Challenges in High-Volume Manufacturing for Die Attach Systems
Increasing demand for high-volume manufacturing accelerates the continuing adaptation of full automation in advanced eutectic packaging. From the perspective of potential purchasers of die attach systems, this demand level places both general requirements on them and also very specific requirements from the systems they purchase. The general requirements include the need for lower cost manufacturing (which is difficult given increasing labor costs in popular manufacturing bases, such as in China) and the need for a much higher level of automation in the industry.
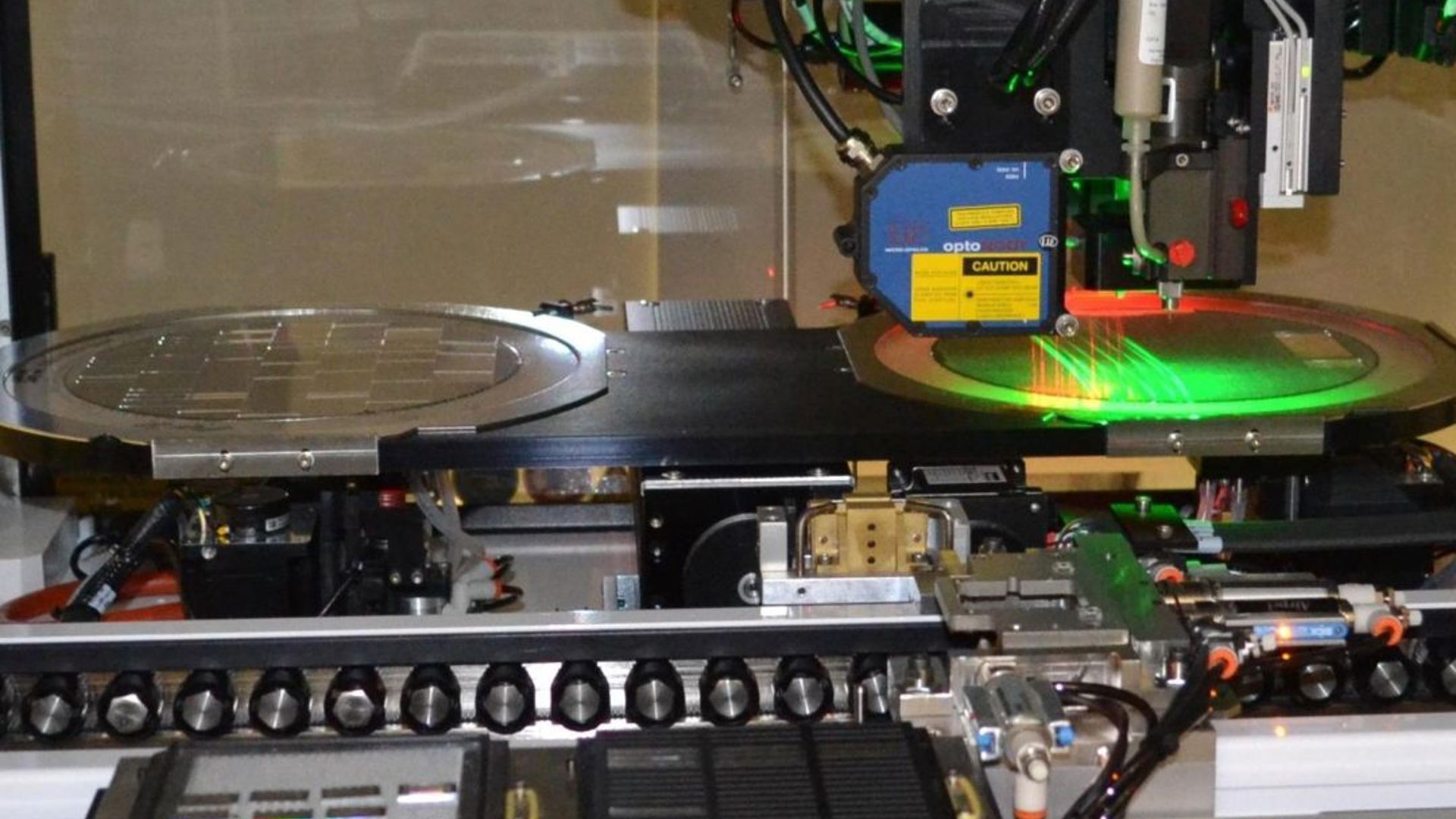
This post concentrates on the very specific requirements that customers must demand from their die attach systems, given this high-volume manufacturing environment:
- throughput and accuracy,
- handling delicate materials,
- the ability to handle a large and diverse component inventory,
- stability requirements of 24/7 operations,
- the scalability needs once demand takes off, and finally,
- the market requirements surrounding traceability of parts
1. Throughput and accuracy. Automation will always deliver higher levels of throughput compared with manual or semi-manual operations, in any sector. Specifically, in the world of die attach, automation can have 3x to 10x of throughput compared to its manual counterpart depending on the exact process. On the other hand, the throughput is only meaningful with achieved accuracy. With the technological advancement of component products and new processes, for example, silicon and InP photonics integrated circuit (PIC), we see the 5µm pick and place accuracy (±3σ, the current main stream) moving to requirements of 3µm (±3σ) accuracy or better, specifically in photonic and imaging applications.
2. Handling delicate materials. III-V materials such as thin GaAs, InP and GaN dies require delicate handling. The crystal facets on edge-emitting laser diodes, the top emitting surface of vertical-cavity surface-emitting lasers (VCSELs), and other active areas must not be touched by the bonding tools because the devices can be damaged. It is even more critical when flip-chip bonding is required. Because all GaN RF transistor die are typically very thin and have a large aspect ratio, the force and pressure control is crucial in picking and placing the die. It is very useful to have a real-time, closed-loop feedback in the force and height control when long term reliability is an issue.
3. Managing multiple parts with various sizes. Optical and RF applications frequently require handling a large range of devices from small to large as well as odd shaped. Many of the devices used in packages are small, including laser diodes and monitoring diodes. Thin metal preforms must be oriented and delicately handled. These preforms are tedious to manually handle. Increasingly extreme aspect ratio devices are used for arrays. These devices can have an aspect ratio as extreme as 15:1. The housings may also be odd shaped, with small housings of large packages with protruding connectors and pins. Flexibility is key for an automatic machine to be able to perform a variety of die attach processes on one platform. The ability to handle many component types from 150 micron diodes to large odd-shaped lids and attach them eutecticly, with epoxy or with thermocompression, is a tremendous advantage over manual or semi-automatic assembly.
4. Stability. Volume manufacturing often requires 24/7 operations or overnight operation with minimal operators. The automatic equipment stability becomes critical in order to avoid or minimize errors and thus loss of materials and productivity. The system stability can be tested through rigorous steps, but more importantly, the platform needs to be proven in the field. A reliable automation supplier with competent local technical services and expertise in photonics, microwave and RF applications is key for success.
5. Scalability. In today’s dynamic market, it’s not just about being first to market, but it’s also about having the capability to scale quickly and safely when higher volume is demanded. How quickly can your manufacturing partner scale production? Increasingly, product cycles are measured in months rather than years. Markets change quickly demanding that all vendors in the supply chain react quickly. It is important to have a product and a process that is scalable, because it often makes a difference between the vendors who dominate and those who do not. Short product cycles mean frequently changing production lines. Manufacturing systems need to be suited for dedicated high- volume manufacturing, yet flexible enough to allow small lot production and changeover between designs.
6. Traceability. Traceability is required for device tuning and component selection at integration. For these reasons, it is important to track individual die lot and serial number information with the serial number of the device being built. Manual record keeping of this pedigree information can be time-consuming, tedious, and vulnerable to human error. Automation equipment must continually compile information and export to log files for later inspection. This should enable all relevant information to be delivered with the completed product.
To examine how MRSI Systems meets these requirements, check out our product pages here.
For more information please contact us.