50 years in the mix
Simplifying high-mix manufacturing for more than 50 yearsIf there’s one constant in PCB assembly, it’s change itself. Whether it’s fast-changing product mixes, components or material flows, Mycronic customers have led the way, bringing complexity under control for more than 50 years.
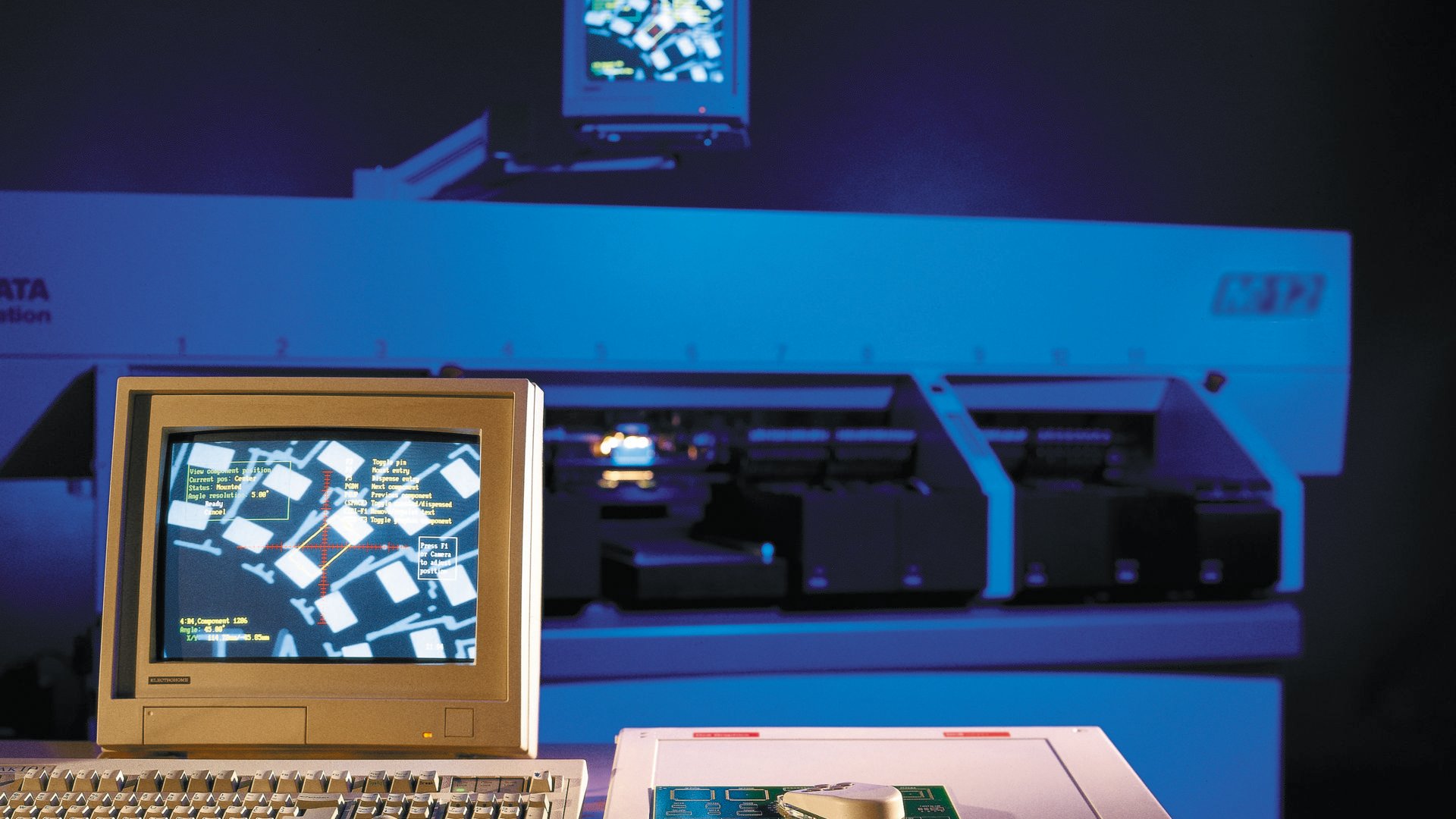
A technology shift is born
Until the early 1980s, through-hole components were the standard in PCB manufacturing. But as demand grew for smaller, more compact electronic devices, surface mount technologies created new opportunities for higher component density and improved performance.
Into this gap stepped a small company from Sweden. Its first systems, which applied a rapidly moving beam of light to show the operator where to mount components, made it possible for advanced manufacturers to manually assemble circuit boards with greater accuracy and flexibility. It would be the starting point for a long line of industry-shaping innovations ranging from flexible pick-and-place systems and solder paste jet printing to fully automated production lines.
Agile assembly at its most complex
“The transition from through-hole to surface-mount opened the door for us in the beginning,” says Robert Helleday, Head of Research and Development at Mycronic. “Of course we weren’t alone, but our focus was unique. Whereas most of our competitors sprang out of the big players’ in-house production, we came from the small-scale production field and everything we did was focused on these customers. They were short-series producers building advanced computers. They were the big French and American aerospace developers. In most cases their production was extremely advanced, and their components were very expensive.”
These producers relied heavily on rapid prototyping cycles and complex, high-density assemblies. As Mycronic’s core pick-and-place technologies evolved, fast changeovers and powerful process control systems were therefore essential. “We more or less grew up together with these customers,” says Robert. “So as our solutions became faster, more automated and software-driven, we stayed in tune with their day-to-day needs.”
Changing the game
For high-mix manufacturers in the late 90s and early 2000s, the cost and complexity of job changeovers was a major barrier to profitability. Most component feeders on the market were heavy, bulky and required regular maintenance. Their feeder positions were fixed. And most required full component reels, leading to significant waste of unused component strips.
Just-in-time thinking
Mycronic’s solution was the Agilis™ feeder system: a compact, interchangeable, zero-maintenance feeder concept. It represented the best of Mycronic’s thinking, setting a new standard for fast and flexible kitting and loading. “This principle is really central to everything we do,” says Robert, explaining how ‘bi-directional material flows’ suffused all the company’s innovations in material handling and automated storage.
“You can’t just keep feeding your machines because you don’t always exhaust your whole reel,” he explains. “You bring things in and out of storage and the timing, tracking and tracing of all these flows is a huge contributor to profitable, agile manufacturing. It’s an integrated workflow that’s crucial for just-in-time production. You need to be able to call up the material and get it onto a board or back into storage with as little human intervention as possible.”
The Agilis feeder system was an instant success, becoming a trademark symbol for agile assembly. Over time, other process steps would go through the same fundamental rethinking. And solder paste printing was just such an application that was ripe for innovation. “It’s an interesting story,” says Robert, “and once again, it was totally driven by customer demands.”

How do you go from a squeegee running across a sheet of metal to a fully software-controlled, high-speed jetting system with nanoliter accuracy?
Precision printing at jet speed
The idea for solder paste jet printing emerged when a long-time French customer approached Mycronic with a seemingly insurmountable task. “They told us: ‘We’ve always had this great pick-and-place machine, but it would be amazing if my printing could be this flexible’,” says Robert. “The thing is, everyone thought it would be impossible. I mean, how do you go from a squeegee running across a sheet of metal to a fully software-controlled, high-speed jetting system with nanoliter accuracy? It took a real long-term R&D initiative, but we managed to create the first jet printer. Even now, 20 years and several machine generations later, no one has emerged with any technology that’s even similar.”
We’ve always been a bit of a challenger: When someone tells us it’s impossible, that just pushes us to think bigger.
Challenging conventions
According to Bobbi Ferm, Chief Engineer and Systems Architect at Mycronic, the introduction of jet printing is emblematic of the Mycronic culture. "We've always been a bit of a challenger," he says. When someone tells us it's impossible, that just pushes us to think bigger. You can see this with our pattern generators as well as with our assembly solutions. We’ve identified clear opportunities, however challenging they might be to solve. We’ve made the right big bets. And they’ve really paid off for our customers.”
Shorter series, bigger profits
Today, Mycronic has grown together with its customer base, providing solutions for every process step from bare board to finished, inspected and coated PCB. These automated full-line solutions make it possible for smaller producers, contract manufacturers and in-house production teams to rapidly iterate new products and deliver value that can’t be achieved by high-volume manufacturers overseas.
“It wasn’t always obvious that advanced automation would be the way to go for these high-flexibility producers,” says Robert. “About 15 years ago, everything was supposed to move to Asia. But for those who stayed despite higher labor costs, we’ve stuck with them and effectively become an extension of their businesses. We’ve been great at supporting these customers and keeping them profitable with short-series production.”
Data-driven assembly
If, twenty years ago, hardware was a major obstacle to rapid job changeovers, today it’s often software. Which is why Mycronic has focused in recent years on simplifying everything from program creation and fine-tuning to inspection review. With the help of advanced machine learning and deep learning systems, manufacturers can now automate a range of repetitive programming and fine-tuning tasks.
Today it’s the person telling the machine what to make. Tomorrow it should be the product telling the machines what it wants to be.
“We’ve come a long way in connecting the software in the pick-and-place to the whole line,” says Robert. “When all our machines work better together within a single workflow, and when they all learn from and improve each other, that’s exciting! Today it’s the person telling the machine what to make. Tomorrow it should be the product telling the machines what it wants to be.”
In solder paste printing, this level of machine-to-machine automation is already here. By combining jet printing, screen printing and solder paste inspection, Mycronic now enables zero-defect printing — an industry first — in which the inspection system serves as a virtual auto-correct for any missing deposits. “It’s getting to the point where customers shouldn’t even notice the hardware,” says Bobbi. “It’s mainly the software they interact with, so we’re gradually bringing the entire production line into a single, intuitive operating system.”
Turning up the volume
Despite all the advances in software, Bobbi remains proud of the engineering behind every new machine. “The absolute best moments in my career have been at 9 AM in a trade show, when the PA announces the opening of the event. After years of hard work, it’s a proud moment when you show a new machine to the world,” he says. “Just last year we released a new high-speed mounthead technology, the MX7, at Productronica. Everyone I met was thrilled about the possibilities it opens up for high-throughput, longer series production.”
The circle continues
It is, after all, pick-and-place equipment that remains firmly at the heart of many customers’ production strategies. And Bobbi is confident that Mycronic machines are uniquely equipped for whatever changes the future might bring. “The pick-and-place machine is like a puzzle: you can build and integrate it how you want. If new technologies emerge, we make it easy to integrate a new magazine, a new nozzle or the latest software. I just recently met a customer with a machine we introduced in 1999, and 23 years later it could still run the latest software. Maybe we had to change out a camera module, but this is still a much longer lifespan than almost any other machine in the industry.”
It’s a constant creative process together with some of the world’s most advanced manufacturers – and that’s the real motivation.
“This is true modular thinking,” he concludes. “It’s circular thinking. And this, I think, is one of the keys to our longevity. We all know high-mix will continue to grow. And innovation cycles will continue to accelerate. But we keep helping our customers adapt and evolve with the lowest cost and least possible effort. It’s a constant creative process together with some of the world’s most advanced manufacturers — and that’s the real motivation at the end of the day.”
Text: Grant Baldrige, Open Communication.
FACTS
Mycronic High-Flex division in brief
- Installed base in more than 50 countries
- Manufacturer of full-line PCB assembly solutions including solder printing, pick-and-place, inspection, component storage, dispensingand coating
- Inventor of the zero-maintenance Agilis feeder technology
- Inventor of jet printing technology for high-speed solder paste jetting