From ping-pong to perfection
Enhancing the art of inspection programming with Escape TrackerIt’s sometimes called the ping-pong effect: the back-and-forth task of adjusting 3D inspection models to eliminate false calls without increasing the risk of escapes. Thanks to a new automated programming assistant, all this work can now be put to better use. Every time you certify a real defect or false call, it remembers, constantly updating your inspection library based on real production data. The result is an inspection process that automatically moves closer to perfection every time it’s in use, saving programmers time, effort – and their most valuable resource of all – concentration.
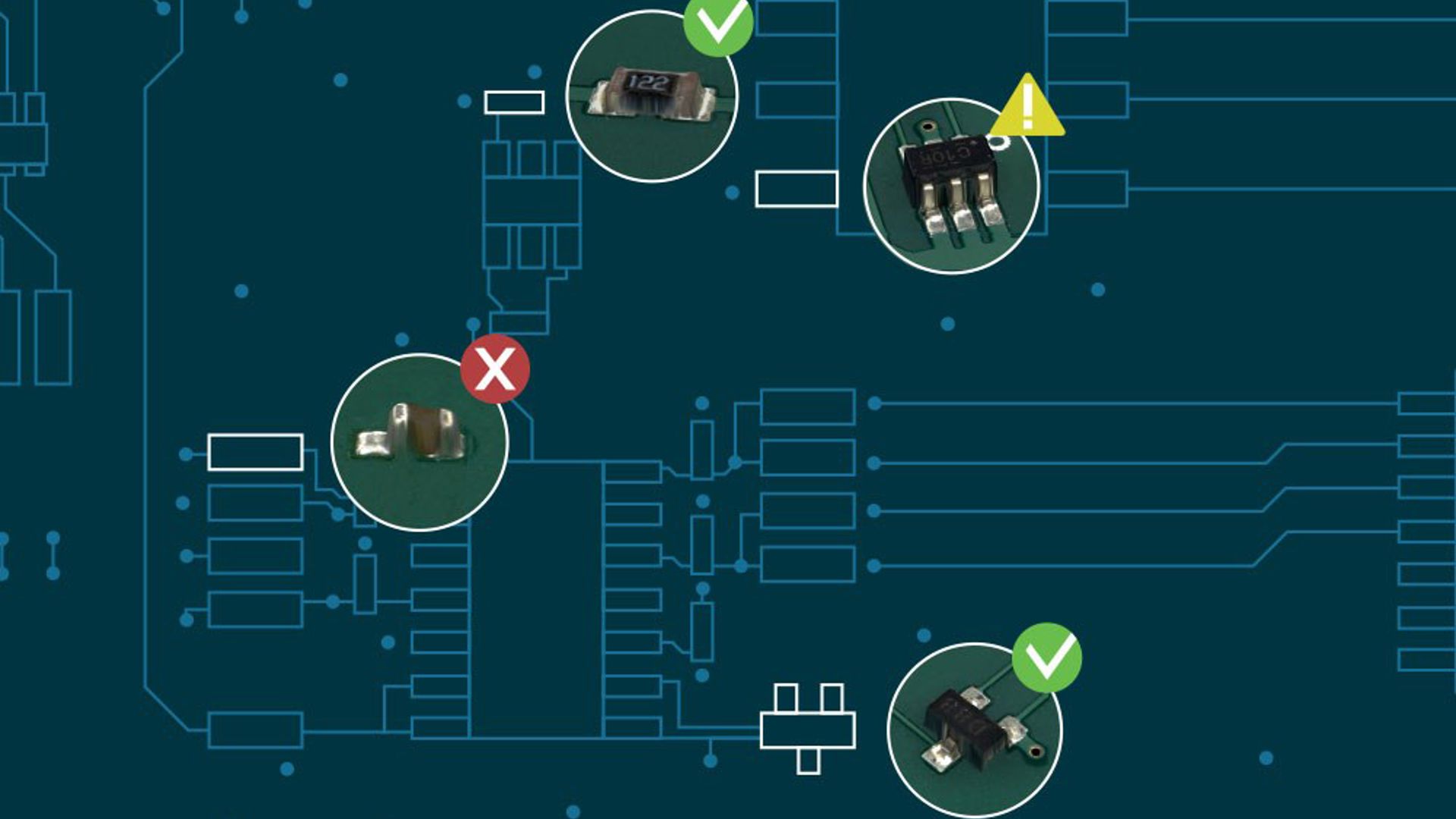
In the pursuit of the perfect inspection model, program fine-tuning can often feel frustrating. Tighten tolerances too much, and the false calls proliferate. Open them up, and new escapes arise. Each modification and every review can have these spin-off effects – not exactly the best use of a programmer’s time and attention.
With Escape Tracker, now there’s a way to improve inspection models over time with no added programming steps. During program fine-tuning, the software effectively runs a background check. Automatically collecting review images. Checking modified parameters against certified inspection data. Hundreds of times per second, it updates the baseline for your entire inspection library, bringing what began as an ideal inspection model closer and closer to the realities of previously manufactured and inspected components.
A more comprehensive quality check
Escape Tracker represents the latest evolution of Mycronic’s industry-leading Library Pro: a powerful inspection library that stores and optimizes a unified database of every inspected product. The major advance with Escape Tracker is its ability to continuously perform non-regression control of the central library’s performance. This gives the software a comprehensive overview of previous production, making it possible to cross-check program settings across products, rather than solely against the current production batch as is common practice today.
Step 1: Once the program has been created, Escape Tracker checks that the latest adjustments made to each inspection model for each type of component will still detect the previously known true defects and will not generate any false calls. In this example, it appears that one true defect is potentially undetected, and five false calls may appear during production.
Step 2: Based on the information provided by Escape Tracker, the programmer makes the necessary corrections to the inspection model of the related component. Often it is a matter of adjusting tolerances.
Step 3: Once the corrections are made, Escape Tracker performs a new efficiency check of the inspection model against known real defects and potential false calls. In this example, the green check marks indicate that all potential issues have been fixed for that component family.
Beyond the golden board
This ability to cross-check a program for a particular component against all historical inspection data marks a significant advance in 3D inspection. In the past, a so-called “golden board” – an ideal finished board – might be used to check the system’s inspection settings. The only problem, of course, is that in the real world of product variations, changing component and PCB suppliers and physical limitations, the ideal mounted component never existed.
No silver bullet
To accommodate for production drift and other changes, many industries solved this problem with a “silver board”, a board with known defects used to periodically re-calibrate inspection settings. Over time, however, even these boards tend to gather dust, oxidation and increasing wear to grow less and less accurate with every use.
A new era of self-regulated inspection
Escape Tracker, together with the advanced software guidance of the MYWizard user interface, makes it possible to move 3D inspection beyond these limitations. By bringing the art of a programmers’ judgement together with the objective reality of every mounted and inspected component, the system automatically adapts to the natural variations of changing production conditions. Making inspection models more robust, programming more efficient and end products closer to perfection, every minute of every day.
Some examples of real defects stored in the system used by Escape Tracker to control the efficiency of a new program:
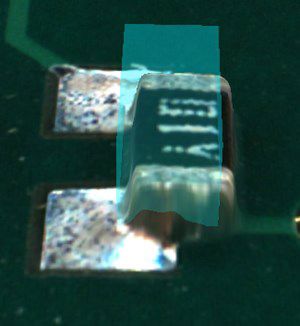
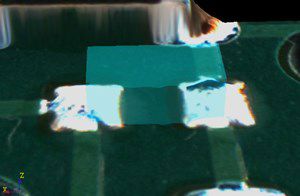
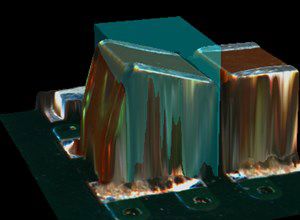
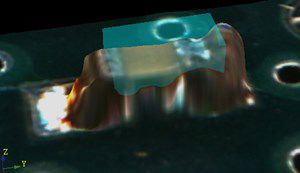