Multiple Die Eutectic Bonding
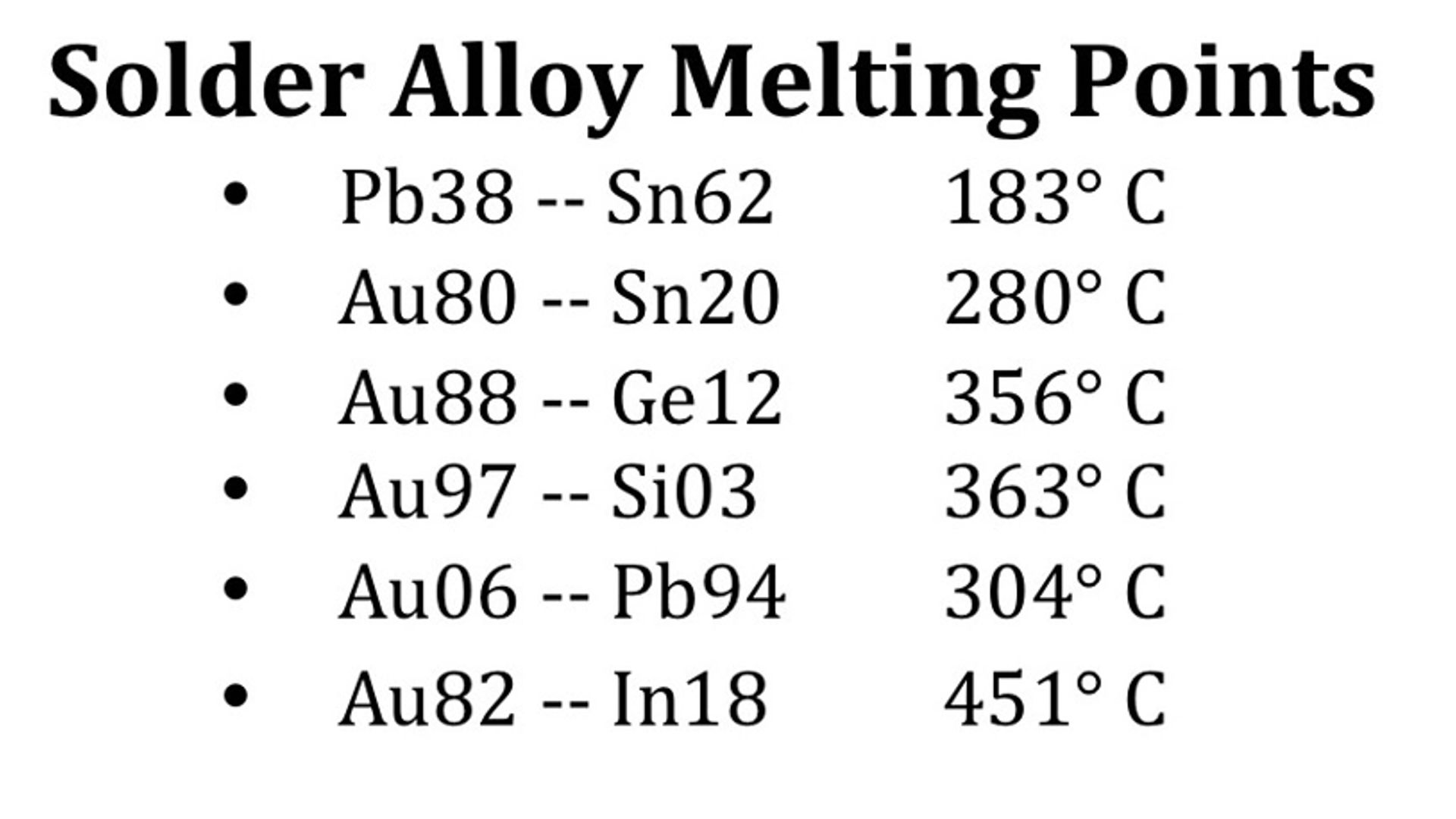
Table 1. Different metal compositions have specific reflow profiles for eutectic die bonding.
An introduction to Successful Applications
The word “eutectic” originated from the Greek word eutektos that means, “easily melting.” In chemistry, eutectic means relating to or denoting a mixture of two substances that melt and solidify at a single temperature (the eutectic point) lower than the melting temperature of the separate constituents or of any other mixture of the two. The term eutectic bonding is used to describe the use of a solder alloy to form a continuous bond between two components.
The placement of a semiconductor device onto a substrate or a board is referred to in the industry as die placement, die attach, or die bonding. Although the objective is the same, process and equipment configuration vary greatly in attaching the die to the substrate depending on the application, the assembly method, and the method used in interconnecting the die or chip within the package. A widely used method of die placement, particularly for the military and telecommunications industry, is by the formation of a eutectic bond.
Eutectic bonding is used as an alternative to epoxy bonding. The choice of eutectic bonding is determined by the application and the technical requirements. Specifically, for space and photonic applications, eutectic bonding is used to avoid the outgassing of epoxies. For high power devices, eutectic bonding is used to handle heat dissipation.
Photonics Devices
Some advanced photonics devices require multiple die, bonded on a submount or carrier. These are attached with eutectic bonding for a range of purposes, such as high thermal conductivity, high reliability, and special hybrid integration. A more complicated tunable laser chip on a carrier may include other additional components, such as a capacitor for bandwidth optimization. Sometimes other mechanical components for fiber alignment may also need to be bonded through eutectic die bonding on the same carrier where the laser sits.
Eutectic Die Bonding Stage
The eutectic bonding stage or eutectic die bonding site is usually a flat anodized aluminum plate with holes for vacuum to hold parts to be assembled. A plate is heated underneath the heating elements. The thermocouple and the heating elements are connected to a programmable temperature controller unit on the system. The gas mixture of nitrogen and hydrogen is introduced to the eutectic die bonding stage through a plumbing, installed close to the sides of the hot plate. To form a blanket of the nitrogen-hydrogen gas, a removable cover made out of metal such as aluminum is installed over the eutectic die bonding stage such that an enclosed heated chamber is achieved. The metal cover has a hole, usually a rectangular shape, that is large enough to fit the parts to be assembled.
Typical Eutectic Die Bonding
Applications requiring some degree of die placement accuracy use a machine vision system before picking a die or component from its carrier, and before placing the part to the substrate or package. The eutectic die bonding site should be pre-heated to a temperature just below the eutectic point of the preform material. The hot nitrogen-hydrogen gas mixture should be flowing in the covered eutectic die bonding site.
A typical eutectic die bonding process begins with the placement of the substrate to the hot plate or bonding site using a flat-faced pickup tool. The preform, such as gold-tin or gold-germanium alloy is placed on the heated substrate using a pickup tool. The die is then placed with controlled force over the preform using a collet and the temperature is quickly raised to the re-flow temperature.
Automated Eutectic Die Bonding System
The automated system for eutectic die bonding should be able to perform gold-silicon eutectic as well as eutectic re-flow using a perform such as gold-tin and gold-germanium. It should have an efficient temperature control in bonding components requiring different re-flow temperatures within a single package. It should also provide an inert gas atmosphere during the eutectic die bonding process. A stable motion (robotic) system, regardless of variations in operating temperature and humidity, and a robust vision system are needed to pick and place parts with high precision. The system should be able to handle parts of various sizes and shapes, and be gentle enough so as not to break or damage parts made out of delicate material like gallium-arsenide (GaAs).
Eutectic Bonding Temperature Control
In order to achieve the bonding of multiple parts within a package, a temperature hierarchy is sometimes required. To achieve this temperature hierarchy, fast ramping heated workstations are used. There are many reasons for a temperature hierarchy. For example, a monitoring diode may need to be attached with eutectic bonding to a spacer at one temperature (for example gold-germanium at temperature Y) and the subassembly (monitoring diode and spacer) may then need to be bonded to a substrate using a lower temperature solder (for example, gold-tin at temperature X). The substrate may then need to be mounted to a package utilizing a lower reflowing solder (e.g., lead-tin at temperature Z) (Table 1). This fast ramping is achieved by utilizing a low-mass hot plate.
As RF power amplifiers decrease in size, but increase in output wattage, the necessity of heat dissipation becomes more significant. These devices are almost always attached with eutectic bonding. The design of high frequency GaAs MMIC’s demands an extremely stable and conductive ground plane beneath the die, which can be achieved with eutectic bonding. Eutectic die bonding eliminates exposure to outgassing from organic conductive epoxies which affects the performance of most optical and laser devices.
Fast ramp rates are achieved with advanced ceramic plates with integrated heaters and vacuum holes to hold parts to be assembled. The thermocouple and the heating elements are connected to a programmable temperature controller unit on the system. The gas mixture of nitrogen and hydrogen are controlled by valves and gauges that regulate the atmosphere. To form a blanket of the nitrogen-hydrogen gas, a removable cover is installed over the eutectic bonding stage so that an enclosed heated chamber is achieved. A retractable shutter can be used to reduce the size of the hole in the cover. This enables the eutectic bonding stage to be used for large packages while still maintaining good gas control.
In summary, eutectic die bonding is an essential element in high volume manufacturing of advanced photonics devices. MRSI Systems designs and manufactures a family of products that automates the eutectic bonding process and delivers a stable, reliable, accurate and fast production process for customers.
For more information please contact us: sales.mrsi@mycronic.com, +1 978 667 9449