Challenges in Die Bonding of Gallium Nitride High Power Devices
The gallium nitride (GaN) device market is rising at a compound annual growth rate of (CAGR) of 17.1% according to Mordor Intelligence, implying a rise from $711m to $1.8 billion by 2023.
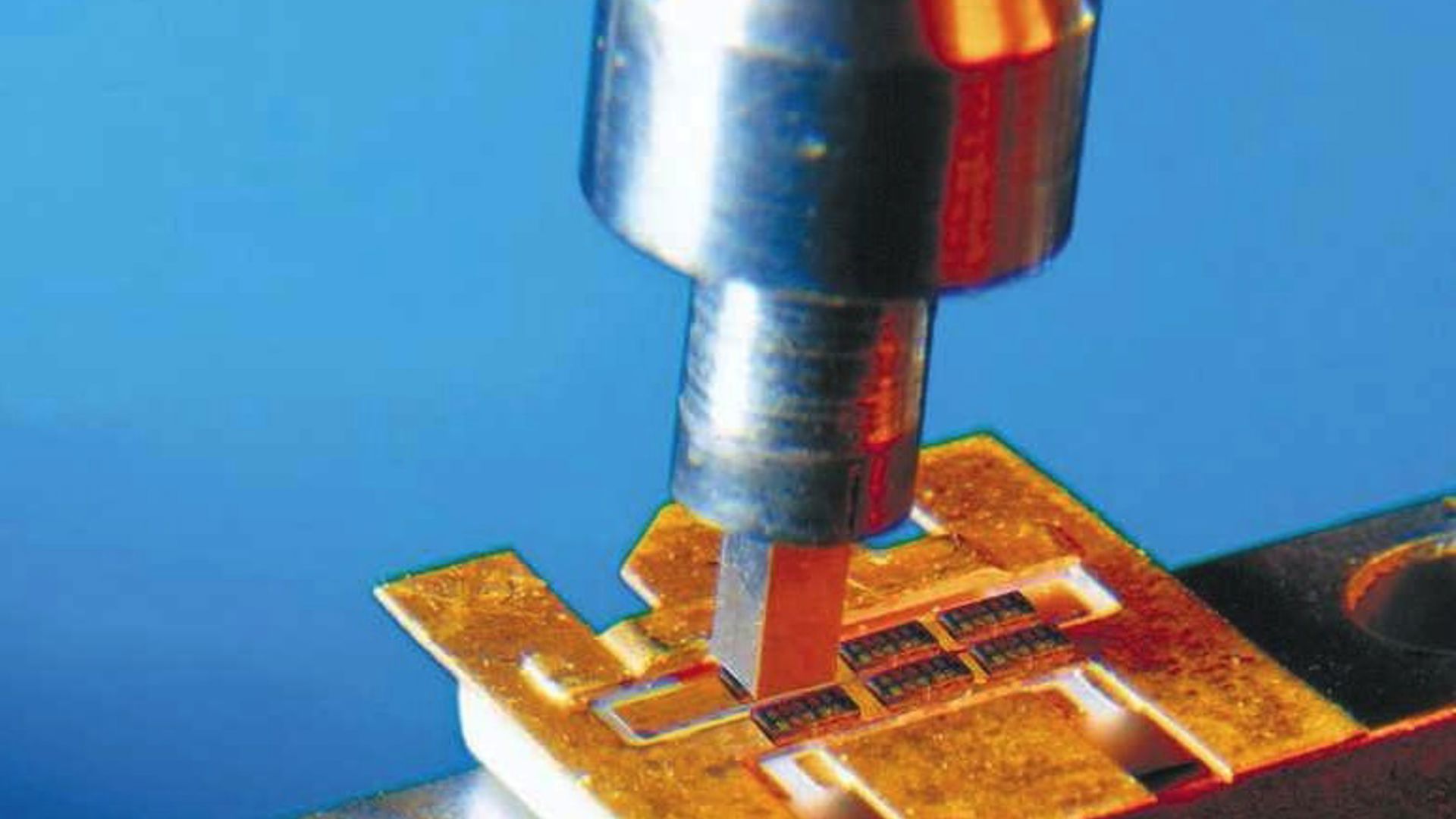
Gallium Nitride (GaN) materials have long been regarded as great alternatives and enhancements to gallium arsenide (GaAs) and silicon-based counterparts for applications demanding high power and high frequency performance. Historically GaN adoption has been hindered partly due to high production costs however with the explosion of new industries requiring radio-frequency devices, the price of GaN technology is expected to continue to fall. We are starting to see accelerated adoptions of GaN materials not just in traditional applications, such as RF power amplifiers for wireless base-stations, but also to enable chip makers to reduce the cost of integrated circuits, driving broad adoption among semiconductor manufacturing companies. Industries driving adoption include, phones, tablets, drones, industrial robots, and automotive applications including electric vehicles. These GaN based devices offer unique challenges in the manufacturing process.
GaN devices have the potential to deliver much higher power, at reduced device sizes than silicon or GaAs. Consequently, it is much more challenging to handle the heat that the GaN die generate. It is critical to improve die bonding techniques to help dissipate the heat out of the GaN die to the heat sink with an overall consideration of performance, reliability, and cost.
Typically, there are two major types of packages for GaN power devices: metal-ceramic and plastic. Metal-ceramic air-cavity packages are the choice for very high power applications, where hermetical sealing is required for reliability. The joint between the die and the heat sink is typically gold tin (AuSn) solder using a eutectic die bonding technique. During the eutectic die bonding process, special care needs to be taken to achieve a thin, uniform, and void-free eutectic interface between the die and the heat sink to dissipate heat effectively and uniformly for both power and reliable performance. This requires a die bonding system to have an accurate and uniform eutectic reflow temperature control for the whole bonding area, and accurate force control during reflow time. A parallel process, such as in-line progressive heating is very helpful in reducing total cycle time and thus increasing production throughput.
For cost-sensitive applications, plastic packages are used. The die bonding material is usually epoxy, which needs to be dispensed on the heat sink prior to die attach. These steps are followed by a thermal curing step. It’s important to note that thermal conductivities of traditional epoxy materials are not as effective as solder materials for eutectic die bonding, so operating power levels are limited in the plastic packages. Recent advances in new materials using sintering of multiple particles of silver, gold, and copper have shown significantly improved thermal conductivity. A plastic package using this new bonding material can potentially operate at much higher power levels. The sintering materials can be dispensed as traditional epoxies. Similar to eutectic die bonding, a thin, uniform, and void-free interface between the GaN die and the heat sink is essential for an epoxy die attach process. This requires die bonding machines to have accurate and uniform dispensing capability, as well as delicate bond force control.
In summary, GaN materials are superior to Silicon and GaAs for high power devices and other targeted applications. Adoption rates will continue to accelerate driven by innovation and cost reductions. MRSI is experienced with the two major types of packages for GaN power devices: metal-ceramic and plastic. By deploying eutectic die bonding for metal-ceramic packages and epoxy die bonding for plastic packages, MRSI has completed hundreds of installations. In addition, because of MRSI’s unique technology and configurable platforms, customers have enjoyed improved throughput, including reduced eutectic die bonding cycle times, and automated in-line material handling systems with parallel loading and unloading. Some customers have gone even further to optimize their production process by using MRSI’s integrated epoxy dispensing system, which works seamlessly with all of our die bonding systems.
Please contact Sales for more information about our die bonding and epoxy dispense solutions.