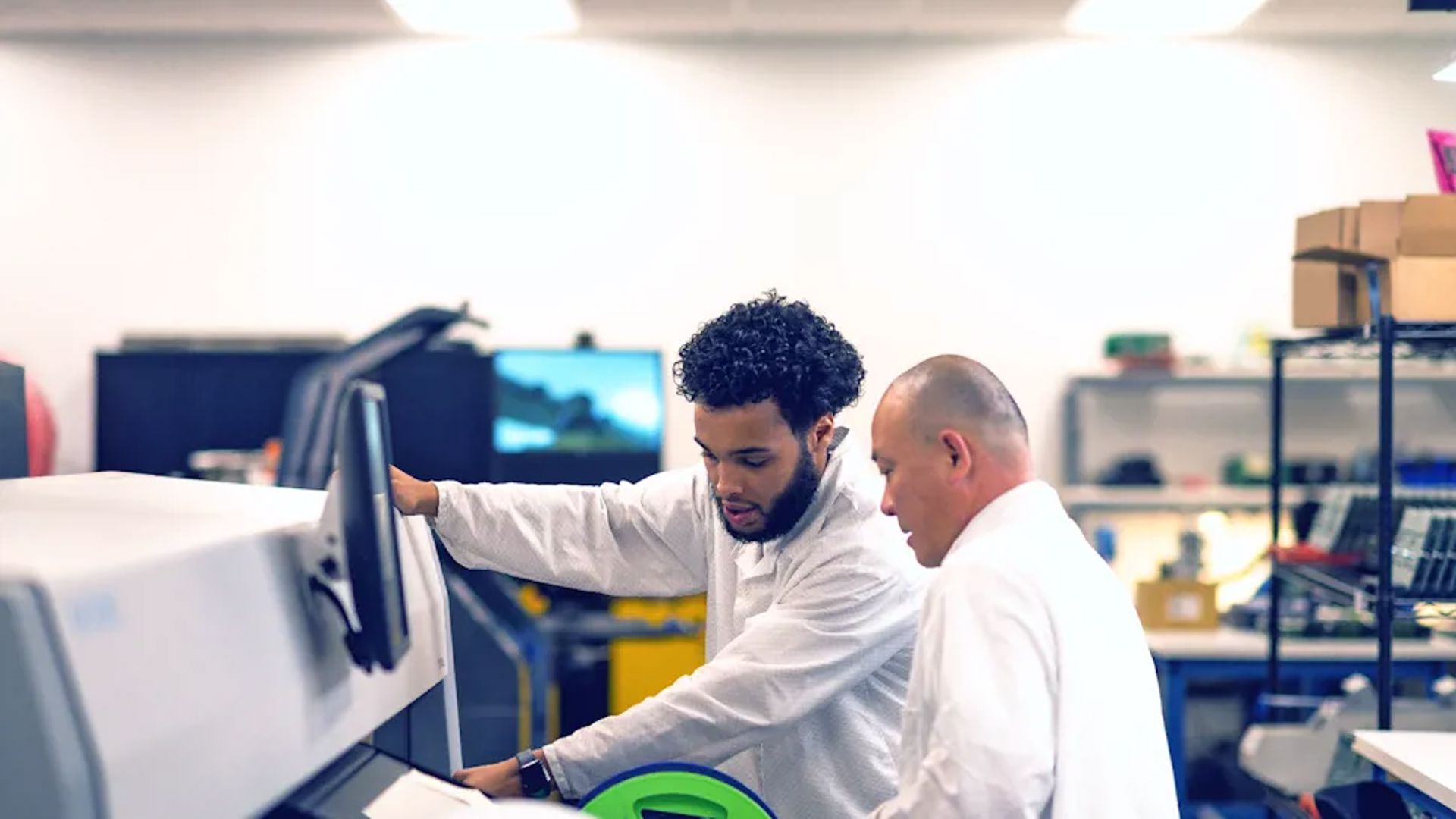
More growth, less pain
How one Silicon Valley company is accelerating the design-to-manufacturing cycle. As their client base and production volumes have expanded, Mycronic equipment has played a central role in the quality, flexibility and production scalability that the company is able to provide.

A showcase stockroom
In the world of rapid prototyping, speed and accuracy are everything. And everything starts in the stockroom. Based on this insight, California-based XLR8 has built a strong reputation for best-in-class material flows thanks to a comprehensive integrated material handling system from Mycronic.
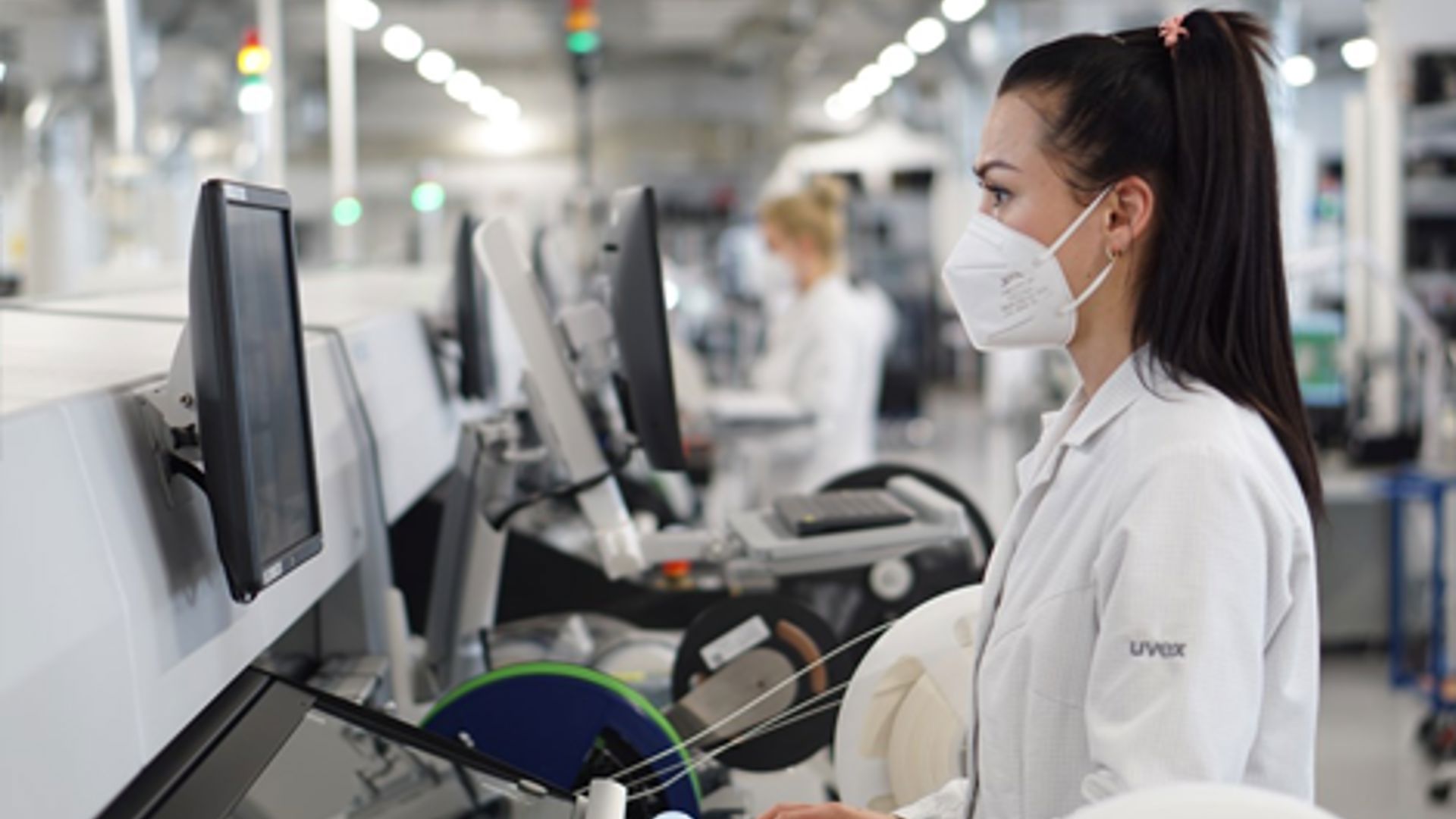
Smaller, smarter, faster
Just outside of Nürnberg, Germany, one forward-thinking manufacturer is rapidly modernizing its production to meet fast-growing demands for advanced industrial IoT electronics. Thanks to the latest full-line assembly solutions from Mycronic, mikrolab can now respond to global competition with greater speed, quality and cost efficiency than ever before.
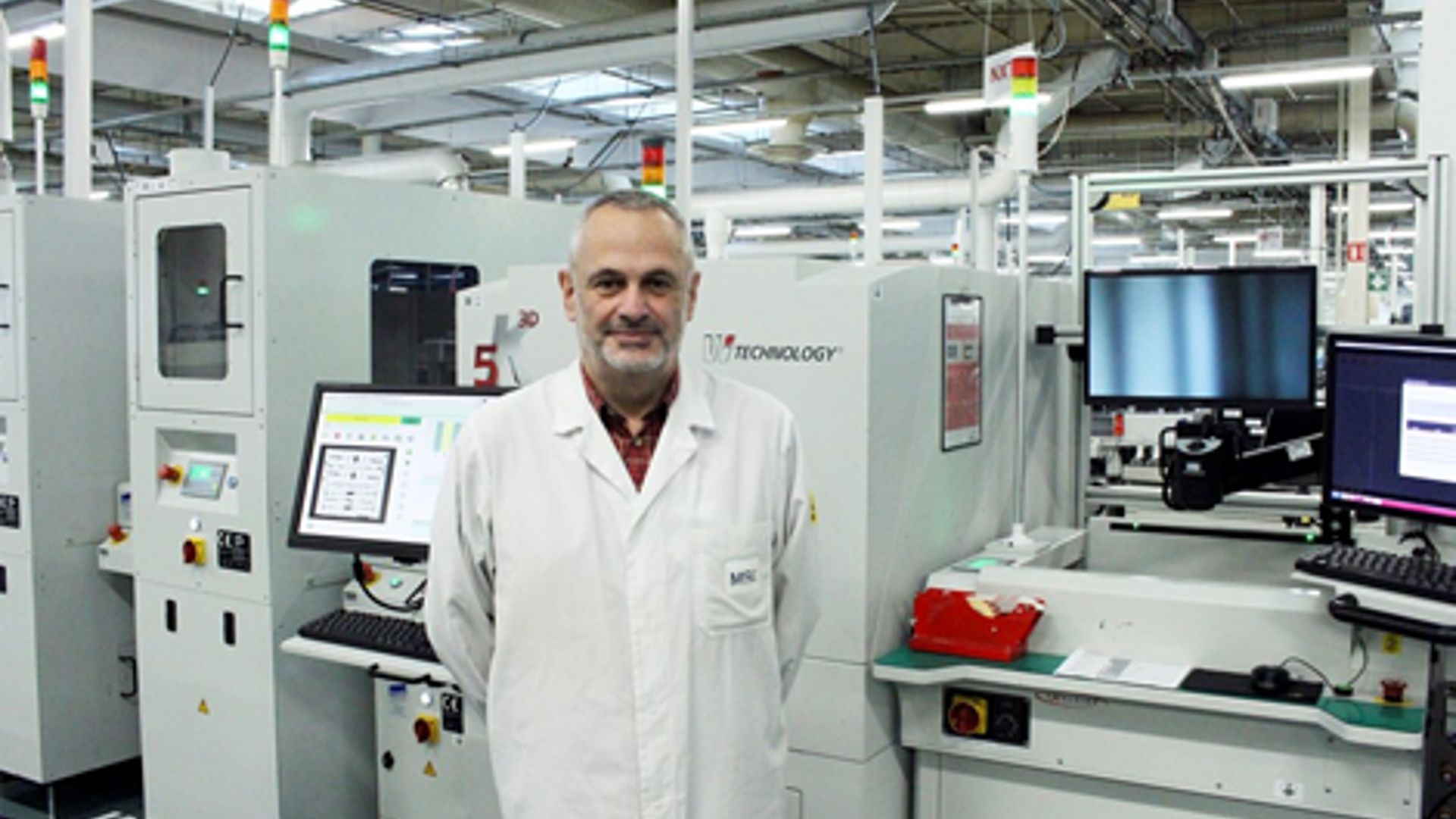
Autonomous inspection
21st century industries demand 21st century manufacturing solutions. With the help of the latest 3D automated optical inspection systems, MSL Circuits – an ALL Circuits company, is helping leading automotive manufacturers make a flawless transformation to the era of electric vehicles.
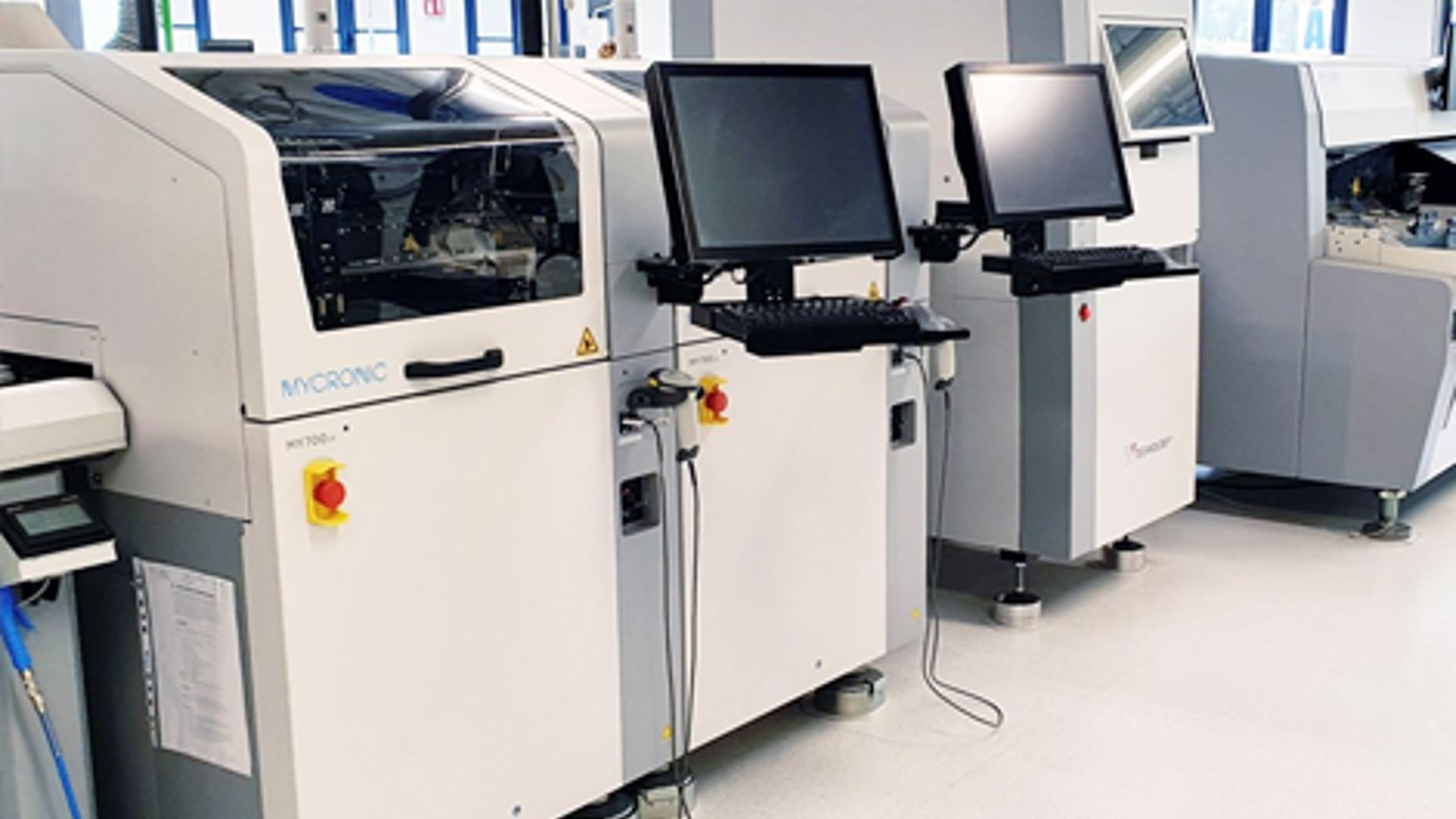
Putting performance data to work
As an innovative European contract manufacturer, DF Elettronica is determined to continually push the limits of automation. Whether it’s inspection, traceability, material transport or process optimization, the application of highly advanced technologies has been central to the company’s successful production strategy for many years. MYCenter Analysis is just the latest in the ongoing pursuit for the optimal high-flexibility production environment.
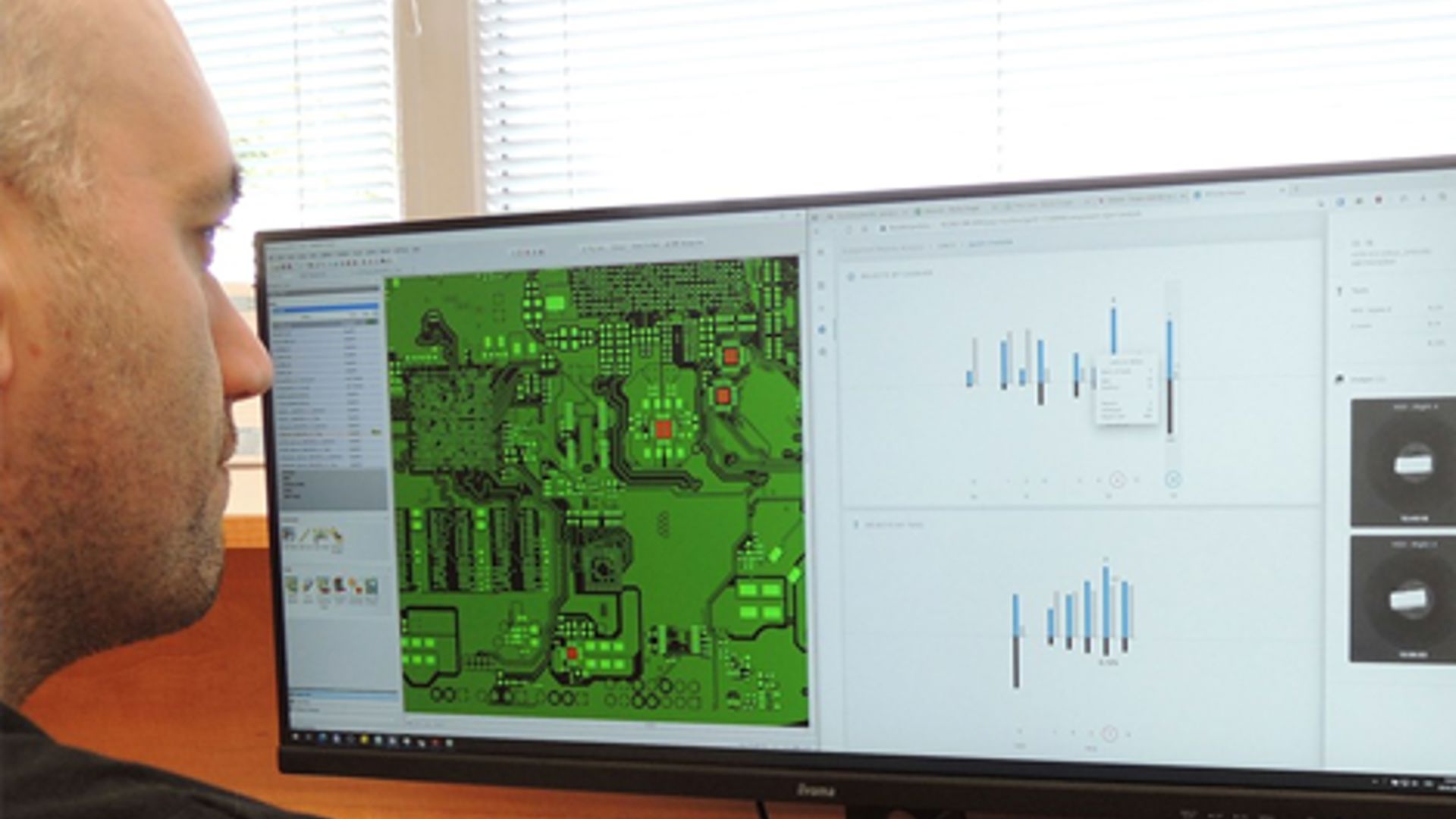
Analysis made easy
For a savvy production manager, it’s always possible to get the right troubleshooting data from your pick-and-place machine – if you have plenty of time and effort to spare. Thanks to MYCenter Analysis, the supervisors at one electronics manufacturing facility can get the statistics they need at a glance, without ever leaving the office.
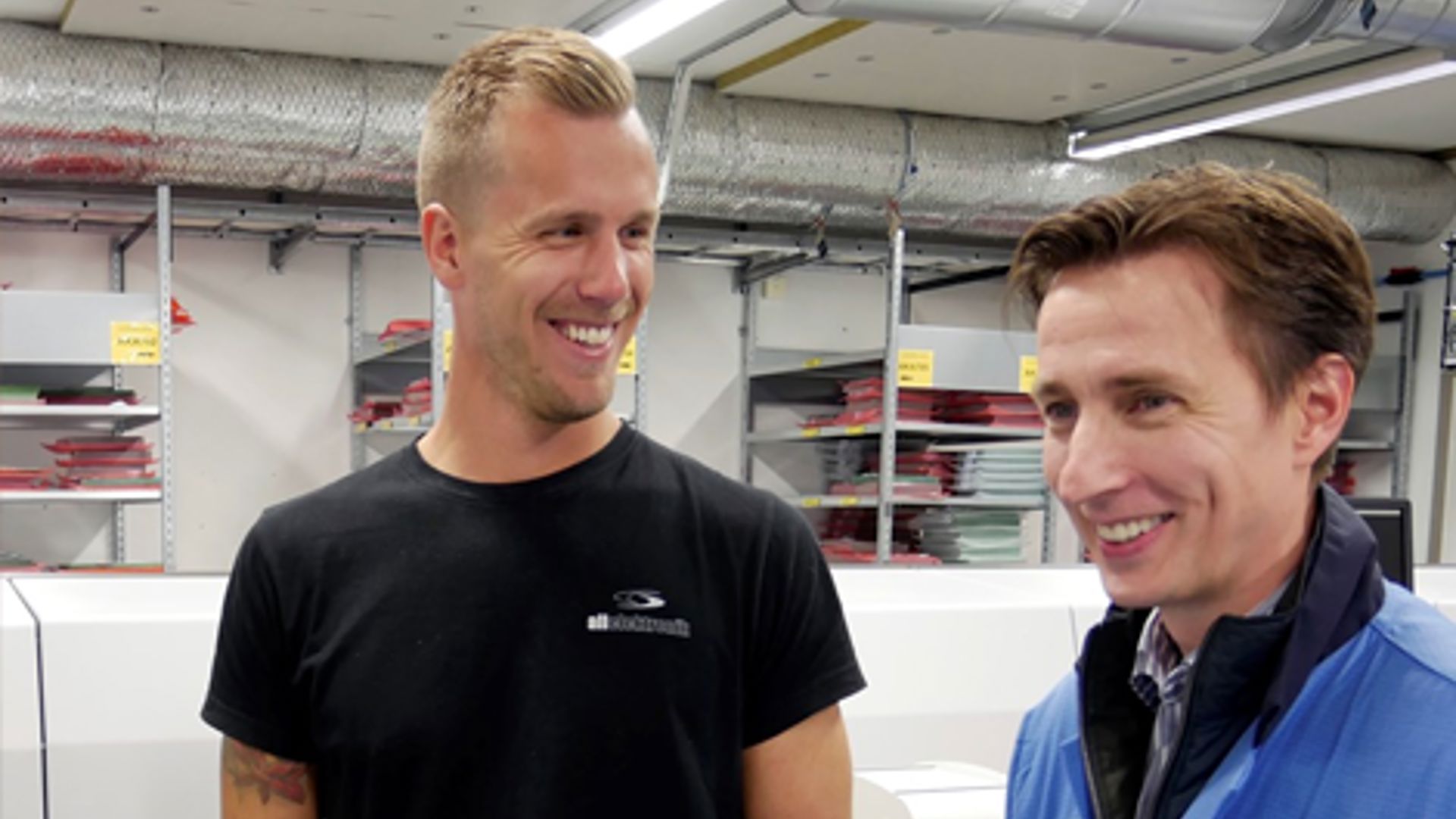
Surprising insights
For Allelektronik in southern Sweden, the new MYCenter Analysis dashboard came as a real eye-opener. Having spent more than a decade optimizing production for a single customer, Production Manager Mats Landström was thrilled to see things from an entirely new perspective. “We really didn’t know if the software would be useful at first,” he says. “Now we can’t live without it.”
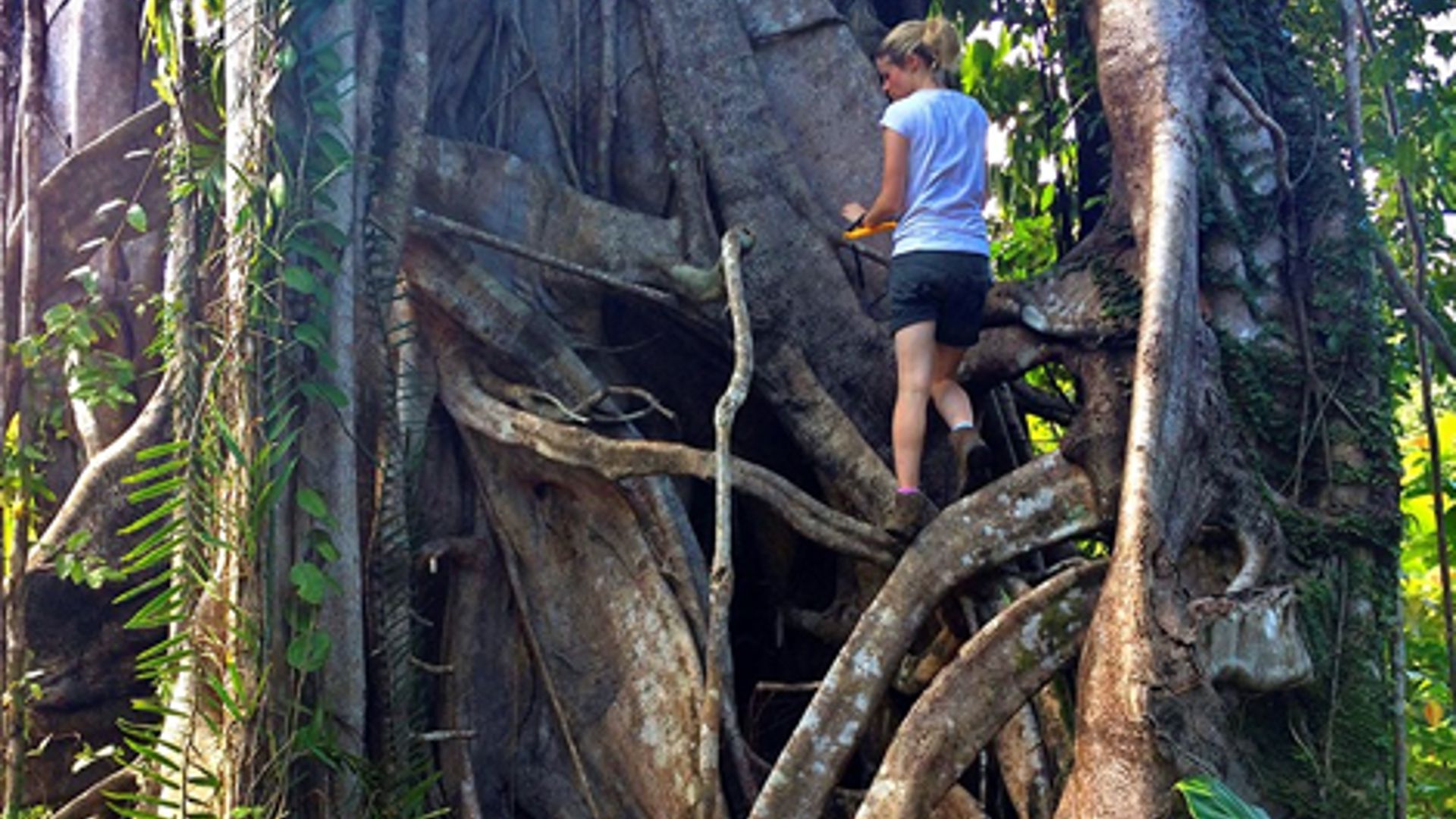
A high-tech future down under
At its headquarters in a high-tech industry hub in Brisbane, Australia, Elexon Electronics is investing in the future of advanced local manufacturing. For CEO Frank Faller, this means finding new solutions to turn ideas into products faster, smarter and with the highest quality.
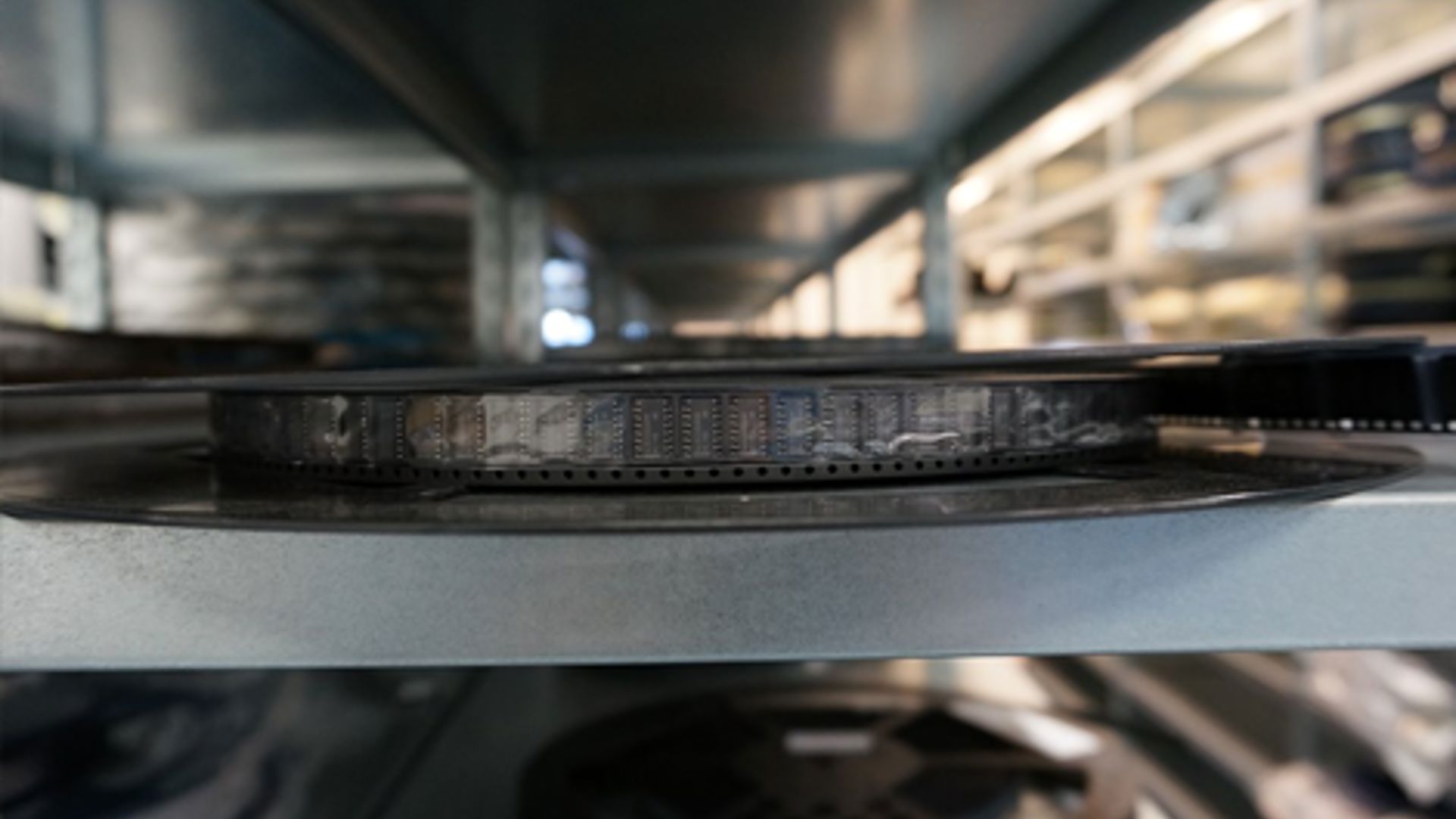
Smarter growth in the SMT factory
What happens when business is growing, components are shrinking, and both staff and production space remain the same? A visit to Allelektronik shows that the answer lies in the thoughtful development of smarter planning systems, advanced equipment and cutting-edge automation solutions.