The perfect solder joint
Screen printing has certainly served the industry well, and gave manufacturers virtually limitless throughput speeds for long series production. But not without trade-offs.
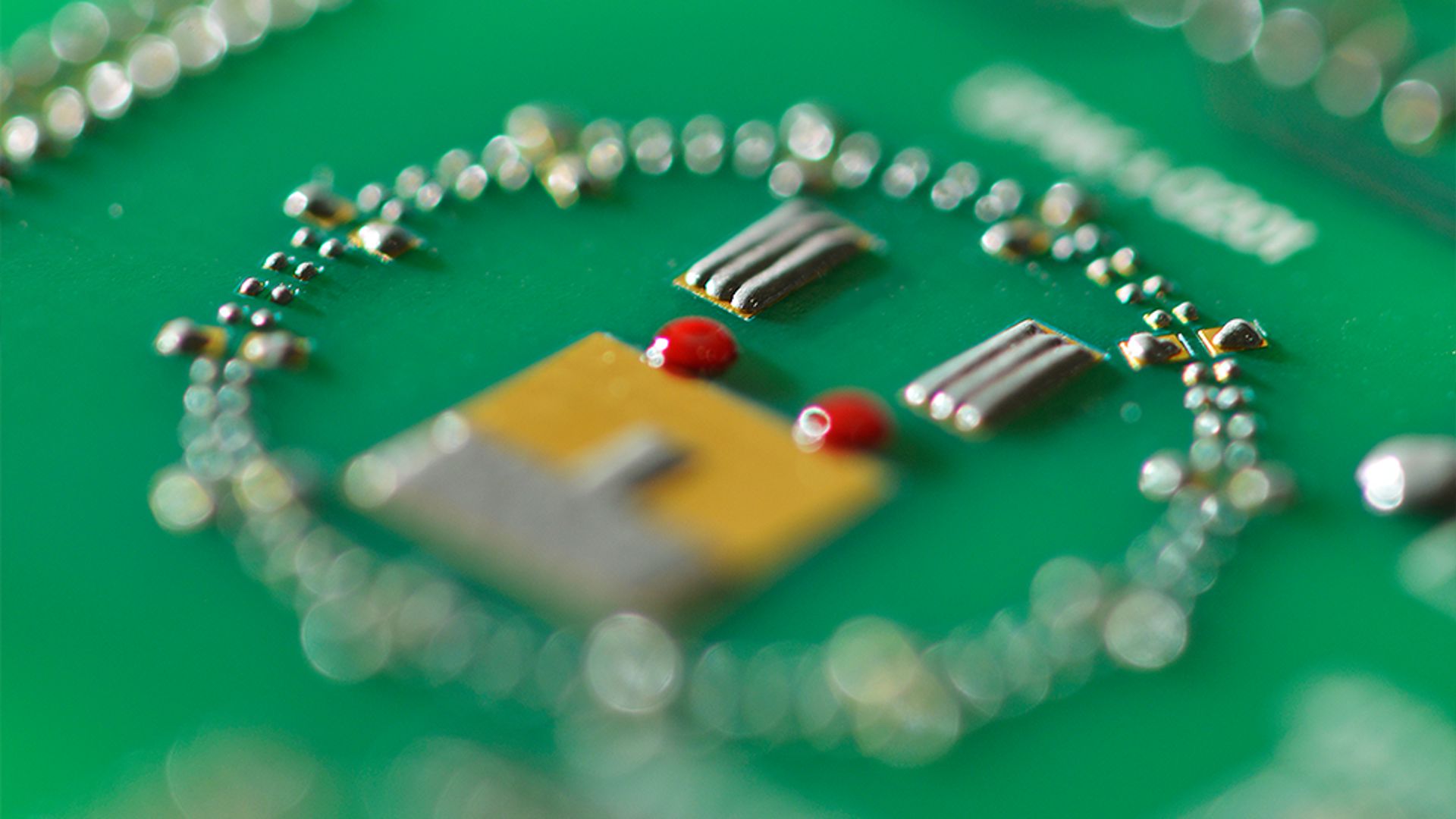
Challenge
For frequent changeovers, the cleaning and storing of stencils instead drives costs up and is a source of errors. And trying to solve today's production challenges with yesterday's solutions is hardly the way to deliver excellence.
In fact, a significant majority of all PCB defects can be traced back to the screen printing process. At the same time, manufacturers all over the world are being compelled to act in order to keep up with the trend towards high-mix production without compromising on quality.
Solution
Import, optimize and print on demand
The MY700 Jet Printer puts you way ahead of the competition and constitutes a giant leap towards more flexible and profitable production. Jet printing replaces screen printing, and allows you to respond rapidly to your customers' demands and changes while achieving superior accuracy for every solder joint. There's simply no time wasted ordering, changing or storing stencils, and far less risk of human error due to a minimal need for operator intervention. Just import CAD or Gerber data, optimize for individually challenging components, and cut your response time down to hours or minutes instead of days.
Engineered for the most complex boards
Jet printing makes it possible to handle the latest, most challenging designs and components while getting the most from your existing production line. Where screen printers struggle with broadband technology, board cavities and board stretch, jet printing delivers perfectly shaped dots with full volume control time and again. Because jet printing allows operators to adjust dot sizes according to the mix of components, placing a smaller component next to a D-PAK for example has never been easier, or more precise.
Jet printing
Each component gets the right amount of solder paste. Always perfect joint.
Promise
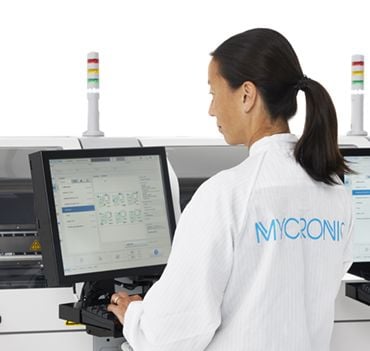