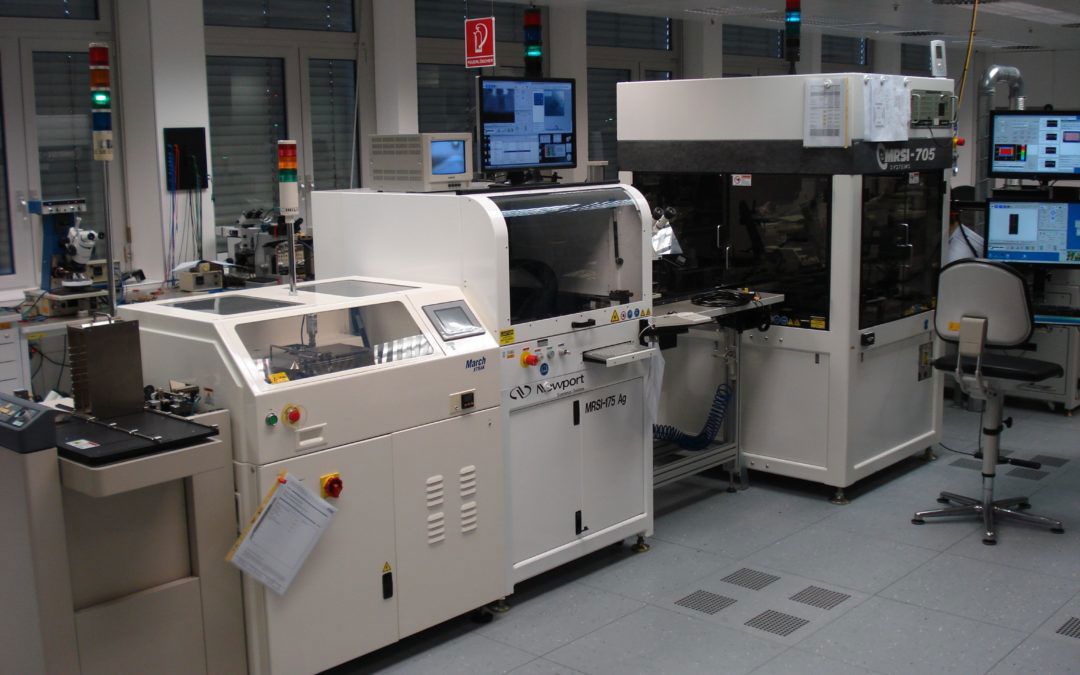
MRSI Systems Automated Microwave Hybrid Manufacturing at TESAT-Spacecom (TESAT)
Challenge
TESAT’s challenge was to develop an “Automated Microwave Factory” to manufacture complex highly integrated LTCC microwave modules within the frequency range 2 to 77GHz, 24 hours per day including a manless overnight ghost shift. TESAT wanted a high volume, high reliability, fully automated production line to build complex microwave modules with minimal labor required for competitive terrestrial products as well as for the commercial satellite market.
Solution
A team consisting of seven highly experienced engineers and technicians was put in place. Major tasks and responsibilities of the team were rapid prototyping, industrial engineering, development of assembly and test processes, development of advanced manufacturing technologies, and last, but not least, high volume series production.
By reducing the number of process variables to the very minimum and developing a series of robust assembly processes like plasma-cleaning, epoxy dispense, pick and place, eutectic die attach, wire-bonding, automatic optical inspection and electrical test, the team was able to ensure that all products were perfectly set up for automated series production. The next step was choosing an appropriate die bonder and epoxy dispenser vendor. MRSI Systems was awarded the contract to supply the MRSI-705 die bonders and the MRSI-175Ag precision epoxy dispensers to form an integral part of TESAT’s production process. The reasons behind this decision included:
- The MRSI-705, 5 micron epoxy and eutectic die bonder, is ideally suited for dedicated high volume production requirements, yet flexible enough for small lot production. The systems key features include a large configurable work area, delicate force control, advanced machine vision, programmable multi-color lighting and automatic tool changing.
The MRSI-705 is ideally suited to meet application-specific needs. The system at TESAT is configured with waffle pack and Gel-Pak inputs, automatic material handling, eutectic die bonding, epoxy stamping and inline surface topography scanning.
- The MRSI-175Ag, precision epoxy dispense system is specifically designed for demanding conductive and non-conductive applications, such as microwave circuit manufacturing. The system’s key features include a large work area, advanced lighting and vision alignment, laser height mapping, automatic needle alignment, purging and cleaning. The system at TESAT includes dual positive displacement dispense pumps, a jet valve and a shared common graphical user interface (GUI) with the die bonder.
- Both systems are equipped with a confocal height sensor which provides a surface topography scanning capability. On the die bonder this new feature is applied for inline topography scanning of the placed die with respect to die coplanarity, bond-line thickness, adhesive fillet height and debris detection on top of the die. Data goes into an advanced traceability system. On the dispenser the confocal height sensor is used for general height measurement (distance of nozzle to substrate surface) and for measuring and reporting the volume of epoxy dispensed.These features combined with material traceability and the ability to store an image of each dispense- or placement element provides advanced inline process control (IPC) as well as mass data for statistical process control (SPC). Both represent also valuable quality control information and replace manual visual inspection.
Results
A workforce of seven highly experienced engineers and technicians using the MRSI systems provide an annual capacity of about 2.1 million microwave placements. Existing production capabilities are also ideally suited for high volume production of T/R modules in X-band radar applications. Existing production experience is 67,000 highly integrated TRX-RF-modules using LTCC multilayer technology and includes attach of roughly 890,000 GaAs- & GaN-MMICs. First pass yields are well beyond industry standards.