共晶贴片
共晶贴片(有时称为共晶贴片粘结)是用于需要增强散热的装置(如高功率放大器)的贴片技术。当涉及传统贴片环氧树脂的释放气体时也使用此技术。金锡、金锗和金硅是三种常见的共晶合金。简而言之,通过将封装或基片放置于可受到热控制的表面上或将封装或基片移动到该表面来自动实现共晶贴片工艺。然后自动化系统将焊膏和模片按顺序放置于基片上。之后急剧升温,实现回流。在理想情况下,由于产能和质量的原因,迅速进行温度剧变。工艺必须在惰性环境中进行,避免氧化。使用称为擦洗的技术可以实现无空隙粘结。下面我们将详细介绍共晶贴片工艺,包括使用同时加工多个部件的联机方法的自动化系统。
共晶贴片被定义为使用中间焊料合金在两个表面之间形成连续粘结的工艺。共晶贴片是一种贴片技术,主要用于针对标准贴片粘结材料进行释放气体敏感的气密封装。例如,在光电子应用中,这通常意味着两个镀金表面通过铅锡、金锡或金锗焊料接合。为实现该粘结,一般将焊膏放置于一个元件(通常为载体或基台)上;然后使第二元件(通常为微波装置、光探测器或激光芯片)对接焊膏。通过加热组件放置的基底,或通过使加热的气体流过组件使组件的温度升高到正好高于焊料的熔点。正如焊料液化,通过适当的力放置芯片。使部件冷却到回流温度以下并完成共晶贴片。根据装置类型和构造,可以在放置过程中使用擦洗。使用共晶组合物使共晶贴片工艺温度降至最低,如图1所示。
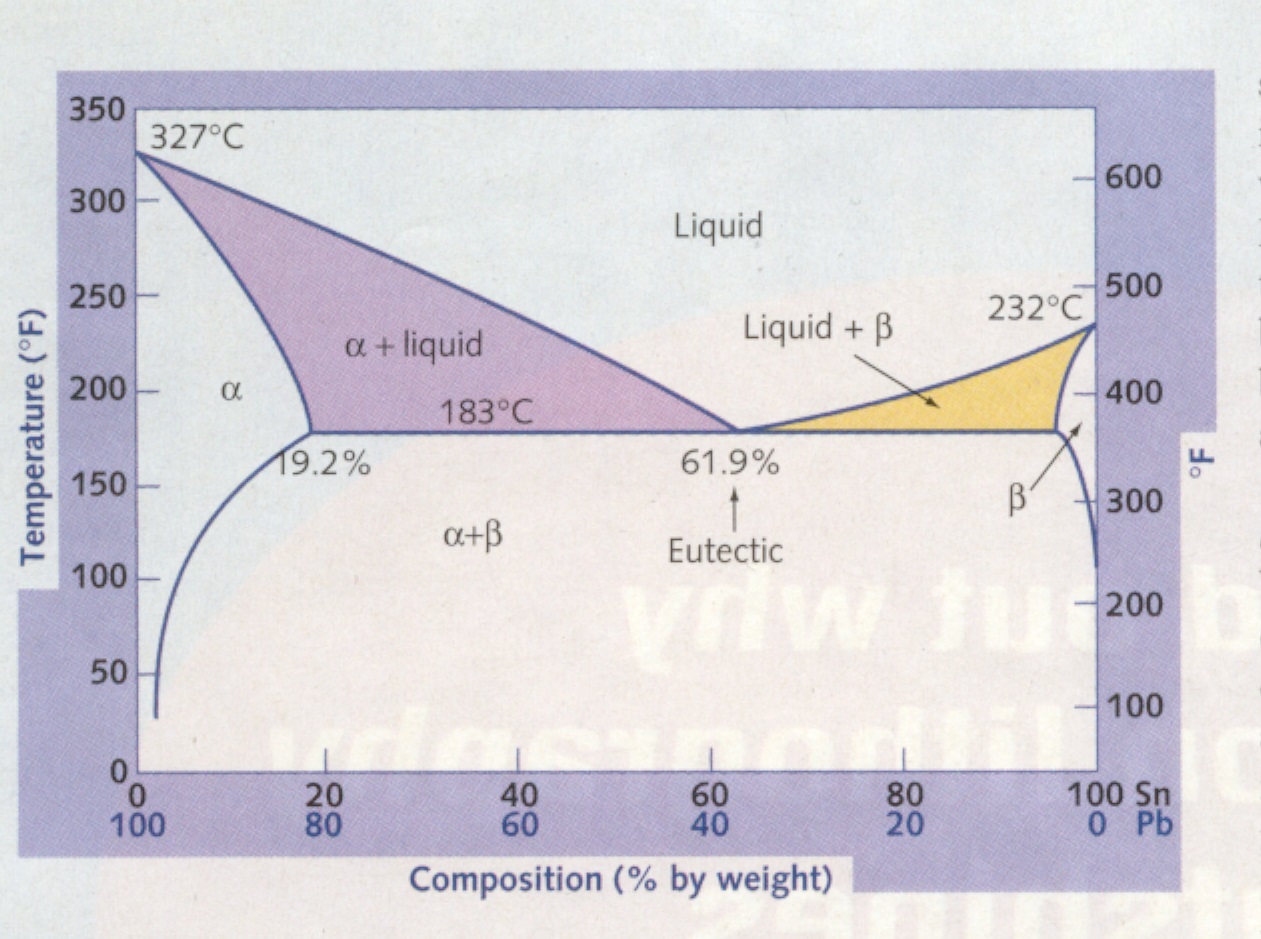
图1:给定金属组合物(在本例中是锡铅)的共晶转变
擦洗步骤包括在装置放置到基片期间将垂直和侧向力同时施加到装置。芯片通常沿负向移动三至五密耳 (0.003–0.005″),然后沿x轴或y轴方向进行类似但正向的移动;重复该步骤几回。还可以沿另一个方向移动。有时采用旋转擦洗。擦洗参数包括x、y和θ方向的振幅、速度和频率。参数由工艺要求确定,如芯片的表面积或载体的质量以及工艺限制(如邻近模片的接近程度)。在三种材料中,擦洗是常见材(粘结)形成的关键工艺步骤。挤出空气会减少空隙。另外,焊料更好地分布于模片上,压力有助于扩散过程。
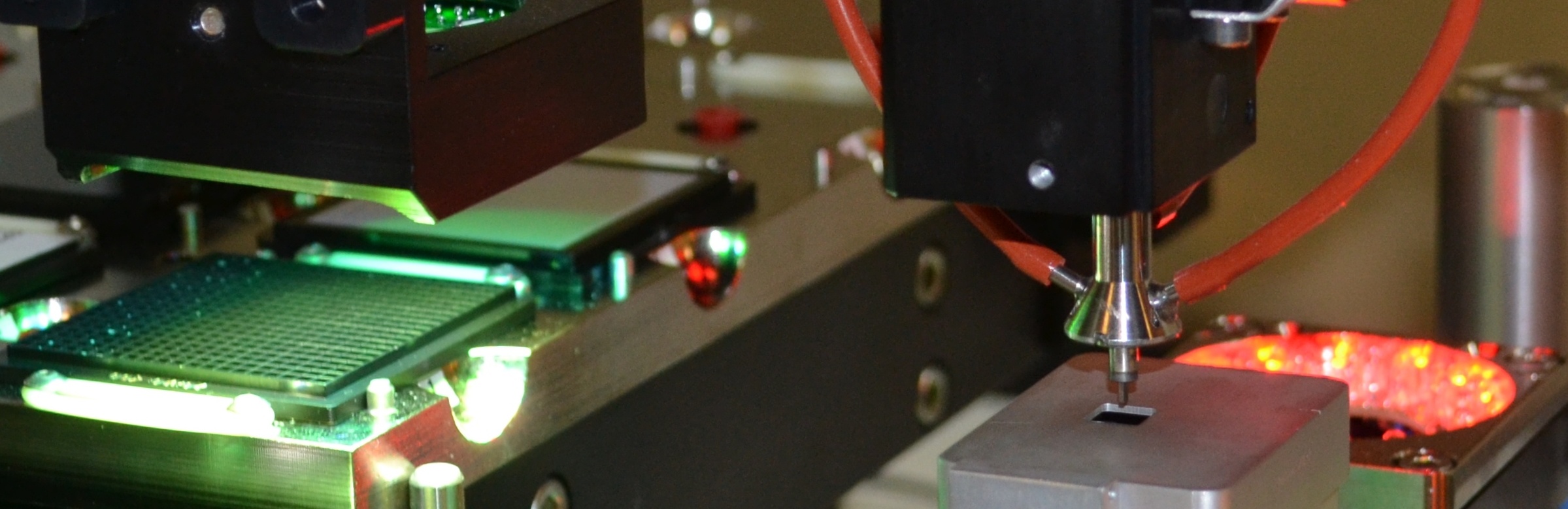
快速匝道共晶粘合阶段
在部件受热期间,控制其中焊接过程的进气至关重要。共晶贴片通常在惰性环境中进行,防止粘结表面氧化。可以使用90–95%氮氢混合气,使其中的氢气用于形成粘结(图2)。
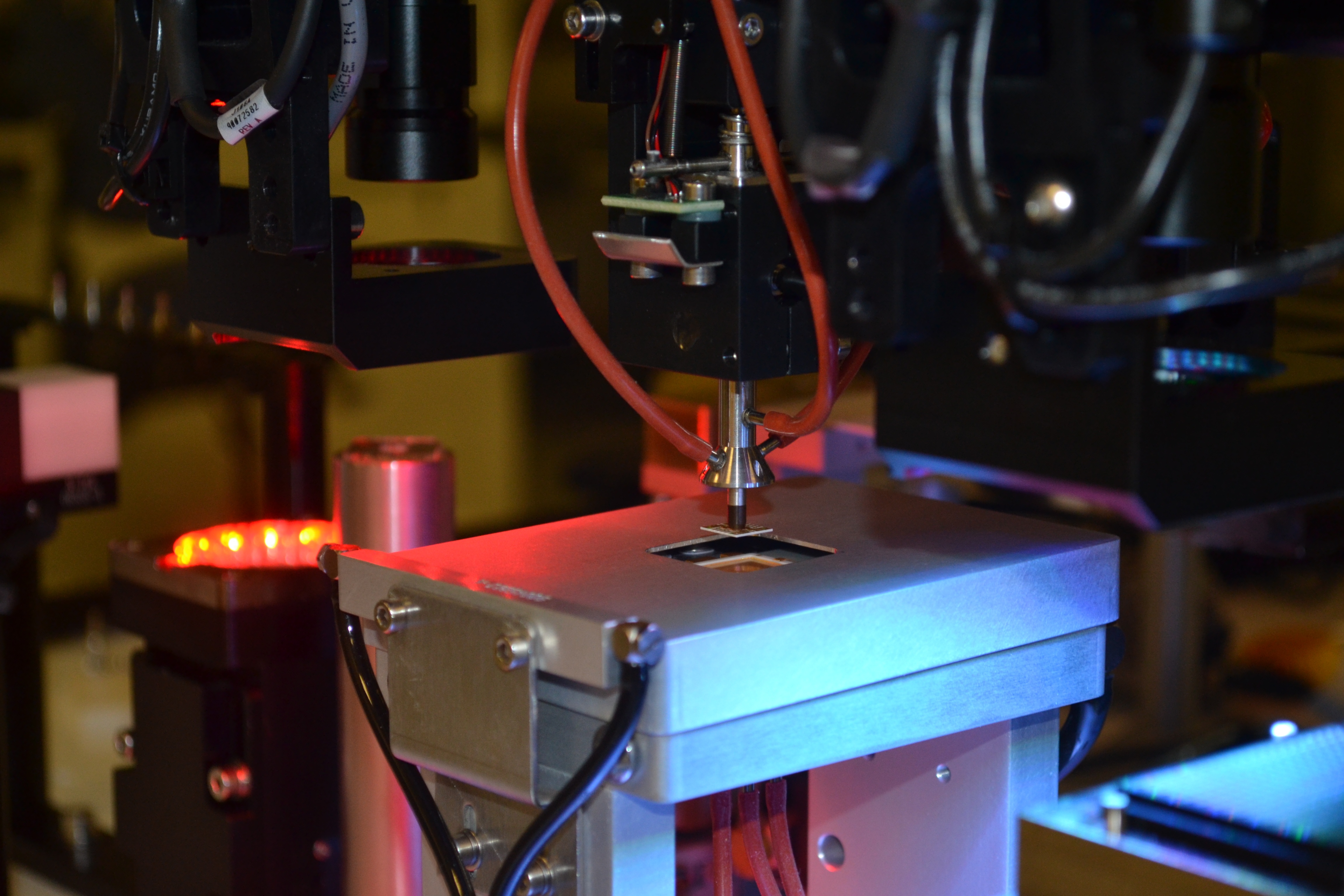
图2:脉冲加热快速温变共晶阶段
从设备制造商的角度来说,管控共晶贴片工艺涉及多个关键要素和工艺。其中包括:准确控制装置温度的功能,准确控制接触力,精确控制用于破坏氧化物的擦洗操作,引入能量以便使温度骤升并混合焊料中包含的各种金属,提供具有保护气体的惰性气体或具有保护气体的助熔剂,以及控制冷却和筒夹。用于共晶贴片工艺的材料组合将决定用于共晶贴片的温度。
联机共晶贴片提供了实现高产量的方法。通过利用在热区域中关联的渐进热板系统,可对在“船体”或载体中运输的部件进行共晶贴片,该“船体”或载体会自动装载、加工和卸载到盒。通过在预加热、组装和后加热区域中关联部件可以严格控制温度。通过每个热区域的温度曲线,可以快速加工具有高热质量的部件。通过限制共晶贴片工位处的温度剧变时间能够实现高产能。所有温度区域均在保护气体下,该保护气体由氮氢混合气组成,用于防止加热部件的氧化(图3)。

图3:在保护气体下的联机共晶贴片
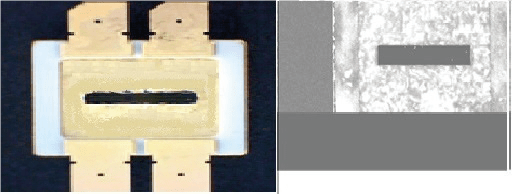
图4:共晶封装(左)和Sonoscan检查结果(右)
对于焊料回流共晶贴片(如砷化镓 (GaAs) 和氮化镓 (GaN) 模片的金锡 (Au/Sn) 粘结),系统会校准封装,然后拾取焊膏并放置于加热的封装上(如果需要,可以预先放置焊膏)(图4)。要进行回流,需拾取模片并放置于其所需放置的位置,并且擦洗,同时通过脉冲加热共晶贴片阶段使共晶贴片位置处的温度升高。
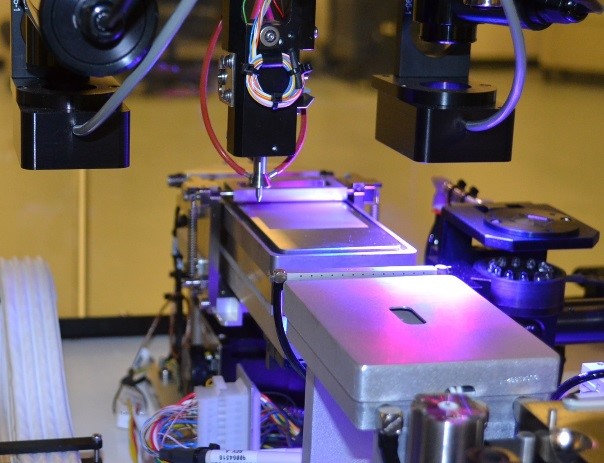
独立共晶连接