Breaking the displays barrier
A look behind the mask in a world driven by displaysIn 1974, the world’s first prototype for a flat, active-matrix LCD was demonstrated. Yet, without a technology capable of mass-producing the small, thin transistors behind their pixel arrays, LCD displays might just have remained in the laboratory. Five decades later, this early innovation has evolved into an industry worth more than USD 133 billion per year. That’s 272 million square meters of LCD and AMOLED displays produced every year for everything from TVs and car displays to computers and mobile devices. At the heart of this revolution is a technology designed and built in Täby, Sweden.
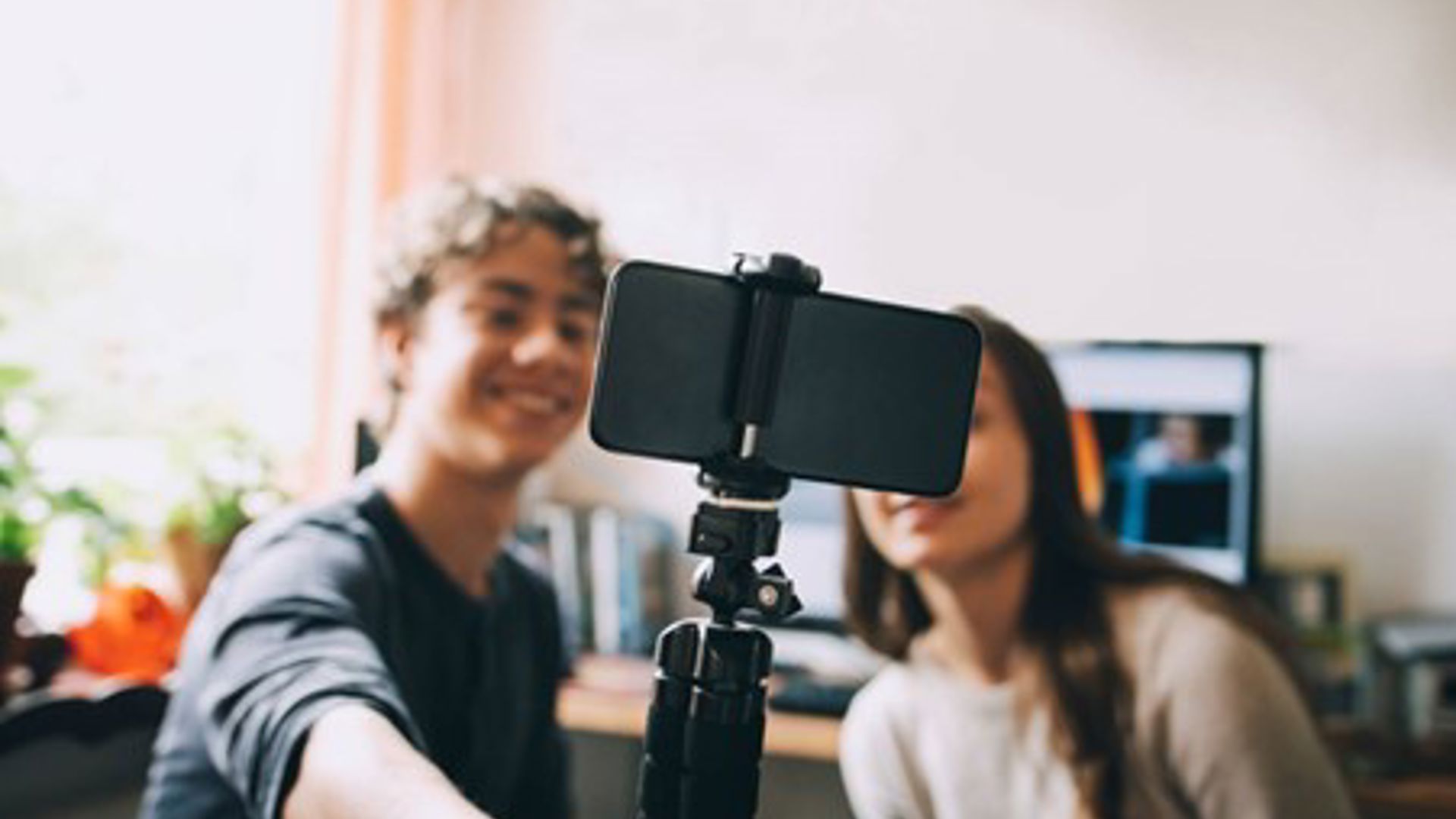
What’s in a pixel?
Seven hours per day. This is how much the average person has grown to rely on display technologies. Yet few of us pause to consider what goes on behind every pixel in every screen we use to work, communicate and play.
Take the screen you’re reading this on. Before it was assembled, it began as a photomask. A template to produce each layer of a pixel array, that photomask contains an unfathomable amount of information etched into two square meters of quartz. And it was most likely produced by a Prexision series mask writer from Mycronic.
Precision patterns at massive scale
“The largest photomask we can write today can contain up to 78 terapixels, or 78 trillion pixels. In this context a pixel is the footprint of the laser beams in our writers, 170x170 nm”, says Anders Svensson, Expert, Pattern Generators at Mycronic. “To give a better idea of what this means,” he says, holding up a yellow sticky note, “scale it up and imagine this Post-it note is a pixel. Then line up 78 trillion of them, one by one. This would cover a distance equal to nine return trips to the moon. This is just a massive amount of data, written with extreme precision over a large area.”
1 nm precision with zero defects
Beneath each pixel of a modern display can be ten or more layers of transistors, and each of these layers requires its own photomask. During the laser writing process, every structure is written with a precision of one millionth of a millimeter. Any minute vibration, any imperceptible “blink” of the laser, or any temperature variation more than 0.05 degrees Celsius during a 3-day writing cycle, and the more than $300,000 photomask will be rendered useless.
This is mainly due to the fact that the human eye is capable of sensing the tiniest of defects or misalignments, creating an affect known as mura – a Japanese term meaning “unevenness” or “irregularity”. “The ability to correct for this is especially challenging, and one of the things that makes our technologies unique,” says Anders. “There are mura patterns that can’t even be measured, but that the eye can see. The human brain can even fill in designs and patterns that don’t exist. So, no matter how advanced your metrology, everything comes down to the visual experience.”
Perfecting a complex architecture
If the precision of individual photomasks wasn’t enough of a challenge, each of the 78 trillion pixels also need to be perfectly aligned through the full stack of more than twenty layers of transistors. “To be able to write a pattern and lay a stack of layers,” explains Anders, “you have to compensate for pressure differentials, humidity and countless other variables that can impact the viewing experience. Solving this demands a huge range of specialists in everything from material science and laser physics to mechatronics and systems engineering. So, each one of these machines represents an extreme technical breadth, with everyone pushing the limits from every imaginable angle.”
This is just a massive amount of data, written with extreme precision over a large area
Enabling exponential growth
The pace of technological change can be especially mind-boggling if you consider that global LCD TV sales only overtook traditional cathode ray tube TVs as late as in 2006. In fact, it was around this time that many within Mycronic realized what a major shift their own technologies were enabling.
The smartphone generation
“When the first smartphones were launched virtually no one in the industry thought they would replace all the regular feature phones,” reflects Young Jin Park, Product Manager Pattern Generators. “But it happened in just a few years. And then I realized that displays would truly change the world. I also knew that the Prexision 8 was a major contributor, which made me especially proud.”
Two decades and billions of displays later, Prexision series machines have since accounted for a majority of all displays produced worldwide. An entire generation has now grown up in a world mediated by display technologies created by Mycronic mask writers.
Connecting worlds apart
More recently, when the covid pandemic struck, the ubiquity of displays made it possible to keep the world connected. “Social distancing. Lockdowns. Travel bans. This all changed how people work and communicate,” says Young Jin. “Before that, a display was a display. It could be beautiful. It could be entertaining. But just like that, it became the place where we all interact in the digital world, doing schoolwork, meeting colleagues and catching up with our families. I think that was the moment when a lot of people really recognized how important displays were.”
Leading the way forward
Despite the speed of all this change, Mycronic has remained at the forefront for several decades. “We have to be extremely aggressive in our R&D,” says Anders. “Just taking laser technologies as an example, we’ve moved from one beam to three, to nine, and now to 15 in a single machine— all to improve throughput and cost-efficiency. And just recently, we released a new type of solid-state laser that runs at about 1% the energy consumption of previous lasers. This lowers the energy consumption of the entire system by up to 70%. Needless to say, innovations like these aren’t born overnight.”
Creating the future together
Of course, R&D investments of this scale would be impossible without close customer partnerships. “The market intelligence, the continuous customer collaboration and the joint research with our customers and sub-suppliers — these are some of the most interesting parts of our job,” says Young Jin. “We work closely within the display industry supply chain — not just with the mask shops — and our partners have fabs everywhere from Korea, Japan and China to Europe and the US. Together we identify market needs and future growth opportunities for every customer and its subsidiaries.”
I realized that displays would truly change the world. I also knew that the Prexision 8 was a major contributor, which made me especially proud.
Navigating a fast-changing industry
Often, this means taking a bold leadership role when investing in the development of new pattern generator technologies. “It’s not like in semiconductors,” explains Young Jin, “where the whole industry has a clear roadmap following Moore’s law and everyone in the supply chain follows it. In displays, there is no roadmap. So it’s always hard to know where the market will be in the next five years. But we have to push forward with new platforms anyway.”
The 2018 launch of the Prexision 800 was a perfect example of such a pioneering innovation, says Young Jin. “When we released it, no one in the market was quite sure: ‘Do we really need a system this advanced?’ It wasn’t until years later, at an event with the heads of all our biggest customers, that one stood up and said, ’This machine really helped us take the lead at the top-end of the display market, which is our highest-margin category today.’”
In fact, although LCD displays still account for the vast majority of units shipped, advanced AMOLED displays have grown to generate nearly half of display makers’ global sales revenues. This points to a promising future for the continued evolution of laser pattern generator technologies.
The resolution revolution continues
“Right now the market drivers continue to be better at color reproduction, higher refresh rate with lower power consumption, increasing display sizes for all applications and, of course, higher resolution,” says Young Jin. “We’re already at the point, at a high enough ppi (pixel per inch), where it’s virtually impossible for the human eye to see individual pixels at a typical viewing distance. A high-end laptop is at around 200 ppi and a high-end smartphone is at around 450 ppi, but it won’t stop there. Manufacturers of near-eye displays are already requesting two to four times higher ppi than for smartphone displays, so we’re always pushing the limits.”
With each new mask writer shipped, the resolution revolution will continue. From the first LCD fifty years ago to today’s most advanced flexible, transparent and VR displays, Mycronic remains at the heart of a technological story that is still unfolding.
No matter how advanced your metrology, everything comes down to the visual experience.
“It’s a bit dizzying sometimes to imagine that about 70 mask writers in the world are the foundation for this huge, fast-changing industry that’s now worth over 133 billion dollars,” concludes Anders. “It keeps us sharp, and it keeps us on our toes. Because if we stop developing, so much of this development will stop with us.”
Each year Mycronic mask writers produce photomasks which generate:
- Production of 3.6 billion displays
- Covering an area of 32,000 football fields
- To a market value of USD 133 billion
Mycronic mask writer history in brief
- Early 1990s – Legacy LRS series creates shadow masks and small photomasks
- 2001-2004 – LRS11k & 15k boosts productivity with multiple beams for larger photomasks up to Gen 7
- 2001-2008 – Improved productivity and performance for photomasks up to Gen 10
- 2014 – Prexision 80 introduces new servo design, hardware and software improvements
- 2018 – Prexision 800 enables higher resolution with same productivity